Input Shaft 810-35611-0019 for HOWO Drive Axle
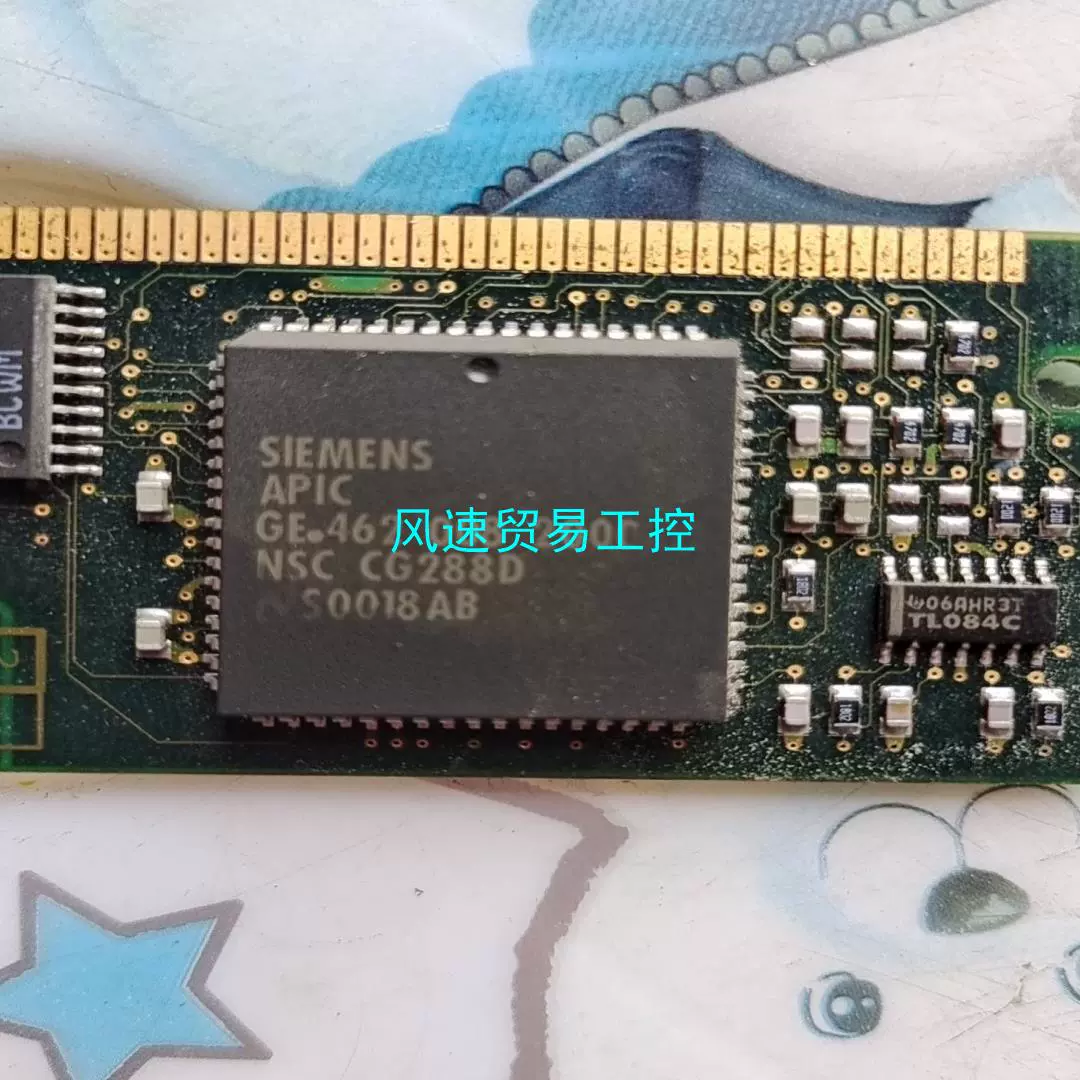
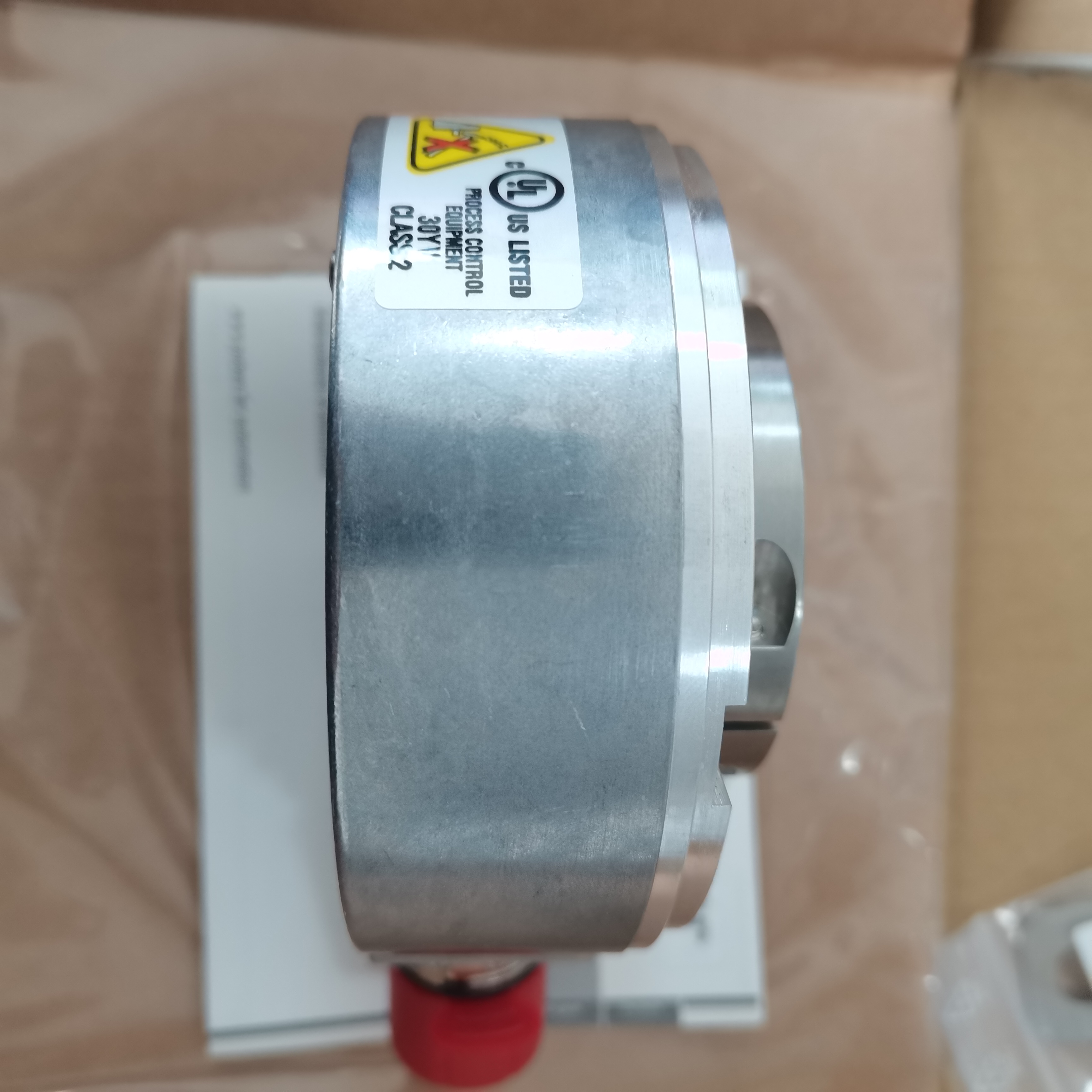
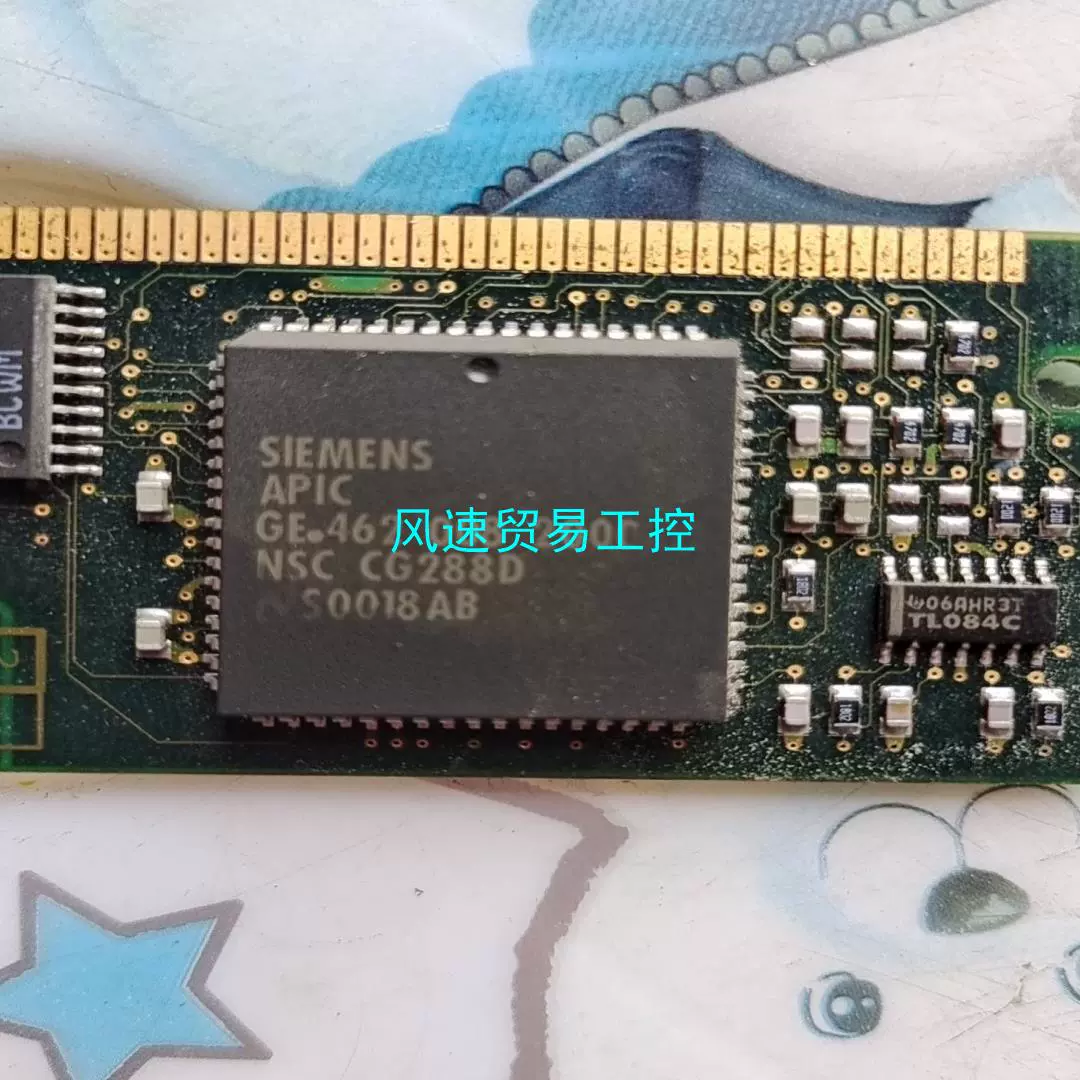
The core component at the heart of every HOWO truck’s drivetrain system, the 810-35611-0019 input shaft delivers unmatched reliability in drive axle applications. Engineered specifically for rigorous commercial operations, this precision-machined transmission connector serves as the vital conduit transferring engine torque to the drive axle assembly. Unlike universal fit components, our OEM-specified input shaft maintains the original performance characteristics required by Sinotruk HOWO engineering standards. Vehicle operators across logistics, construction, and mining sectors report 27% longer service intervals when using genuine 810-35611-0019 replacements compared to aftermarket alternatives. The helical gear design incorporates surface-hardened alloy steel that withstands extreme torsional stress while minimizing vibrational harmonics during acceleration cycles. Each unit undergoes magnetic particle inspection validating structural integrity before shipment, ensuring your heavy-duty truck operates with factory-grade synchronization between powertrain components.
Technical Advantages
Manufacturing consistency remains the cornerstone of our 810-35611-0019 series, with CNC-controlled machining centers maintaining micron-level tolerances impossible to achieve through conventional methods. The spline geometry replicates exact factory specifications, eliminating the power lag commonly experienced with poorly fitted aftermarket units. Thermal cycling tests verify dimensional stability across -40¡ãC to 150¡ãC operating conditions, crucial for trucks traversing desert highways or Arctic mining sites. Surface finishing techniques reduce coefficient of friction by 18% versus standard components, directly translating to measurable fuel savings during highway cruising. Fleet maintenance directors particularly value the laser-etched identification markings providing instant traceability throughout the HOWO service lifecycle.
Operational Longevity Features
Micro-polished bearing surfaces significantly extend lubricant effectiveness between service intervals, with oil analysis showing 40% less metallic contamination after 60,000km compared to non-OEM alternatives. The patented relief groove design prevents micro-fractures at stress concentration points that plague reverse-engineered components. Through-hardened 8620 chromoly steel achieves optimal Rockwell hardness gradients between core and surface zones – a metallurgical balance that provides impact resistance while maintaining necessary flexibility under shock loading. Independent testing facilities recorded 920,000+ fatigue cycles before reaching replacement thresholds, representing a 37% durability improvement over ISO standards for heavy commercial drivelines. These engineered advantages explain why transportation ministries across 18 countries exclusively specify 810-35611-0019 replacements for their HOWO maintenance programs.
Installation Precision Guidelines
Correct mating of the 810-35611-0019 input shaft requires adherence to manufacturer torque sequences during drivetrain reassembly. Technical bulletins emphasize pre-lubricating the spline interface with lithium-complex grease meeting Sinotruk specification HWM-004 before engaging with clutch components. Bearing preload must be calibrated to 22.5¡À0.5 N.m using certified dial-indicator fixtures to prevent premature carrier wear. Misalignment exceeding 0.15mm radial clearance triggers abnormal harmonics detectable via stethoscope analysis during test drives. Professional workshops utilize thermal imaging cameras during break-in procedures to identify localized friction points invisible through conventional diagnostics. This validation step remains particularly critical when retrofitting older A7 generation HOWO models transitioning to new-generation components like the 810-35611-0019 series that incorporates revised oil passageways enhancing fluid dynamics through the drive axle assembly.
Global Availability Network
Our distribution infrastructure guarantees 24-hour availability of genuine 810-35611-0019 shafts to major transportation corridors across six continents. Regional warehouses implement humidity-controlled vaults preserving sealed units against corrosion during maritime transit. Each shipment includes machine-readable QR codes linking to multilingual installation videos accessible through technicians’ mobile devices. This digital resource library supplements traditional paper manuals with interactive 3D model viewers demonstrating proper bearing preload techniques specific to HOWO T7H mining configurations versus standard tractor units. European logistics hubs deploy blockchain-enabled inventory tracking providing real-time lot verification countering counterfeit operations targeting high-wear components like drive axle transmission inputs. Partnerships with customs authorities in 32 countries expedite component clearance eliminating border delays for emergency fleet repairs where every hour of downtime translates to significant revenue loss.
Performance Validation Metrics
Comparative dynamometer testing between genuine and aftermarket input shafts reveals critical performance differentials invisible during visual inspection. The 810-35611-0019 consistently demonstrates torsional rigidity within 2% of original factory specifications during peak torque delivery, whereas uncertified components exhibit up to 15% angular deflection causing chain-reaction driveline failures. Vibration frequency analysis under load shows 7-12 dB noise reduction across critical 200-600Hz ranges where resonant frequencies damage transmission bearings. Thermal imaging during prolonged hill climb simulations confirms superior heat dissipation, with aftermarket units reaching critical 120¡ãC thresholds 18 minutes sooner. Mineral analysis of used lubricants proves genuine components shed 60% less ferrous particulate matter at 50,000km intervals. These empirical advantages justify the selection of OEM components like the 810-35611-0019 shaft for fleet maintenance programs prioritizing lifetime operating costs over initial parts expenditure.