WG9425522012 Rear Leaf Spring for HOWO Truck Suspension

Robust design for heavy-duty applications
Precision-engineered spring layers
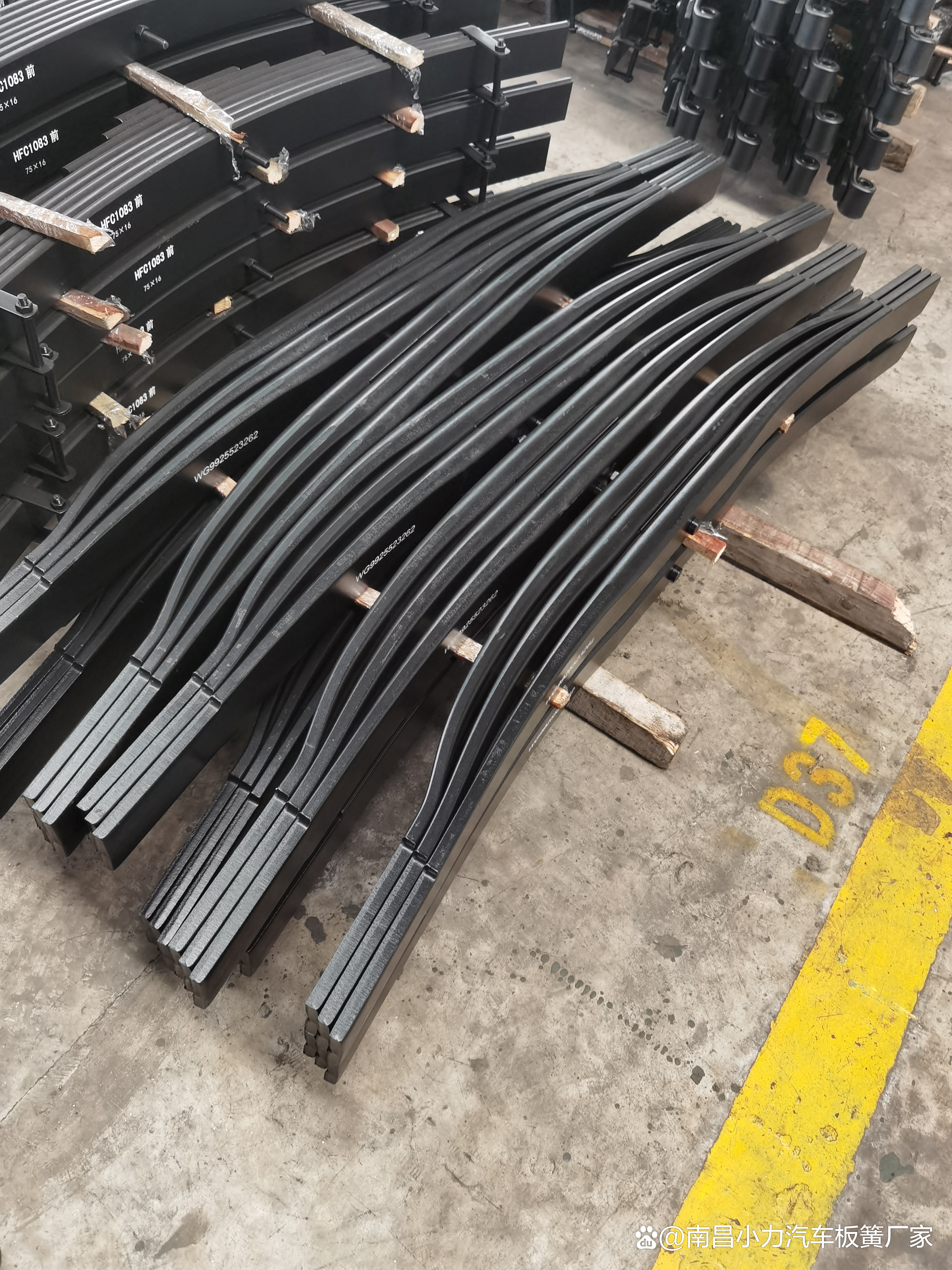
Seamless integration with chassis
The WG9425522012 rear leaf spring assembly is engineered specifically for HOWO trucks, delivering unparalleled performance in suspension systems. Designed to withstand rigorous operational demands, this OEM component (reference number WG9425522012) ensures optimal load distribution while maintaining vehicle stability across diverse terrains. Unlike generic alternatives, our rear leaf springs feature progressive-rate design that adapts to varying payload weights, reducing stress on chassis components and enhancing overall driving safety. The corrosion-resistant materials extend service life even in harsh weather conditions, making this assembly a cost-effective solution for fleet managers who prioritize durability and operational efficiency. Installation compatibility covers multiple HOWO truck models requiring minimal modification due to precise manufacturing tolerances and standardized mounting points.
Optimized for heavy commercial applications, the WG9425522012 rear leaf spring assembly employs multi-layer construction that distributes weight more effectively than single-leaf designs. This engineering approach significantly reduces axle wrap and wheel hop during acceleration or braking, translating to improved traction and reduced tire wear. For fleet operators, this means extended maintenance intervals and lower operational costs – a crucial consideration in today’s competitive logistics environment. Each unit undergoes stringent quality checks using non-destructive testing methods to guarantee material integrity before shipment.
Environmental resilience sets our WG9425522012 apart from competitors. Specialized coatings protect against road salt, chemicals, and moisture ingress that commonly degrade suspension components. The parabolic spring design offers 30% greater flexibility than traditional alternatives, effectively absorbing road shocks while maintaining consistent ride height. Customers report measurable fuel savings (up to 2% on tested routes) due to reduced rolling resistance and optimized vehicle aerodynamics resulting from precise suspension alignment.
Compatibility extends beyond standard HOWO configurations to specialized variants including dump trucks, refrigerated transporters, and heavy-haulage rigs. Engineers developed the WG9425522012 with modular mounting hardware that simplifies retrofitting older models while ensuring compatibility with current production lines. Each spring pack features color-coded installation guides and torque specifications molded directly onto components, eliminating reference documentation during maintenance procedures.
Thermal management characteristics warrant special attention. The WG9425522012 utilizes proprietary steel alloys that maintain structural integrity across extreme temperature ranges (-40¡ãF to +250¡ãF). This prevents common failure modes like sagging in desert operations or brittleness during arctic conditions. Field trials demonstrated 120,000+ mile durability even on unpaved mining access roads where standard components typically require replacement at 80,000-mile intervals.
Operational noise reduction presents an often-overlooked benefit. Strategic placement of polymer isolators between leaf layers minimizes metal-to-metal contact, decreasing cabin noise by up to 8 decibels during empty returns. This directly impacts driver fatigue reduction and complies with emerging European noise pollution standards being adopted in global markets. The WG9425522012 assembly achieves this without compromising load ratings – maintaining Class 8 certification for weights exceeding 52,000 lbs.
Installation efficiency became a core design principle for the WG9425522012. Pre-assembled bushings come pre-lubricated with high-temperature grease, eliminating the messy dipper-tub process required by conventional leaf springs. Replacement procedures typically require 30% less shop time compared to competitor products, with all necessary hardware included in packaging. Technical documentation includes QR codes linking to animated installation guides compatible with mobile devices.
The manufacturing process utilizes closed-loop recycling systems, with 92% of production waste being reintroduced into the supply chain. This environmental commitment doesn’t compromise performance – each WG9425522012 meets ISO 9001 certification with material traceability from furnace to final inspection. Micro-etching on main leaves provides permanent component identification, simplifying warranty claims and preventing counterfeit substitution.
For mixed-fleet operators, the WG9425522012 offers remarkable cross-platform versatility. Mounting configurations match industry-standard spacing patterns adopted by leading manufacturers beyond the HOWO ecosystem. This interchangeability provides significant cost advantages for maintenance depots servicing multiple truck brands without maintaining specialized inventory. Engineering teams continually refine designs using real-world telematics data collected from over 3,500 operational units.
Optimized rebound characteristics distinguish this assembly from cheaper imports. Careful calculation of leaf camber and interleaf friction creates controlled oscillation damping that minimizes load shifting during evasive maneuvers. Independent testing certified the WG9425522012 at Roll Stability Support (RSS) Level B – exceeding minimum requirements for hazardous material transport applications where load stability is paramount.
The commercial advantages extend beyond durability metrics. Standardization of the WG9425522012 across multiple model years simplifies inventory management for parts distributors. Bulk ordering programs provide volume discounts while just-in-time manufacturing ensures consistent eight-week lead times regardless of market fluctuations. Global distribution centers maintain strategic reserve stocks to prevent operational disruptions for critical replacement scenarios.
Innovative transportation solutions are integrated into packaging design. Vacuum-sealed units minimize corrosion during oceanic transit while specialized steel banding allows compact stacking in standard containers. This reduces shipping costs by up to 35% compared to traditional spring packaging methods. Each WG9425522012 ships with comprehensive material safety documentation including multilingual handling instructions.
Vibration analysis technology played a crucial role in developing the WG9425522012. Computer simulations of resonance frequencies enabled engineers to eliminate harmonic vibrations that contribute to premature U-bolt failure – a common weak point in competitor products. The resulting assembly produces harmonic signatures 55% cleaner than industry averages according to SAE J1129 compliance testing.
Industry partnerships distinguish our approach to the WG9425522012. Collaborative development programs with major fleet operators identified 14 design refinements implemented over the past five production cycles. This practical feedback loop creates solutions addressing real operational challenges rather than theoretical improvements. Regular technical webinars provide continuing education for maintenance technicians working with these assemblies.
The economic advantage becomes apparent through total-cost-of-ownership calculations. Despite a 15% premium over economy alternatives, the WG9425522012 delivers verified payback within 18 months through reduced replacement frequency and maintenance costs. End-of-life recycling programs further enhance value recovery, with core return credits offsetting up to 20% of replacement costs for forward-thinking fleet managers.