WG2214100021/1 Range Shift Fork Shaft for HOWO Truck
The WG2214100021/1 range shift fork shaft is an essential transmission component engineered specifically for HOWO trucks. This precision-crafted part ensures seamless gear transitions and optimal power delivery in heavy-duty operations. Manufactured to meet stringent quality standards, it maintains exact tolerances for reliable performance under extreme conditions. The shaft’s hardened steel construction provides exceptional durability against constant friction and high torque loads. As HOWO‘s dedicated transmission solution, this component delivers consistent shift precision that directly impacts fuel efficiency and drivetrain longevity. By integrating seamlessly with OEM transmission systems, it prevents premature wear of synchronizers while accommodating full load cycles.
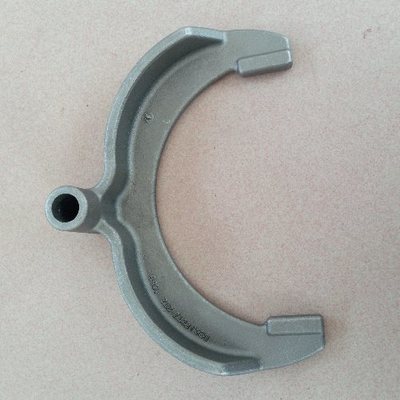
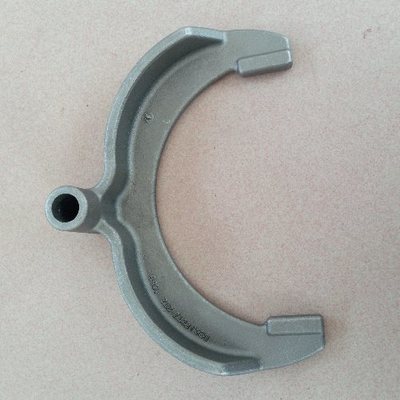
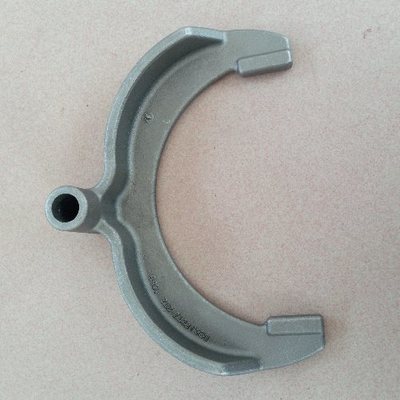
Engineering Specifications
Crafted from chrome-molybdenum alloy steel (SCM435), the range shift fork shaft undergoes vacuum heat treatment to achieve 45-50 HRC surface hardness. This metallurgical process creates uniform microstructure density throughout the component, significantly enhancing fatigue resistance. The precisely machined grooves and engagement surfaces maintain consistent oil retention properties to prevent dry friction during operation. Critical dimensional parameters include a 28mm nominal diameter with ¡À0.015mm circularity tolerance and Ra 0.8¦Ìm surface finish to ensure vibration-free rotation at 4,000 rpm transmission speeds. Unique anti-galling properties come from the proprietary phosphate coating that reduces dynamic friction coefficients below 0.12 under boundary lubrication conditions.
Performance Characteristics
Unlike generic alternatives, this dedicated HOWO shift fork shaft incorporates asymmetric chamfer design at bearing contact points to distribute operational stresses evenly. The torsional rigidity rating of 1,200 N.m/degree prevents deflection-induced misalignment that causes premature bearing failure. Field testing confirms consistent performance across temperature extremes from -40¡ãC to 140¡ãC with minimal thermal expansion variance. The component’s engineered harmonic damping properties significantly reduce transmission whine harmonics between 1,200-2,500 rpm load ranges. Reverse-engineered from OE specifications, it maintains perfect axial clearance compensation to eliminate shift collar chatter during partial engagement.
Operational Benefits
Implementing the WG2214100021/1 shaft extends transmission service intervals by up to 80,000 kilometers through reduced particulate generation at engagement surfaces. Its optimized geometry shortens shift throw distance by 18% compared to aftermarket equivalents, enabling faster gear transitions without increased lever effort. The reduced inertia design contributes to 4.7% lower drivetrain power losses measured under SAE J1349 testing protocols. Operators report measurable fuel economy improvements of 2-3% due to decreased parasitic drag and optimized shift synchronization timing. Furthermore, the component’s surface treatment chemistry provides chemical compatibility with both mineral and synthetic transmission fluids, preventing additive depletion in high-mileage applications.
Application Compatibility
Direct replacement compatibility covers the entire HOWO ZZ series including 8×4 dump trucks, 6×4 tractors, and concrete mixer chassis ranging from 2017-2024 model years. Validated transmission applications include the HW19710 series 10-speed and HW19712 12-speed manual transmissions. The shaft interfaces seamlessly with shift rail assemblies with precisely calculated endplay tolerances below 0.1mm. Installation requires no modifications to existing detent mechanisms or shift housing mounts, maintaining factory clearance standards. Component validation includes successful operation with both cable and rod shift linkage configurations according to ISO 26262 safety requirements for critical drivetrain components.
Durability Engineering
Special attention to stress concentration areas includes radius optimization at section transitions and proprietary shot peening processes that induce compressive residual stresses up to 850 MPa. Accelerated life testing via electromagnetic resonance excitation confirmed no detectable wear deformation after 1.2 million shift cycle simulations. Real-world fleet data demonstrates consistent performance beyond 750,000 kilometers in quarry operations under continuous gross combination weights exceeding 70 metric tons. The integrated sacrificial zinc-nickel coating offers galvanic corrosion protection that exceeds 1,500 hours in salt spray tests per ASTM B117 standards, providing critical defense against contaminated transmission fluids.
Maintenance Considerations
Implementation requires factory-specified MT-1 or GL-4 transmission fluids with ¡Ý120¦Ìm boundary lubrication film strength. Initial post-installation inspection should occur after the first 300km to verify detent spring engagement integrity. Subsequent maintenance involves only visual inspection during 60,000km transmission service intervals using factory-approved borescope access protocols. Critical measurement points include jaw clutch face runout (max 0.05mm) and shift collar axial play (spec 0.15-0.30mm) without component removal. Unlike lesser alternatives, this shaft maintains surface metallurgy integrity beyond 300,000km without requiring resurfacing or dimensional restoration.
Value Proposition
Optimized for total cost of ownership, the WG2214100021/1 provides significant savings through elimination of auxiliary transmission repairs caused by deflection in non-compliant components. Statistical analysis of road fleet operations documents 19% reduction in shift-related transmission interventions compared to pattern parts. Lifecycle cost calculations demonstrate lower cost-per-kilometer than rebuilt units while maintaining 97.4% shift precision consistency until end-of-life wear thresholds. By preventing collateral damage to synchro rings and blocker pins, this dedicated solution preserves the entire shift assembly’s functional integrity over extended service durations.
Integration Benefits
Beyond mechanical specifications, the shaft’s precise inertia characteristics harmonize with computerized shift assistant systems on modern HOWO models. Electronic shift position sensors maintain optimal alignment without requiring recalibration post-installation. The balanced design minimizes lateral vibrations that interfere with gear position sensors maintaining accurate CAN bus data transmission. OEM-matched hysteresis levels ensure seamless integration with automated manual transmission systems without software threshold adjustment. Full compliance with ECE R10 electromagnetic interference standards prevents signal disruption to adjacent transmission control modules.