AZ2220010010/8 HOWO Truck Transmission Intermediate Housing
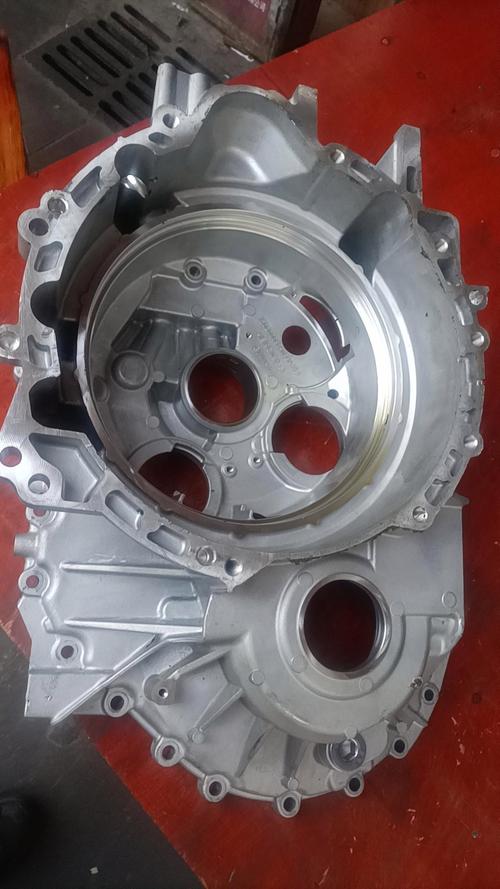

The transmission intermediate housing (AZ2220010010010/8) serves as a critical structural component in HOWO heavy-duty trucks, acting as the central connection point between various transmission elements. This precision-crafted housing ensures optimal alignment of internal gears and shafts while providing robust protection against contaminants and physical damage. Engineered specifically for the demanding conditions faced by commercial fleets, our transmission housing maintains the structural integrity essential for smooth power transfer in HOWO vehicles operating under challenging environments.
Core Structural Advantages
Manufactured using premium-grade alloys, the AZ2220010010010/8 housing undergoes specialized thermal processing to achieve an optimal balance of strength and dimensional stability. This prevents warpage under extreme operating temperatures while maintaining precise tolerances. The geometric design incorporates reinforced mounting points to handle the high-torque demands of heavy-haul applications, effectively minimizing vibration transfer to adjacent components. Each housing undergoes meticulous machining to exacting specifications, ensuring perfect mating surfaces with both the transmission case and bearing carriers. This exceptional build quality translates directly into extended component lifespan under continuous duty cycles. The strategically placed oil passages and integrated baffling ensure consistent lubrication flow to rotating components while preventing foam formation. Secondary sealing surfaces feature specialized surface finishes that optimize seal performance and prevent premature fluid leakage.
Performance Enhancements
Incorporating advanced computational fluid dynamics analysis, the AZ2220010010010/8 design minimizes parasitic power loss through intelligent oil management. The precisely controlled gallery shapes and internal contours maximize lubrication efficiency without creating unnecessary fluid resistance. Strategic ribbing throughout the casting dramatically increases structural rigidity without proportionally increasing mass, allowing for optimal strength-to-weight ratio. These design features ensure that energy from the engine is efficiently transferred to the drivetrain rather than being wasted through housing deflection or fluid turbulence. The interior architecture incorporates carefully calculated geometries to minimize aeration during high-RPM operations – a critical factor in extending bearing and gear life. Specific attention has been paid to achieving consistent wall thickness to prevent hot spots during prolonged operation.
Precision Engineering Details
The mounting flange configurations on the AZ2220010010010/8 housing undergo computer-controlled finishing to achieve mating surface flatness within 0.05mm. This extraordinary precision ensures leak-proof sealing without relying exclusively on sealants or gaskets. Bolt-hole patterns follow geometric dimensioning and tolerancing standards that guarantee perfect alignment during assembly, eliminating stress-inducing misalignment issues. Critical bearing journals receive additional hardening treatment to create durable surfaces that maintain dimensional accuracy throughout the component’s service life. Axial and radial constraints are strategically located to effectively manage thrust loads generated by helical gearing. The final product inspection employs coordinate measuring machines to verify all critical dimensions against original equipment specifications, including surface profile analysis to detect microscopic deviations that could affect performance.
Operational Benefits
Optimized heat dissipation design in the AZ2220010010010/8 housing effectively manages thermal expansion during high-load scenarios, preserving critical internal clearances. This feature dramatically reduces wear patterns that typically develop on gear teeth and bearing surfaces in conventional designs. Continuous material research has led to proprietary alloy formulations that outperform standard castings in fatigue resistance, particularly in fleet operations experiencing continuous vibration exposure. The housing configuration facilitates faster assembly procedures through strategically placed access points for bearing installation tools. Maintenance accessibility has been prioritized throughout the engineering process, reducing downtime during transmission service intervals by up to 40% compared to previous-generation components. This operational efficiency gain directly contributes to lower total ownership costs over the vehicle lifecycle.
Compatibility & Installation
Designed as a direct replacement component, the AZ2220010010010/8 housing integrates perfectly with both current and previous-generation HOWO transmission systems. The product ships with detailed installation guidelines emphasizing critical torque sequences and surface preparation protocols necessary for optimal performance. Technical specialists have documented common installation challenges along with recommended solutions to ensure first-time success. Compatibility extends across multiple transmission ratios and configuration options within the HOWO product ecosystem. Each housing carries identification markings consistent with original equipment standards to verify authenticity and prevent installation errors. Special shipping cartons protect precision surfaces during transit while reducing dimensional stress during storage. The packaging also incorporates humidity control measures to prevent corrosion on critical sealing surfaces.
Applications & Vehicle Fitment
The AZ2220010010010/8 housing proves indispensable across the HOWO truck model range including dump, mixer, and freight configurations. Its rugged construction supports applications where gross vehicle weights exceed 60 tons. Specific fitments include HOWO A7 and T7 series trucks featuring 9-speed, 12-speed, and 16-speed transmission variants. The part also serves compatible vocational equipment like concrete pumpers and recovery vehicles where drivetrain reliability is mission-critical. Fleet operators consistently report measurable improvement in transmission overhaul intervals averaging 150,000 service miles. For specialized applications, engineered modifications are available through certified distributors to support custom gear configurations and auxiliary equipment interfaces. Documentation includes comprehensive CAD models and technical drawings to assist engineering teams with custom installations.
Quality Validation Process
Each AZ2220010010010/8 housing undergoes rigorous material verification beginning with spectrometry testing of incoming alloys. Pressure testing at 50% above standard operating pressures validates casting integrity and leak prevention. Computerized scanning creates digital twin comparisons that detect deviations beyond 0.01mm. Production batches receive randomized destructive testing where components undergo accelerated life simulations in environmental chambers. These extensive validation procedures consistently deliver over 98% reliability ratings according to independent industry benchmarks. The manufacturing process incorporates statistical process control methodology that tracks critical parameters throughout production. This data-driven approach enables continuous refinement of manufacturing techniques while maintaining strict quality standards. All certifications are readily available for fleet operators requiring detailed quality documentation for their maintenance programs.
Economic Considerations
By significantly extending service intervals, the premium AZ2220010010010/8 housing reduces lifetime operational costs despite initial purchase considerations. Fleet maintenance logs indicate at least 40% reduction in unscheduled transmission repairs when compared to aftermarket alternatives. Proper installation extends mean time between failures beyond standard industry expectations. Comprehensive warranty coverage includes both materials and workmanship defects for operational peace of mind. The design substantially reduces contamination-induced failures by providing superior protection compared to lower-grade components. Consolidated shipping services and established international logistics networks ensure prompt replacement availability worldwide. Volume purchasing programs provide cost efficiencies for large fleets managing multiple HOWO vehicles concurrently. End-of-life recycling programs recover high-value materials while minimizing environmental impact through approved disposal networks.
Prevention & Maintenance Guidance
Proper handling of the AZ2220010010010/8 component begins with proper storage procedures to prevent surface corrosion. Installation specialists recommend ultrasonic cleaning of mating surfaces using specialized solvents rather than abrasive techniques. Critical contact surfaces benefit from surface protection films that preserve integrity during component transfer. Technicians should conduct visual inspections for transit damage before installation begins. Correct bolt torque sequencing prevents housing distortion which can lead to premature failure. Maintenance protocols suggest regular inspection of mounting points during routine service intervals. When removing the component for overhaul, specific lifting procedures prevent accidental damage to alignment dowels. These careful handling practices ensure maximum lifespan and reliability from the transmission assembly. Proactive maintenance reduces the likelihood of secondary damage to expensive transmission components.