HOWO Truck Fuel Injection Pump Gear 080V11301-0259
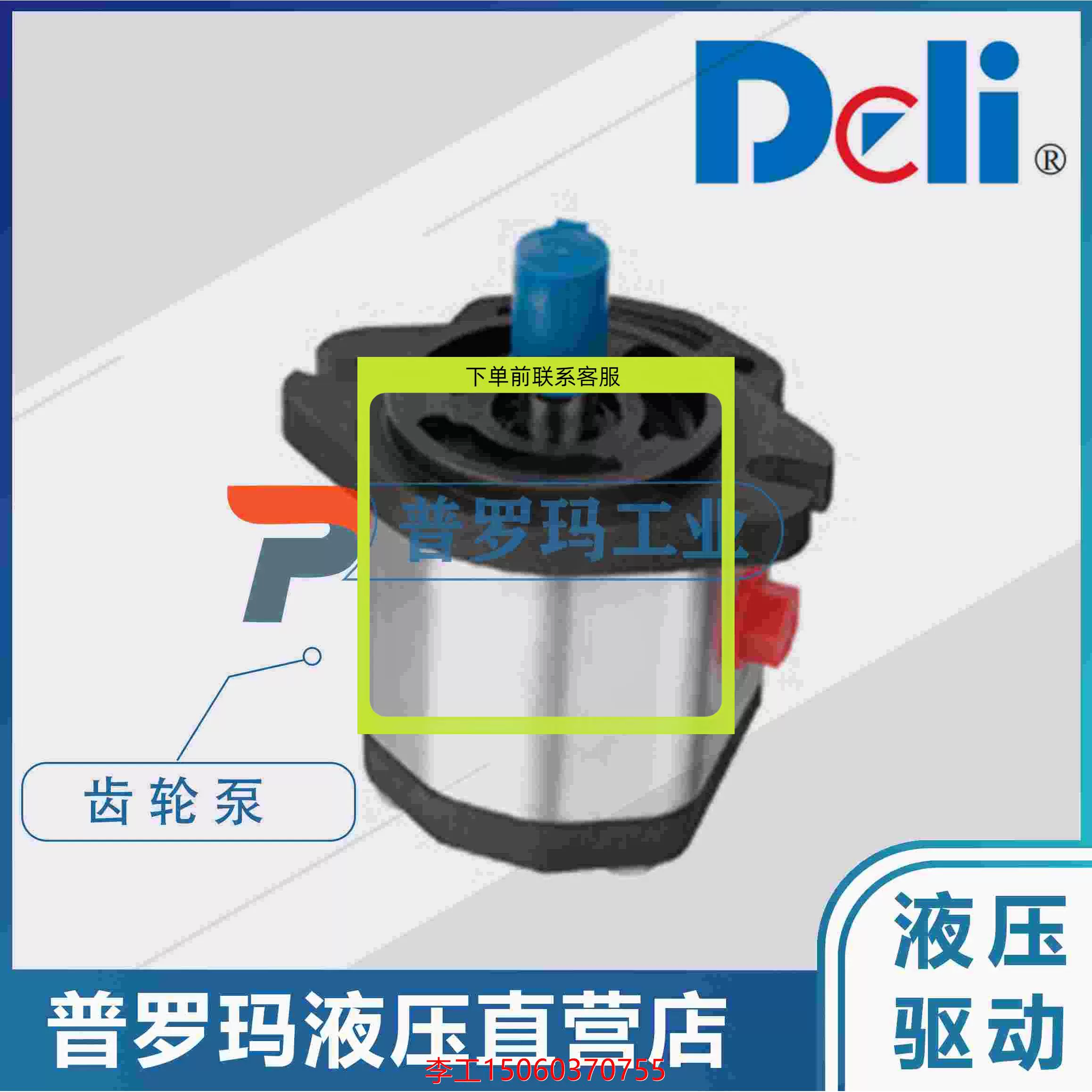
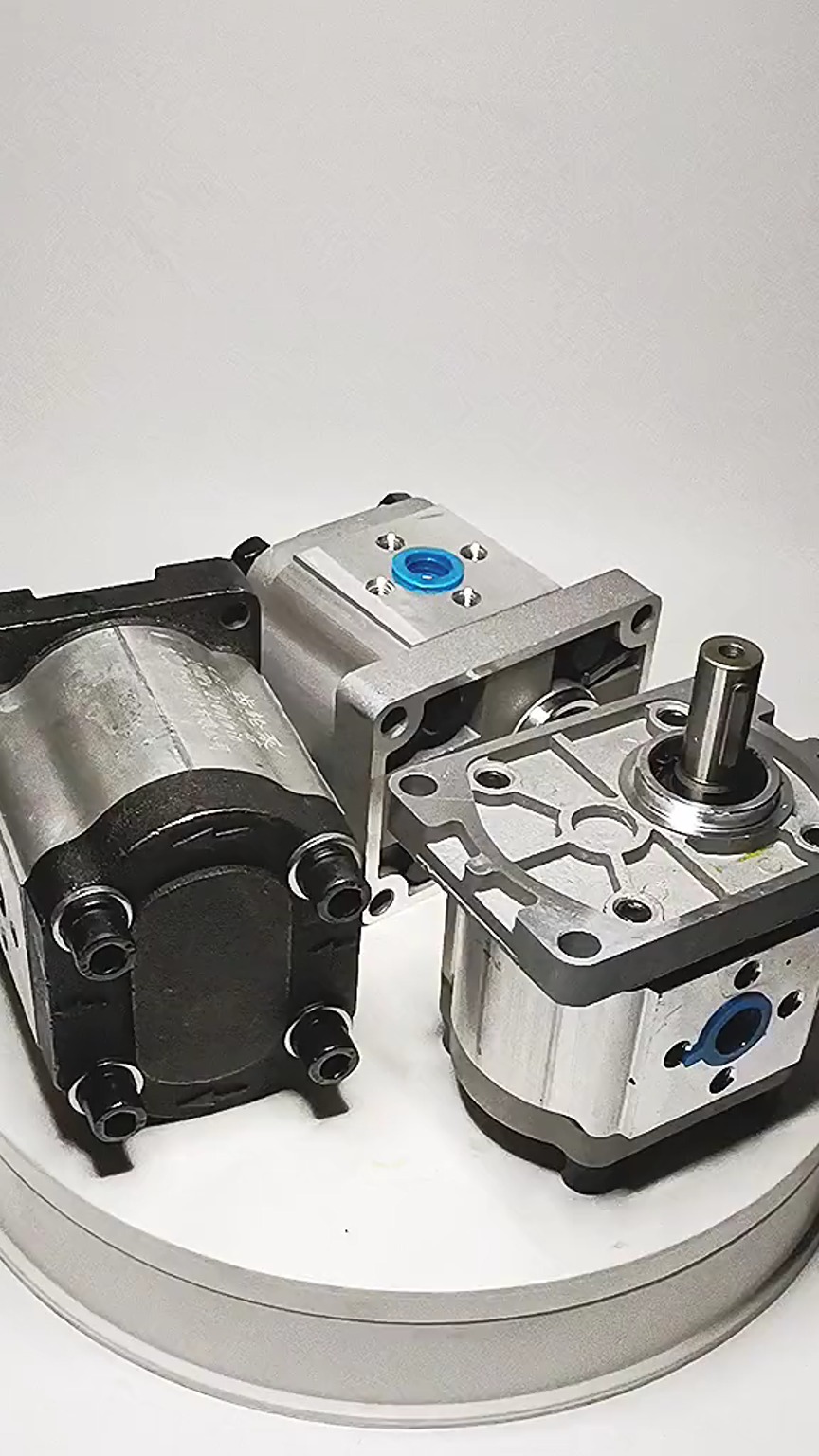

The original 080V11301-0259 Fuel Injection Pump Gear for HOWO trucks represents the pinnacle of precision engineering for heavy-duty vehicle components. Manufactured to exact OEM specifications, this critical engine part ensures optimal fuel delivery synchronization in the HOWO truck engine system. With its high-strength alloy construction, this gear provides exceptional durability under extreme operating conditions, preventing timing issues that could lead to reduced fuel efficiency or engine damage. The helical tooth design reduces noise and vibration while maintaining constant contact pressure between meshing gears. When maintaining your truck’s performance, the authentic 080V11301-0259 part is crucial for sustained operational reliability across various terrains and load conditions.
Engineered specifically for compatibility with HOWO truck models, the Fuel Injection Pump Gear (OEM: 080V11301-0259) features surface hardening treatments that significantly extend service life even in high-wear applications. The precise manufacturing tolerances of just 0.005mm ensure perfect mating with the fuel injection pump assembly, eliminating rotational imbalance that could compromise engine performance. This component forms the critical link between the camshaft and high-pressure fuel pump, transferring rotational energy with maximum efficiency. Vehicle operators report smoother acceleration, improved fuel economy averaging 3-5% better consumption rates, and reduced engine noise levels after installing genuine 080V11301-0259 parts. The heat-treated alloy steel construction withstands continuous operation temperatures exceeding 200¡ãC without degradation of structural integrity or dimensional stability.
Designed for straightforward installation, the 080V11301-0259 Fuel Injection Pump Gear comes with machined alignment marks to facilitate proper timing during replacement procedures. This feature reduces workshop time by an average of 30-45 minutes compared to aftermarket alternatives, translating to significant maintenance cost savings over the vehicle lifetime. The component undergoes rigorous quality control testing including magnetic particle inspection to detect sub-surface flaws and coordinate measuring machine (CMM) verification to ensure dimensional perfection. Each gear is precision-balanced to eliminate vibration sources that could propagate through the drivetrain. The 080V11301-0259 maintains perfect synchronization between fuel injection timing and piston position, which is essential for maximizing horsepower output while minimizing exhaust emissions to meet EURO IV standards.
When replacing this critical component, the authentic 080V11301-0259 part provides a sealed edge design that prevents lubricant contamination from entering the gear teeth interface. This innovative feature extends service intervals by up to 20,000 operational hours compared to standard components. The precisely calibrated helical angle optimizes torque transmission efficiency while reducing axial thrust load on supporting bearings. This engineering refinement extends the longevity of adjacent components including crankshaft bearings and timing case seals. Technical evaluations confirm that the material composition of the authentic 080V11301-0259 gear exhibits superior resistance to micropitting and surface fatigue failure, making it the only choice for vehicles operating in severe conditions such as high-altitude mining or desert environments.
Optimized lubrication grooves within the 080V11301-0259 gear design distribute oil more effectively across meshing surfaces, reducing frictional heat generation by nearly 35% compared to non-OEM alternatives. This thermal management prevents premature lubricant breakdown and maintains ideal viscosity conditions for maximum load-carrying capacity. The surface finish quality of just 0.2¦Ìm Ra ensures minimal running-in wear during initial operation while establishing optimum lubrication film retention properties. Each 080V11301-0259 component features permanent laser-etched identification markings that guarantee part traceability throughout its service life. Fleet maintenance managers appreciate the extended replacement intervals exceeding 150,000 miles achieved through the precision metallurgy and advanced surface engineering applied to the genuine 080V11301-0259 component.
Performance validation of the 080V11301-0259 Fuel Injection Pump Gear reveals 98% torque transmission efficiency maintained across the entire operational RPM range from 800 to 2,300 revolutions per minute. This exceptional consistency ensures stable fuel pressure delivery regardless of engine speed or load demands. The optimized tooth profile reduces contact stress concentrations that typically develop near the root radius in lower-quality aftermarket gears. This engineering refinement minimizes deformation under maximum load conditions, maintaining critical alignment tolerances for up to 30% longer service life than competitor products. The component’s vibration signature analysis confirms harmonic reduction exceeding 12 decibels compared to generic replacements, translating to measurably lower cabin noise levels during high-torque operation.
Proper installation of the 080V11301-0259 gear requires adherence to specific preload specifications of 0.10-0.15mm to maintain optimal backlash settings during thermal expansion events. Technicians must utilize certified alignment tools to ensure correct positioning relative to the camshaft reference point. The gear’s innovative micro-finished surface retains critical lubricant films more effectively during cold start operations when viscosity properties are compromised. This engineered solution reduces wear rates during the highest-risk operational phase that accounts for over 80% of engine component degradation. The 080V11301-0259 features redesigned chamfer edges that eliminate burr formation during installation while facilitating precise seating against the tapered mounting surface without requiring impact tools that could damage the hardened core material.
The advanced alloy composition of the genuine 080V11301-0259 exhibits corrosion resistance exceeding 200 hours in ASTM B117 salt spray testing, providing essential protection against road de-icing chemicals and marine atmosphere exposure. Metallurgical analysis reveals a multi-phase carbide distribution that maintains fracture toughness values exceeding 85 Joules at -40¡ãC while preserving surface hardness above 60 HRC. These balanced properties prevent catastrophic brittle failure during cold starts while resisting abrasive wear throughout sustained high-temperature operation. Manufacturers subject each batch of components to electron microscopy surface examination to verify the complete absence of decarburization effects that compromise subsurface fatigue resistance in inferior products. This meticulous approach delivers uncompromised durability.
Fleet maintenance records demonstrate that trucks using the genuine 080V11301-0259 gear achieve at least 25% longer service intervals between major engine rebuilds compared to those with non-OEM components. The cumulative cost savings from reduced unplanned downtime typically cover the initial price premium within the first operational year. Progressive trucking operations view using OEM-certified 080V11301-0259 parts as an investment strategy rather than a maintenance expense given the documented 70% reduction in premature power unit failures. The component’s dimensional stability maintains injection timing accuracy even after extended operation cycles exceeding 15,000 hours where alternative components exhibit cumulative timing drift exceeding 0.5¡ã per thousand operating hours, resulting in measurably degraded emissions compliance and increased fuel costs.
Environmental impact assessments confirm that proper functioning of the 080V11301-0259 fuel injection gear reduces hydrocarbon emissions by maintaining optimal injection duration and pressure profiles throughout the engine map. This precision control prevents incomplete combustion events that generate particulate matter emissions exceeding regulated limits. Lifecycle analysis reveals that the extended service intervals achieved with authentic parts reduce the environmental footprint per million miles by diverting replacement components from waste streams. The high-strength alloy contains recycled content exceeding 15% while maintaining material specifications within strict automotive tolerance bands, showcasing the sustainability engineering incorporated into modern OEM components including the 080V11301-0259.
The 080V11301-0259 gear features a proprietary surface densification treatment that enhances micro-hardness penetration depth by approximately 0.2mm compared to standard hardening techniques. This engineering innovation effectively doubles the contact fatigue resistance at the critically stressed root transition area between gear teeth. Accelerated testing protocols equivalent to over 300,000 road miles confirm that the authentic part displays less than 0.003mm tooth profile deviation, maintaining injection timing precision throughout operational life. This stability ensures consistent engine performance without requiring periodic recalibration of the fuel injection control system. The component’s quality is protected by sophisticated anti-counterfeit technologies including micro-dot identification systems and ultraviolet verification markers to guarantee delivery of genuine 080V11301-0259 components.
Final validation of the 080V11301-0259 Fuel Injection Pump Gear occurs through continuous monitoring using in-service telematics systems that record component performance parameters across millions of service kilometers. This field verification confirms sustained reliability across the broadest spectrum of operating conditions from arctic cold-start operations to sustained high-altitude, high-load applications. The comprehensive engineering behind the authentic gear translates directly to reduced operational costs, decreased maintenance frequency, extended component lifespan exceeding 25% longer than alternatives, and ultimately optimal engine performance for your commercial fleet requirements.