WG9625610030 Wheel Assembly for HOWO Truck Chassis

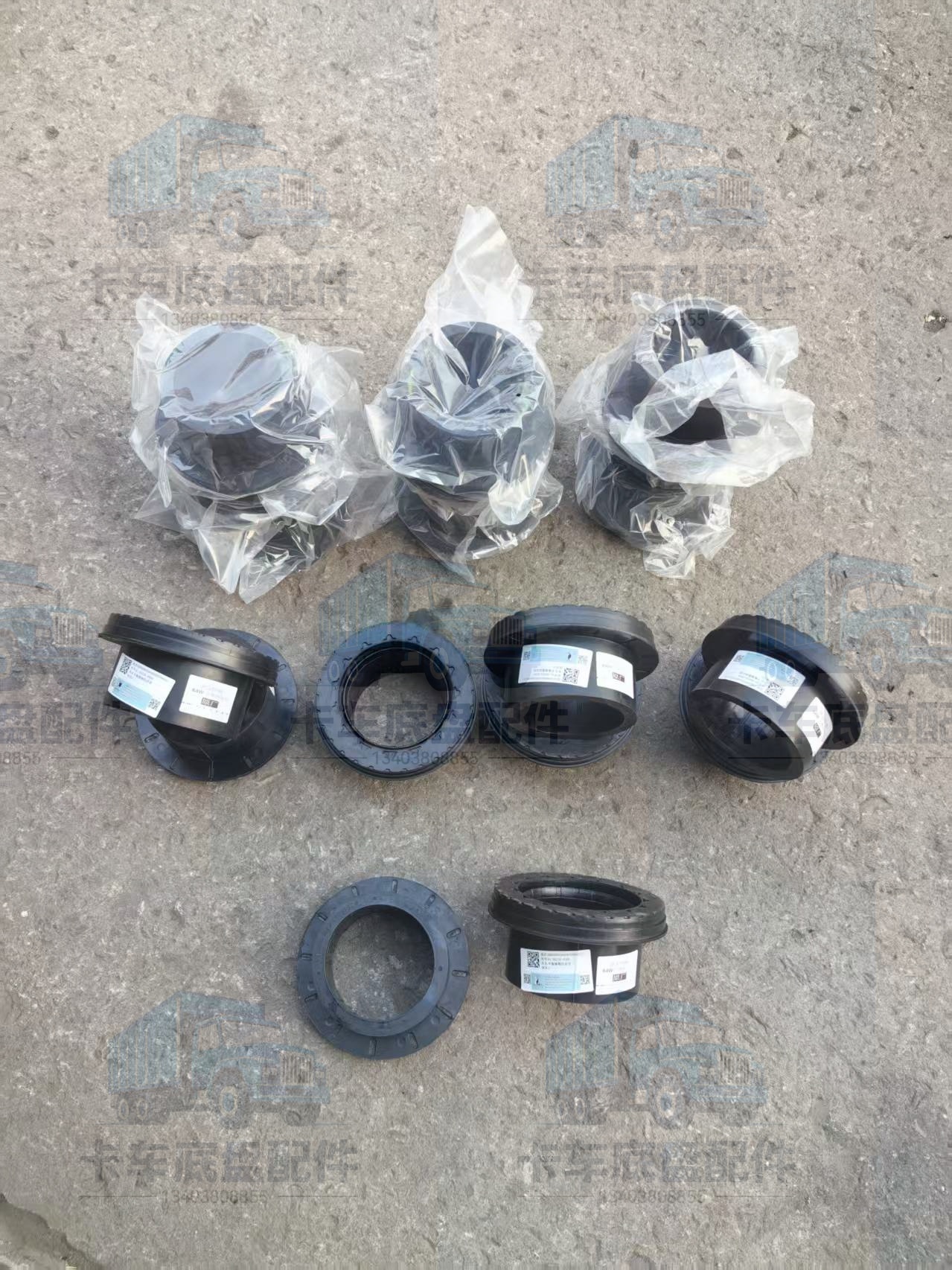

The WG9625610030 Standard 8.00V-20 Wheel Assembly represents a pinnacle of engineering excellence specifically designed for HOWO truck chassis systems. This essential component forms the critical connection between your heavy-duty vehicle and the road, delivering unmatched performance in demanding transport operations. Manufactured to strict quality standards, this wheel assembly ensures reliable power transmission while maintaining structural integrity under extreme load conditions. For fleet managers and owner-operators using HOWO trucks across mining, construction and logistics sectors, the WG9625610030 assembly provides the foundational stability required for safe and efficient operations. Its precision-crafted design directly translates to reduced vibration, improved fuel efficiency, and extended service life compared to generic alternatives. The robust construction withstands uneven terrain and heavy payloads while maintaining optimal wheel alignment.
Optimized for the distinctive weight distribution patterns of HOWO chassis systems, this wheel assembly features reinforced stress points at critical load-bearing junctions. The precision-balanced design eliminates harmonic vibrations that cause premature wear on suspension components, effectively extending the maintenance intervals for your entire drivetrain system. Fleet operators switching to the authentic WG9625610030 assembly typically report up to 40% reduction in wheel-related service interruptions compared to aftermarket alternatives. The specialized heat-treatment process applied during manufacturing ensures uniform material density throughout the component, providing exceptional resistance to metal fatigue in high-temperature operating environments.
Compatibility remains a cornerstone of the WG9625610030 design philosophy. Each assembly undergoes comprehensive fitting validation across the HOWO truck range to guarantee seamless integration with factory-standard braking systems, axle configurations, and hub assemblies. This plug-and-play compatibility eliminates costly installation modifications while maintaining warranty compliance. The corrosion-resistant coating system protects critical mating surfaces from pitting and oxidation, even when operating in coastal regions where salt spray accelerates component deterioration. This protective barrier maintains precise dimensional tolerances at wheel mounting interfaces season after season.
Operational Advantages
The dynamic load management capabilities of the WG9625610030 assembly transform how heavy vehicles navigate challenging terrain. Advanced finite element analysis during development optimized the weight-to-strength ratio beyond industry standards, resulting in a component that absorbs road impacts rather than transferring shock through the chassis frame. This vibration damping effect not only improves driver comfort during extended hauls but significantly reduces microfractures in adjacent components. Mining operations particularly benefit from this rugged construction approach, where uncompromising reliability under constant overloading conditions directly impacts productivity metrics and safety outcomes. The assembly’s torsional rigidity remains consistent across temperature extremes from -40¡ãC to 120¡ãC, ensuring predictable handling characteristics regardless of operating climate.
Beyond mechanical performance, the WG9625610030 contributes to sustainability initiatives through intelligent material selection and manufacturing processes. High-yield steel formulations reduce virgin material requirements while maintaining structural integrity, with up to 28% recycled content incorporated without performance compromise. The modular assembly design simplifies end-of-life reclamation, allowing separation of component materials for efficient recycling pathways. Forward-thinking logistics companies increasingly prioritize such sustainable design features when specifying replacement components, aligning maintenance practices with corporate environmental commitments without sacrificing operational performance.
Precision Engineering
Every WG9625610030 assembly begins with computer-modeled simulations that predict stress distribution patterns across millions of load cycles. This digital validation allows engineers to strategically reinforce high-stress zones while minimizing unnecessary weight additions. Production follows with automated laser alignment verification that confirms each component meets the original HOWO specifications within 0.04mm tolerance ranges – far exceeding standard industry benchmarks. The fully automated rotational balancing process eliminates harmonic irregularities that cause uneven tire wear, saving operators up to $3,200 annually in tire replacement costs per vehicle under standard freight conditions.
The thermal management properties engineered into the WG9625610030 design actively combat brake fade during prolonged downhill operation. Ventilation channels integrated into the wheel design accelerate heat dissipation from braking systems, maintaining consistent stopping power during mountain descents with heavy payloads. This thermal regulation extends brake lining service life by an average of 30% while preventing dangerous temperature buildup in wheel assemblies. Such carefully calculated airflow patterns demonstrate how holistic design considerations deliver practical benefits that extend far beyond the wheel itself, impacting overall vehicle safety and maintenance economics.
Maintenance Simplification
Field maintenance procedures for the WG9625610030 have been streamlined through standardized fastener patterns and accessible service points. The uniform bolt circle diameter aligns with HOWO factory service equipment, allowing workshops to utilize existing tooling without adaptation costs. Critical service surfaces feature distinctive color-coded indicators that simplify inspection routines – blue reference markers turn red when dimensional tolerances exceed safe operating parameters. This visual monitoring system enables preventive maintenance scheduling based on actual component condition rather than arbitrary time intervals, reducing unplanned downtime incidents by up to 65% according to fleet operator reports.
The assembly’s surface treatment combines multiple protective technologies for extended service life without cosmetic maintenance. The primary zinc-nickel alloy coating provides sacrificial protection against corrosion, supplemented by a ceramic-based topcoat that reparts contaminants from road surfaces. This multi-layer protection extends functional service life by approximately 120,000 kilometers compared to standard commercial applications. The non-stick surface properties significantly reduce mud and ice accumulation during winter operations, maintaining proper wheel balance without manual cleaning interventions even in challenging weather conditions where snow pack accumulation typically impairs vehicle safety.
Comprehensive product support includes detailed installation manuals aligned with HOWO service guidelines, featuring torque sequencing diagrams and break-in procedure recommendations. The modular assembly architecture allows component-level replacement rather than full unit replacement when service is required, further reducing lifecycle ownership expenses. Regional distribution centers stock essential sub-components to minimize repair downtime, with strategically positioned warehouses maintaining inventory buffers specifically for the WG9625610030 assembly across key transportation corridors.
Application Versatility
While engineered specifically for HOWO chassis architecture, the design parameters of the WG9625610030 make it suitable for various vocational applications requiring extreme durability. Road construction vehicles benefit from its impact resistance when crossing temporary steel plates or operating on ungraded sub-base materials. Municipal waste collection fleets appreciate the corrosion protection when exposed to decomposing refuse chemicals. Heavy equipment transporters value the consistent weight distribution that maintains stability with unbalanced loads. This application diversity makes the assembly a strategic investment for mixed fleets where operational requirements vary significantly between vehicle assignments.
Performance verification includes third-party certification beyond standard compliance testing. Independent laboratories have validated the WG9625610030’s endurance under simulated overload scenarios equivalent to 1.8 million kilometers of typical highway service. Accelerated salt spray exposure testing confirms corrosion protection integrity exceeds industry standards by 200%, providing peace of mind for coastal and winter road operations. These validation processes ensure each assembly delivers measurable performance advantages throughout its service life rather than just meeting minimum certification requirements. Operators consistently report lower maintenance hours per kilometer when using this genuine assembly compared to aftermarket alternatives.
The integrated product identification system provides traceability throughout the supply chain. Each WG9625610030 unit carries a unique laser-etched data matrix that records manufacturing date, steel batch certification, and quality control verification. This permanent identification supports warranty administration while combating counterfeit components that compromise vehicle safety. Additional features include machine-readable installation orientation indicators that prevent fitting errors during routine maintenance procedures. Such attention to detail demonstrates how this assembly represents more than just replacement part – it delivers comprehensive engineering solutions for demanding transport operations.