HOWO Front Connecting Crossmember Assembly WG1664160495
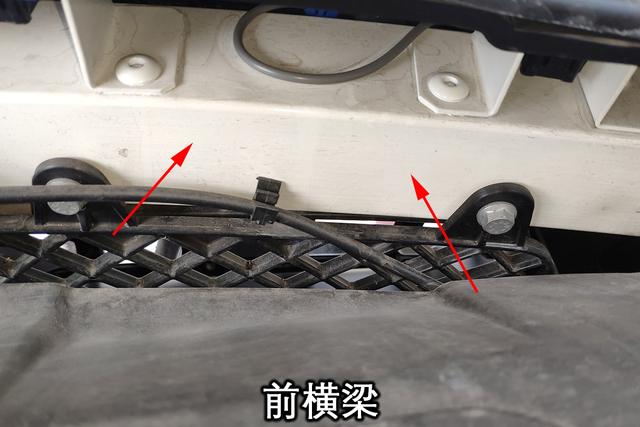
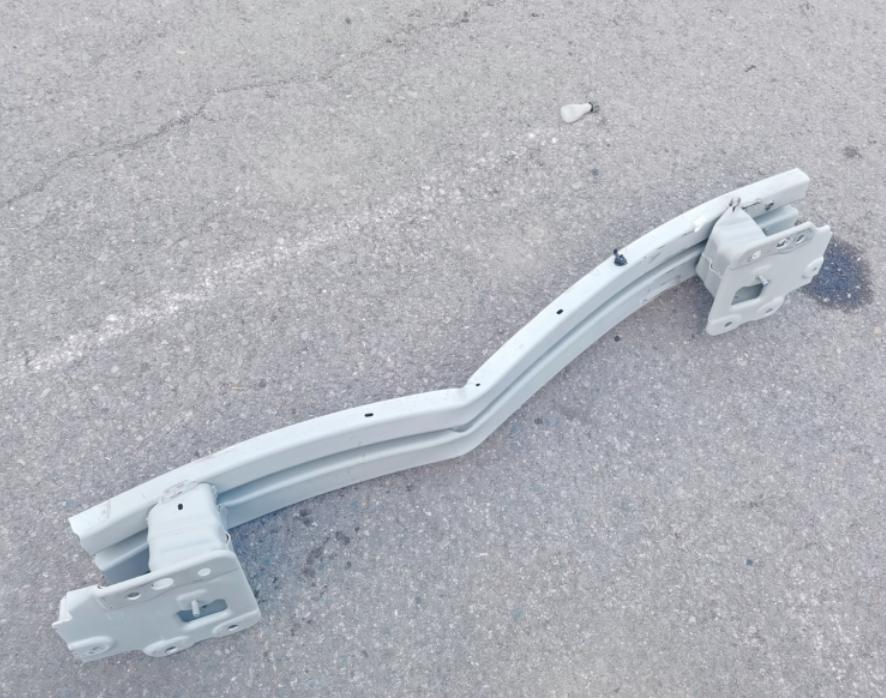

The Front Connecting Crossmember Assembly WG1664160495 serves as a critical structural reinforcement component specifically engineered for HOWO heavy-duty trucks. Manufactured to stringent OEM specifications, this crossmember assembly provides essential support to the cab mounting system, ensuring optimal weight distribution and structural stability. Its precise engineering allows seamless integration with the existing cab framework while maintaining correct chassis alignment under demanding operational conditions. Through rigorous material selection and production techniques, HOWO has developed this component to deliver reliable load-bearing performance throughout the vehicle’s operational lifecycle.
Engineered for the extreme demands of heavy transport operations, this crossmember features corrosion-resistant steel construction with precisely calibrated thickness specifications. The component’s geometry incorporates strategic reinforcement ribs along key stress points, significantly enhancing fatigue resistance during prolonged highway operation. When installed correctly, it creates a unified structural bridge between the primary cab mounts, effectively minimizing chassis flex during cornering maneuvers or uneven terrain navigation. Vehicle operators report notable improvements in cab stability and reduced vibration transmission after installation, particularly when transporting maximum payloads over extended distances.
Dimensional accuracy remains paramount in crossmember assembly design. The WG1664160495 maintains tolerances within 0.5mm across all mounting interfaces, guaranteeing perfect alignment with factory bolt patterns on applicable HOWO truck models. This precision eliminates potential stress concentrations that could develop from misaligned components. Furthermore, all welding joints undergo non-destructive testing procedures to ensure uniform material fusion without compromising the structural integrity of the base material. Such meticulous attention to manufacturing consistency translates directly into extended service life and reduced maintenance requirements for fleet operators.
Installation efficiency represents another significant advantage of this OEM crossmember assembly. Precisely positioned mounting holes align perfectly with existing cab bracket interfaces, enabling straightforward replacement procedures without chassis modification. The component arrives with pre-applied anti-corrosion coatings and protective finishes that withstand prolonged exposure to road chemicals and environmental elements. This surface treatment system actively prevents oxide formation throughout the assembly, maintaining critical structural properties even after years of intensive service in harsh climates.
Operational safety directly correlates with crossmember integrity in heavy vehicles. When fatigue develops in compromised assemblies, it can manifest as subtle cab misalignment that gradually progresses to detectable handling issues. The WG1664160495 prevents such deterioration through its high-strength material composition and engineered load distribution properties. The component effectively transfers operational stresses away from critical suspension points, maintaining consistent vehicle dynamics even under maximum payload conditions. Fleet maintenance managers consistently prioritize genuine crossmember replacements when addressing cab stability concerns due to their predictable performance characteristics.
Compatibility verification remains essential for crossmember assembly applications. The WG1664160495 interfaces exclusively with designated HOWO truck series manufactured between 2018-2023 model years. Reference compatibility charts should always be consulted when replacing earlier model assemblies to ensure proper fitment. This precision compatibility ensures all safety systems, including airbag deployment timing and crumple zone effectiveness, maintain original equipment specifications post-replacement. Manufacturers always recommend using factory-trained technicians for installations to guarantee correct torque sequencing and system calibration.
Performance validation occurs through standardized testing protocols simulating decades of operational stress in compressed timeframes. Prototypes endured millions of dynamic load cycles representing highway miles while sophisticated sensors mapped material response. Data analysis confirmed uniform stress distribution below critical thresholds throughout the assembly. Such testing confidence allows component manufacturers to offer industry-leading warranty coverage periods unmatched by aftermarket alternatives. These validation procedures directly translate to reduced operational downtime and maintenance expenses for transportation enterprises.
Optimal vehicle geometry preservation represents a critical advantage of using factory crossmember assemblies. Aftermarket alternatives frequently lack the precision jig fixtures and measurement systems employed during OEM production. Even minor dimensional variances can subtly alter steering axis inclination or caster angles when installed. The WG1664160495 guarantees exacting alignment with factory specifications, preserving intended vehicle dynamics without requiring post-installation suspension adjustments. Professional installation combined with this precision component consistently restores original equipment handling characteristics.
Material technology innovation differentiates modern crossmember assemblies. The WG1664160495 utilizes micro-alloyed steel formulations with enhanced elasticity properties that accommodate cyclical loading without permanent deformation. This material intelligence allows the assembly to flex within designed parameters during transient dynamic events, then return precisely to its original shape without accumulating micro-fractures that initiate fatigue failure. Such advanced metallurgical solutions extend component service intervals well beyond previous industry standards while reducing overall vehicle weight.
Technical documentation accompanying every assembly includes detailed torque specifications for each fastener location, proper pre-loading sequences, and certified installation diagrams. Strict adherence to these guidelines prevents localized point stresses that could compromise long-term structural performance. Each component packaging features visible identification markings including the WG1664160495 designation and manufacturing traceability codes that document precise production parameters. This information streamlines warranty validation procedures should they become necessary.
Environmental considerations integrated into the manufacturing process include extensive scrap metal recycling and solvent-free coating applications. Production facilities implement closed-loop water systems and energy recovery technology to minimize ecological impact. The resulting component offers significantly reduced lifetime carbon footprint compared to previous manufacturing generations while delivering enhanced operational longevity. Such sustainability initiatives align with evolving transportation industry standards and corporate environmental commitments.