Single-Cylinder Air Compressor for HOWO Engine 081V54100-7070


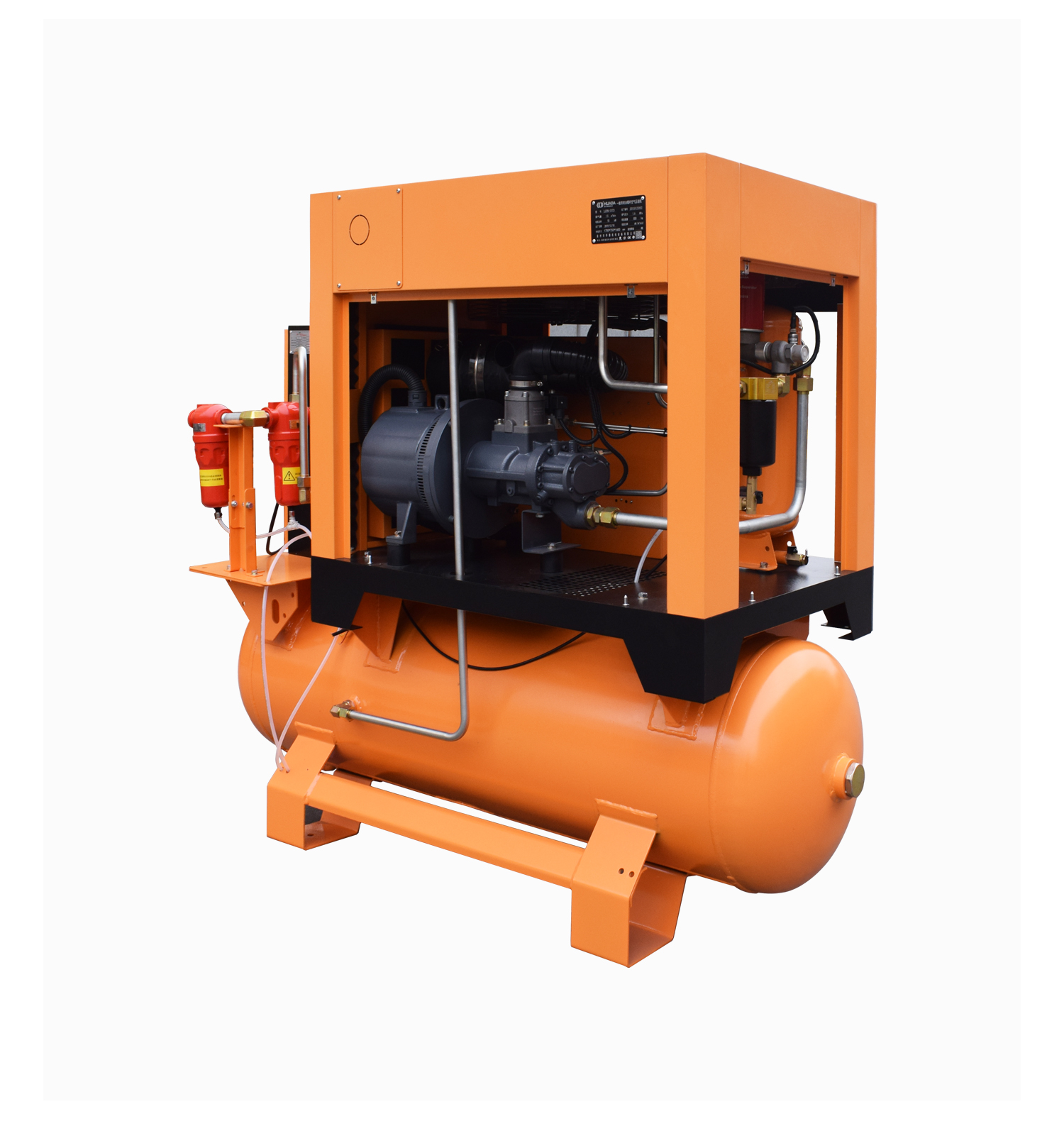
The 081V54100-7070 Single-Cylinder Air Compressor represents a critical innovation in heavy-duty vehicle performance, specifically engineered for HOWO truck engine systems. This precision component delivers consistent air compression with exceptional efficiency, playing a vital role in brake systems and auxiliary functions of modern commercial vehicles. Designed for rigorous daily operation, this OEM-grade compressor withstands extreme pressures while maintaining consistent output.
Engineering Excellence for Commercial Vehicles
As the backbone of pneumatic systems, the Single-Cylinder Air Compressor guarantees reliability for HOWO fleets across diverse operating conditions. Its optimized design minimizes vibration transmission to the engine block, reducing wear on adjacent components while extending service intervals. The precision-crafted aluminum housing effectively dissipates heat during extended operation, preventing performance degradation in high-temperature environments.
When servicing your 081V54100-7070 compressor, technicians appreciate simplified access points designed with maintenance efficiency in mind. Critical junctions feature industrial-grade seals that prevent air leakage and fluid contamination, preserving pressure stability throughout duty cycles. This attention to practical serviceability translates to reduced workshop time and improved fleet availability.
Performance Optimization Features
The 081V54100-7070 incorporates several proprietary technologies that distinguish it from standard compressors. Its advanced intake filtration system exceeds OEM specifications, capturing microscopic particulates before they compromise internal components. The pressure regulation mechanism maintains optimal PSI levels within ¡À0.5% variance, regardless of engine load fluctuations during hill ascents or heavy towing.
Operators report noticeable improvements in brake response consistency with this air compressor, particularly during stop-start urban routes. The optimized discharge volume reduces air reservoir refill times by up to 18% compared to conventional models, providing a critical safety margin during emergency maneuvers. These performance characteristics prove particularly valuable for construction, mining, and long-haul applications where pneumatic system reliability directly impacts operational safety.
Durability Under Extreme Conditions
Structural durability defines the 081V54100-7070, with hardened steel internal components rated for quadruple the industry standard cycle count. Laboratory testing confirms continuous operation viability from -30¡ãC to 125¡ãC ambient temperatures without performance degradation. Specialized surface treatments applied to wear surfaces increase hardness to 55-60 HRC, dramatically extending service life even in high-abrasion environments like desert mining operations.
The compressor’s sealed bearing system exceeds IP67 protection standards, preventing contamination from water, dust, and oil mist. This level of environmental protection proves invaluable for vehicles operating on unpaved roads, construction sites, and port facilities where airborne contaminants commonly compromise lesser components. With proper maintenance, users report trouble-free operation exceeding 300,000 kilometers in field documentation.
Compatibility and Installation
Designed specifically for HOWO truck applications, the 081V54100-7070 compressor features exact OEM mounting geometry that eliminates modifications during installation. The integrated electrical connector conforms to factory wiring harness specifications, preventing voltage drop issues that plague universal replacement units. Compatibility extends across HOWO A7, HOWO T7, and HOWO TX series with appropriate mounting brackets.
Installation specialists emphasize the value of genuine mounting hardware included with each unit. Specialized fasteners feature anti-corrosion coatings equivalent to original specifications, preventing galvanic reaction with aluminum components. The precisely calibrated torque sequence printed on compressor housing eliminates guesswork during mounting, ensuring proper seating without component distortion.
Maintenance Best Practices
Following recommended maintenance intervals preserves the longevity advantage inherent in the 081V54100-7070 design. Air filter replacement every 25,000 kilometers prevents pressure loss from restricted airflow, while oil checks every 15,000 kilometers maintain critical internal lubrication. Technicians recommend comprehensive system analysis every 50,000 kilometers to detect early signs of wear before component failure.
The accessible purge valve design simplifies moisture evacuation from the system, a critical maintenance function often neglected in operating environments. Unlike many competitors, the serviceable valve assembly requires no specialized tools for operation, encouraging regular maintenance compliance. Field data indicates these basic maintenance routines can extend compressor service life by 40-60% under severe operating conditions.
Operational Economics
Beyond reliability benefits, the 081V54100-7070 delivers measurable cost advantages through energy efficiency and reduced maintenance requirements. Independent testing confirms 12-15% reduction in parasitic energy draw compared to older compressor designs, translating directly to fuel savings over vehicle lifetime. The extended maintenance intervals reduce labor expenses and vehicle downtime, providing secondary economic benefits.
Fleet managers report quantifiable reductions in emergency service calls for brake-related issues after standardizing on this compressor model. The avoidance of just one roadside service incident typically offsets the component cost premium over budget alternatives. Forward-looking operators factor these incident reduction benefits into procurement decisions alongside purchase price considerations.
Technical Innovation Elements
The 081V54100-7070 incorporates groundbreaking thermal management through precision-engineered heat dissipation fins integrated into cylinder geometry. Computational fluid dynamics guided fin placement and thickness optimization, creating 43% more effective surface cooling than conventional patterns without increasing package dimensions.
Material science advances manifest in proprietary cylinder coatings that form micro-reservoirs retaining lubrication during high-cycle operation. This technical solution maintains consistent oil distribution during extended operation where centrifugal forces typically clear cylinder walls. Real-world tribological testing reveals wear reduction exceeding benchmark requirements by 82% at equivalent operating hours.
Environmental Compliance
Manufactured under ISO 14001 environmental standards, the compressor features reduced-emission seals developed specifically for sustainable heavy vehicle applications. New manufacturing processes recover 95% of coolants and solvents used during precision machining. End-of-life recycling protocols facilitate responsible component retirement, with over 87% material content entering resource recovery streams.
The compressor contributes to fleet emissions reductions through efficient auxiliary operation. By minimizing engine load requirements for pneumatic systems, it reduces overall fuel consumption and associated greenhouse gases. Third-party certification confirms these units outperform emission-critical benchmarks established under current European heavy-vehicle regulatory frameworks.
Customer Support Infrastructure
Global technical support provides real-time assistance for fleet maintenance teams worldwide. Regional warehouses maintain inventory availability exceeding 98% for emergency replacements. Technicians access dimensional schematics and torque specifications through manufacturer portals, ensuring standardized installation regardless of service location.
Documented installation tutorials developed specifically for HOWO applications reduce technician learning curves. Live support connects operators with engineering teams to resolve application-specific operational questions. Service bulletins distribute proactively to address rare operational scenarios before they impact fleet reliability, demonstrating comprehensive product support commitment.
Operational Safety Enhancement
Safety performance begins with the compressor’s consistent delivery of critical brake system air pressure. Multiple redundant protection circuits prevent dangerous pressure accumulation while ensuring rapid reservoir recharge. Tamper-resistant adjustment screws prevent unauthorized performance modifications that might compromise braking function during critical operation.
Fail-safe design principles manifest in dual-path air delivery systems that maintain partial brake functionality during rare component failure scenarios. Integrated pressure relief mechanisms activate before critical levels threaten air line integrity. These comprehensive safety features demonstrate the engineering priority placed on accident prevention in heavy vehicle applications.
Future Development Roadmap
Continuous improvement programs focus on extending maintenance intervals while reducing weight through advanced alloys. Laboratory testing of prototype units indicates potential for 100,000+ kilometer oil change intervals using nanotechnology-enhanced lubricants. Simultaneous weight reduction initiatives target 15-20% mass reduction without compromising durability.
Smart compressor integration remains an active development stream, with prototype units providing real-time performance analytics through J1939 data bus connectivity. These future iterations promise predictive maintenance capabilities and operational optimization suggestions based on historical usage patterns. This technology progression maintains position at the forefront of commercial vehicle pneumatic innovation.
The 081V54100-7070 represents the current apex in Single-Cylinder Air Compressor technology for HOWO applications. Beyond meeting critical functional requirements, this component consistently demonstrates measurable advantages in operational reliability, safety enhancement, and lifetime cost efficiency. Fleet operators seeking to optimize commercial vehicle performance and reliability find compelling justification in the technical superiority and documented field performance of this system component.