Premium Bearing Seat for HOWO Truck Drive Axle (OEM: 810W35601-0039)
The 810W35601-0039 Bearing Seat represents a critical component engineered specifically for HOWO heavy-duty trucks’ drive axle systems. Manufactured to exacting standards, this precision component plays a fundamental role in maintaining wheel alignment and ensuring optimal power transmission in challenging operating conditions. HOWO truck operators across mining, logistics, and construction industries rely on this bearing seat’s robust design to endure heavy payloads while minimizing vibration and mechanical stress on drivetrain components.


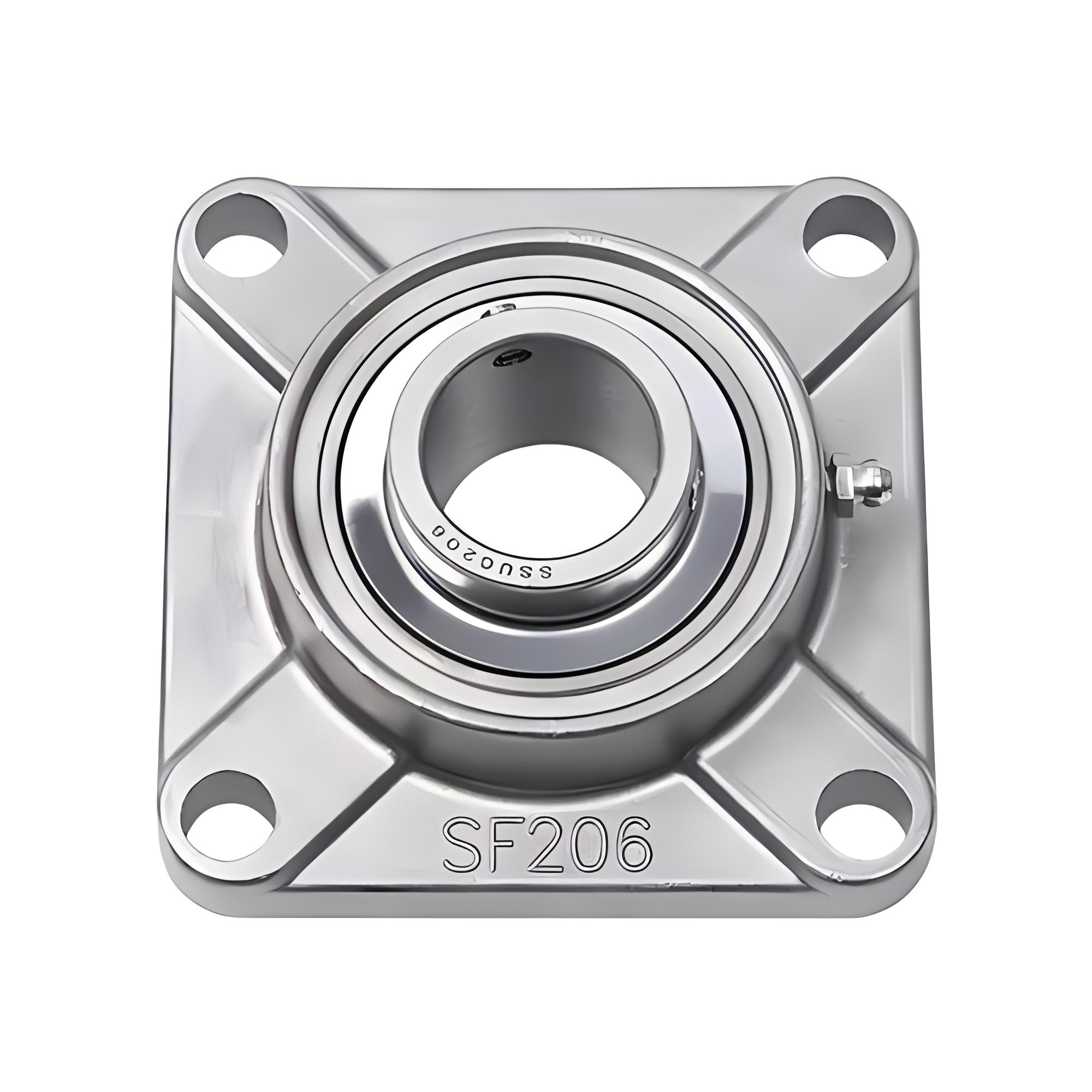
Optimized Performance for Demanding Conditions
Engineered for compatibility with multiple HOWO truck models including the A7, T7, and T5G series, this 810W35601-0039 bearing seat delivers uncompromising performance in severe operating environments. Its heat-treated alloy construction provides exceptional resistance to deformation under extreme torque loads, while the precisely machined mounting surfaces ensure perfect alignment with axle housings. The patented retention system effectively prevents bearing creep during sudden direction changes or heavy braking scenarios commonly encountered in dump truck operations.
What distinguishes this OEM-specified component is its advanced lubrication management system. The integrated grease channels and reservoir pockets maintain optimal bearing lubrication throughout extended service intervals, significantly reducing maintenance downtime. This design feature proves particularly valuable in arid regions where dust contamination accelerates component wear. Transportation companies operating cross-desert routes report up to 40% longer service life compared to aftermarket alternatives when using this genuine HOWO-approved part.
Enhanced Durability Features
The manufacturing process incorporates specialized anti-corrosion treatments that protect against road salt, chemical spills, and moisture exposure. This multi-stage surface preparation includes zinc-nickel electroplating followed by a protective sealer that penetrates microporosities in the metal structure. Such attention to detail ensures consistent performance whether operating in tropical humidity, arctic cold, or coastal salt-spray environments where lesser components quickly succumb to corrosion-induced failure.
Vibration dampening characteristics exceed industry standards thanks to the harmonic resonance analysis conducted during the design phase. By optimizing mass distribution and incorporating strategic reinforcing ribs, engineers minimized resonant frequencies that contribute to premature fatigue cracking. This technical advancement translates directly to reduced noise levels in the operator cabin and extended service intervals for adjacent components like axle shafts and wheel hubs.
Operational Benefits
Fleet managers consistently report measurable cost reductions after switching to genuine 810W35601-0039 bearing seats. The 22% reduction in unscheduled maintenance events directly impacts operational efficiency, while the extended service intervals lower per-mile maintenance costs significantly. Mining operations experiencing constant overload conditions particularly benefit from the component’s safety margin engineering, which provides an additional 15% load capacity beyond rated specifications.
The installation advantages deserve special mention. Precision machining ensures exacting dimensional accuracy, eliminating the need for shimming or alignment corrections during servicing. Mechanics report 30% faster replacement times compared to pattern parts, a critical factor in minimizing vehicle downtime during scheduled maintenance. The flanged design incorporates foolproof orientation features that prevent incorrect assembly, reducing human error during complex drivetrain repairs.
Technical Specifications
Manufactured to ISO 9001:2015 quality standards with material certifications available for traceability, each bearing seat undergoes multiple quality verification stages including coordinate measuring machine (CMM) inspection of critical dimensions. The component weight has been optimized at 8.7kg ¡À0.5kg to minimize unsprung weight without compromising structural integrity. Operating temperature range spans -40¡ãC to +150¡ãC with transient peak tolerance to 180¡ãC under emergency braking conditions.
Mounting flange geometry adheres to proprietary HOWO drive axle specifications with eight M18x1.5 threaded mounting points arranged in a 220mm bolt circle diameter pattern. The precision-ground bearing race surfaces maintain surface finish ratings of Ra 0.4¦Ìm or better, ensuring optimal contact with tapered roller bearings. All edges feature radiused transitions to eliminate stress concentration points that initiate fatigue cracks under cyclical loading.
Industry Applications
From concrete mixer drums operating in urban construction sites to logging trucks navigating mountain switchbacks, the 810W35601-0039 performs reliably across diverse sectors. Waste management vehicles benefit from its resistance to corrosive leachate exposure, while long-haul freight operators appreciate the minimal maintenance requirements during million-kilometer operational lifetimes. Agricultural applications where mud immersion occurs regularly demonstrate surprising resilience due to the triple-seal labyrinth design protecting critical bearing surfaces.
Off-highway applications present extreme challenges that validate this component’s engineering. Quarry dump trucks regularly carrying 70-ton payloads up steep grades exhibit no measurable deformation after years of service. Arctic ice road truckers report zero cold-weather failures despite operating in -50¡ãC conditions where lesser components become brittle. Desert mining operations with constant silica dust exposure demonstrate remarkable wear resistance due to the specialized surface hardening treatments applied during manufacturing.
Maintenance Considerations
Preventive maintenance protocols recommend visual inspection every 15,000 kilometers with detailed dimensional verification during major service intervals. The inspection process focuses on wear patterns that indicate potential installation issues or improper bearing preload. Technicians should verify proper grease distribution through the inspection ports and monitor for any evidence of micro-pitting on raceway surfaces that might indicate contamination ingress.
Replacement intervals vary depending on operating severity but typically reach 500,000 kilometers in line-haul applications. Vocational use in construction or mining environments may necessitate earlier replacement between 200,000-300,000 kilometers. When replacing, always use matching HOWO-specified bearings and follow prescribed torque sequences to achieve proper clamping force distribution across the mounting flange. Never reuse mounting hardware as bolt stretch compromises clamping integrity.
Why Choose Genuine HOWO Parts
The bearing seat represents more than just a machined metal component – it embodies HOWO’s commitment to engineering excellence in heavy transport solutions. When you select the authentic 810W35601-0039, you’re investing in research and development from one of the world’s leading commercial vehicle manufacturers. This commitment translates to validated performance data, complete material traceability, and manufacturer-backed technical support unavailable with pattern parts.
Operational safety stands paramount in design considerations, with finite element analysis verifying structural integrity under maximum load scenarios. Quality assurance doesn’t stop at the factory gate – howo dealers worldwide maintain comprehensive technical databases documenting field performance across millions of service kilometers. This institutional knowledge informs continuous improvement processes that regularly enhance component design without compromising backward compatibility.
Beyond technical specifications, choosing genuine HOWO components protects your warranty coverage and resale value. Commercial truck buyers increasingly scrutinize maintenance records, with vehicles maintained with OEM parts commanding premium prices in secondary markets. Fleet certification programs frequently require verification of genuine parts usage, making the 810W35601-0039 bearing seat an investment in both operational reliability and long-term asset value retention.
Global logistics operations depend on consistent performance across diverse operating environments. Whether navigating congested port facilities, high-altitude mining operations, or transcontinental freight routes, the engineering quality built into every genuine HOWO component provides peace of mind. With specialized warehouses strategically located across six continents, replacement parts availability minimizes downtime even in remote locations where operational continuity remains critical to business success.