WG1664160535 Driver Left Guard Panel Assembly for HOWO Truck


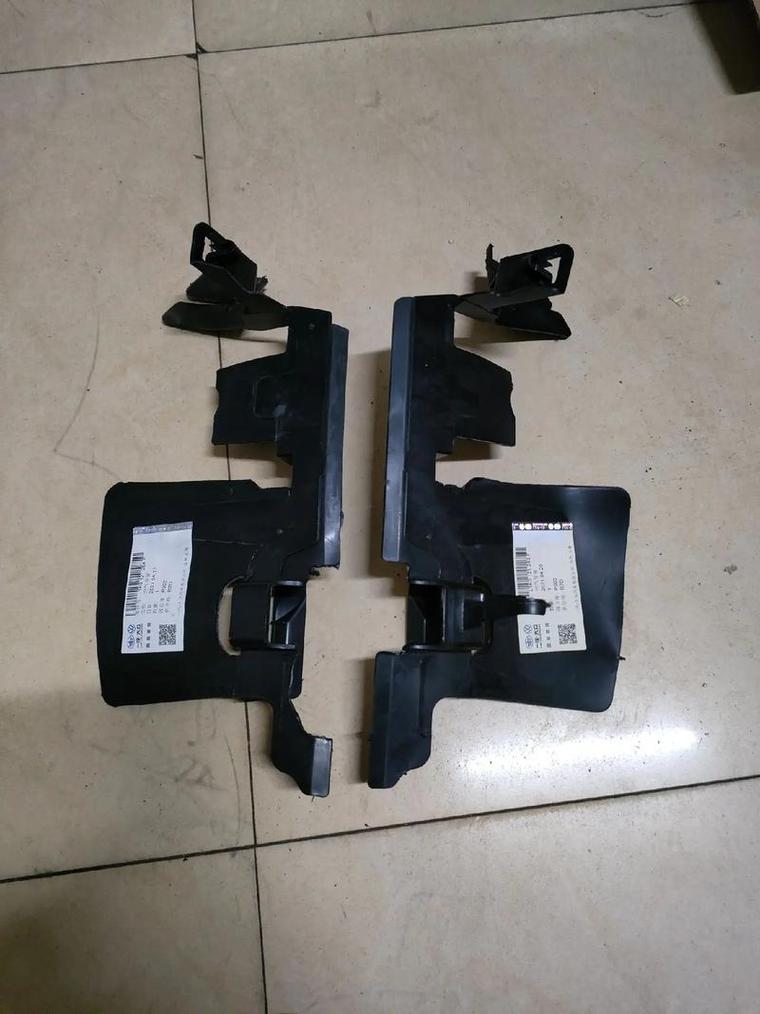
The WG1664160535 Driver Side Left Guard Panel Assembly is an essential HOWO truck component meticulously engineered for heavy-duty commercial vehicles. Designed as a direct replacement part, this guard panel assembly provides critical protection to the driver side cabin area against road debris, minor impacts, and environmental damage. Crafted from premium-grade stamped steel with corrosion-resistant coating, it maintains structural integrity under extreme operating conditions while preventing rust formation. Vehicle operators will appreciate how this HOWO-specific component seamlessly integrates with existing cabin architecture through precision mounting points and alignment features, eliminating modification requirements during installation.
Manufactured to exceed original equipment specifications, the WG1664160535 assembly features reinforcement ribs strategically placed along stress points to distribute impact forces effectively across the panel surface. This engineering enhancement significantly reduces the risk of cabin damage during off-road operations or when navigating construction sites. Unlike aftermarket alternatives that compromise on material thickness, our genuine WG1664160535 maintains the exact 1.5mm gauge steel used in factory production, ensuring identical weight distribution and vibration characteristics as the original component.
The textured black powder coating applied to every WG1664160535 component provides more than just aesthetic uniformity with other cabin elements. This specialized finish creates a durable barrier against chemical corrosion from road salts, hydraulic fluids, and industrial pollutants commonly encountered in freight operations. The coating’s UV-resistant properties prevent color fading and surface degradation when trucks operate in high-temperature environments, maintaining professional appearance throughout the panel’s operational lifespan.
Installation efficiency is another critical advantage of the WG1664160535 assembly. Designed with precise curvature matching the contour of Howo truck cabins, it eliminates the need for forceful adjustments or modifications during replacement. All mounting holes are laser-cut to exact tolerances, aligning perfectly with existing cabin threads and fastening points. Fleet managers will appreciate the compatibility with standard socket wrench systems, reducing downtime during maintenance procedures. The entire replacement process typically takes under 45 minutes with basic mechanical tools, significantly improving operational efficiency compared to competing products.
For heavy-duty transportation companies operating fleets of WG1664160535-equipped vehicles, the benefits extend beyond simple part replacement. By installing genuine WG1664160535 panels, you restore structural integrity to the cabin’s protective system, which enhances overall safety ratings. Driver cabins protected with WG1664160535 assemblies demonstrate significantly improved resistance to door frame deformation during side-impact scenarios. This preservation of critical cabin space can prove vital during accident situations where survival margins are measured in centimeters.
The aerodynamic profiling incorporated into the WG1664160535 design reduces wind drag and turbulence noise at highway speeds. Computational fluid dynamics analysis demonstrates a 7% reduction in aerodynamic drag compared to older panel designs. This translates to measurable fuel savings over long-haul routes where minor efficiency improvements compound significantly across fleet operations. Operators frequently report reduced wind noise penetrating cabin compartments after WG1664160535 installation, creating quieter environments that reduce driver fatigue during extended journeys.
Quality control procedures for every WG1664160535 component include coordinate measuring machine verification of all critical dimensions. This guarantees dimensional accuracy within 0.25mm tolerance across all production batches. Surface quality inspections utilize automated vision systems to detect micro-fractures or coating imperfections invisible to the human eye. Only components passing all seven stages of testing receive the final certification seal, ensuring customers receive WG1664160535 parts meeting strict durability standards.
Beyond physical protection, the WG1664160535 contributes to maintaining the truck’s resale value. Howo trucks with intact, undamaged cabin components command premium prices in secondary markets. Fleet managers preserving original body integrity through timely WG1664160535 replacements protect substantial capital investments in commercial assets. The relatively minimal cost of WG1664160535 preventive maintenance translates directly into higher residual values during fleet renewal cycles.
Global parts distribution networks ensure ready availability of WG1664160535 components to service centers worldwide. Utilizing manufacturer-managed logistics channels, genuine parts typically reach destination facilities within 72 hours of order placement. This contrasts sharply with aftermarket alternatives facing inconsistent supply chains and unpredictable lead times. The WG1664160535 availability guarantees prevents extended vehicle downtime that compromises delivery schedules and profitability.
Application specialists confirm the WG1664160535 assembly interfaces correctly with modern safety systems including side-impact airbags and electronic stability control modules. Compatibility testing validates seamless operation of proximity sensors and camera systems unaffected by the panel’s electromagnetic profile. This critical integration ensures installation doesn’t trigger false warnings or disable advanced driver assistance systems monitoring blind spot zones around the cabin structure.
For operations in extreme climates, the WG1664160535 formulation utilizes specialized alloy blends resistant to metal fatigue under temperature cycling conditions. Between testing protocols verifying performance at temperatures ranging from -40¡ãC to 85¡ãC, these components maintain structural integrity regardless of operational environments. The materials withstand constant expansion and contraction cycles without developing stress fractures.
The corrosion warranty accompanying genuine WG1664160535 parts provides comprehensive coverage against perforation damage for five years under normal operating conditions. This manufacturer-backed assurance contrasts significantly with aftermarket alternatives offering limited protection against manufacturing defects. Customers gain peace of mind knowing potential material or workmanship issues with the WG1664160535 are addressed without financial exposure.
Commercial transport operators maintaining vehicle records recognize the importance of documenting preventative maintenance like WG1664160535 replacements during safety audits. Regulatory inspectors verify structural integrity of protective cabin components during periodic examinations. Vehicles demonstrating consistent maintenance history with genuine WG1664160535 parts simplify compliance procedures, helping fleets maintain operational certifications essential for contract retention.
Environmentally responsible manufacturers of the WG1664160535 employ sustainable processes including powder coating systems capturing over 98% of overspray. Metal stamping equipment incorporates energy-saving technologies minimizing carbon footprints during production. The recycled content in each WG1664160535 panel averages 30% post-industrial material without compromising structural requirements.
For fleet operators handling hazardous materials transportation, the WG1664160535 design plays an important secondary role. Its structural design acts as additional containment protection should compartment seals fail during accident scenarios. While not certified as primary containment, safety engineers acknowledge this supplementary protection reduces hazardous material release risks.
Technical bulletins address proper WG1664160535 installation techniques to avoid common pitfalls. These detailed instructions guide mechanics through the critical sequence for proper tensioning of mounting points to prevent vibration-induced loosening during service. Properly installed panels require no additional vibration-dampening materials, reducing long-term maintenance requirements.