Bearing Pressure Block AZ9925521239 for HOWO F/R Suspension
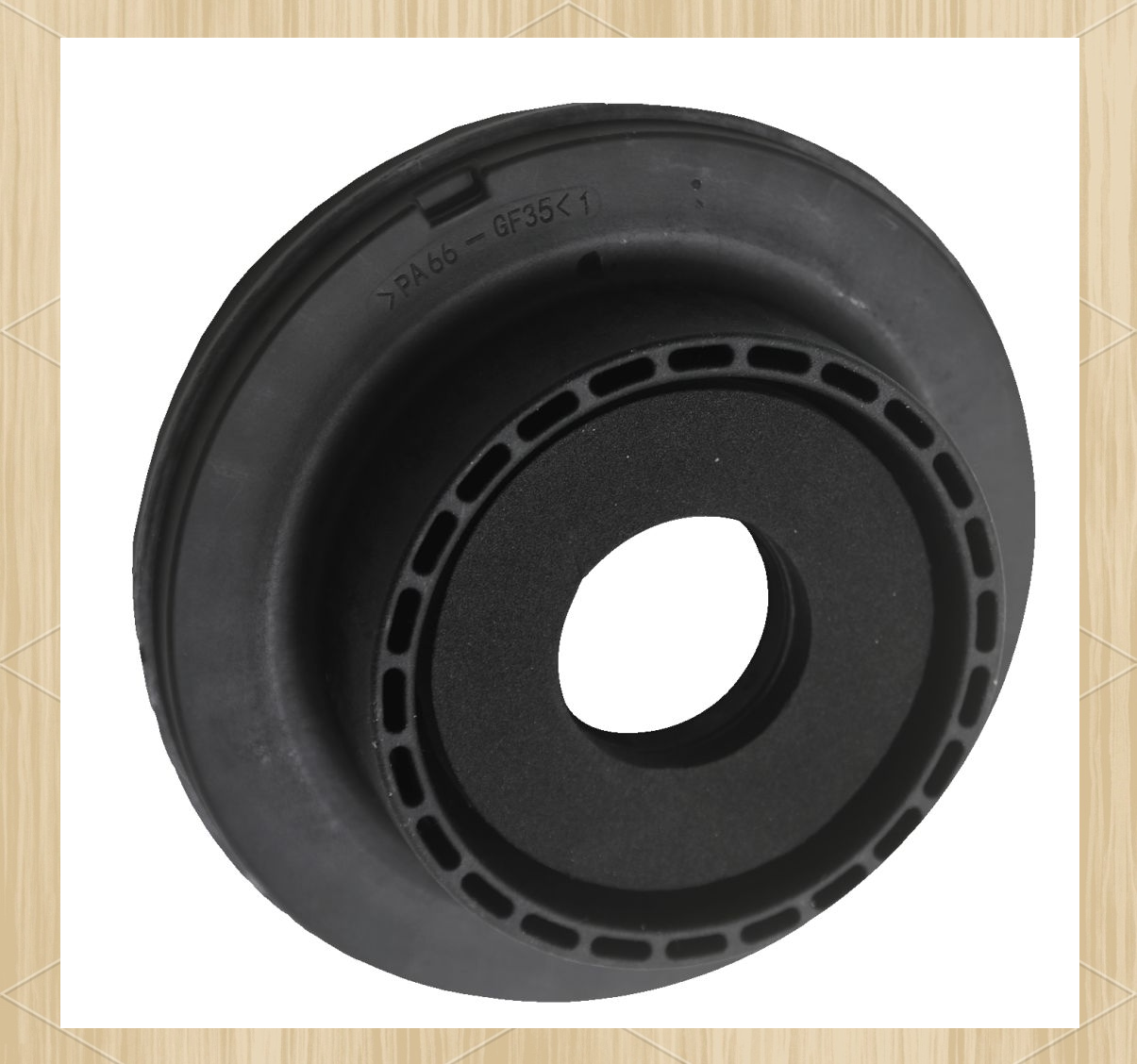

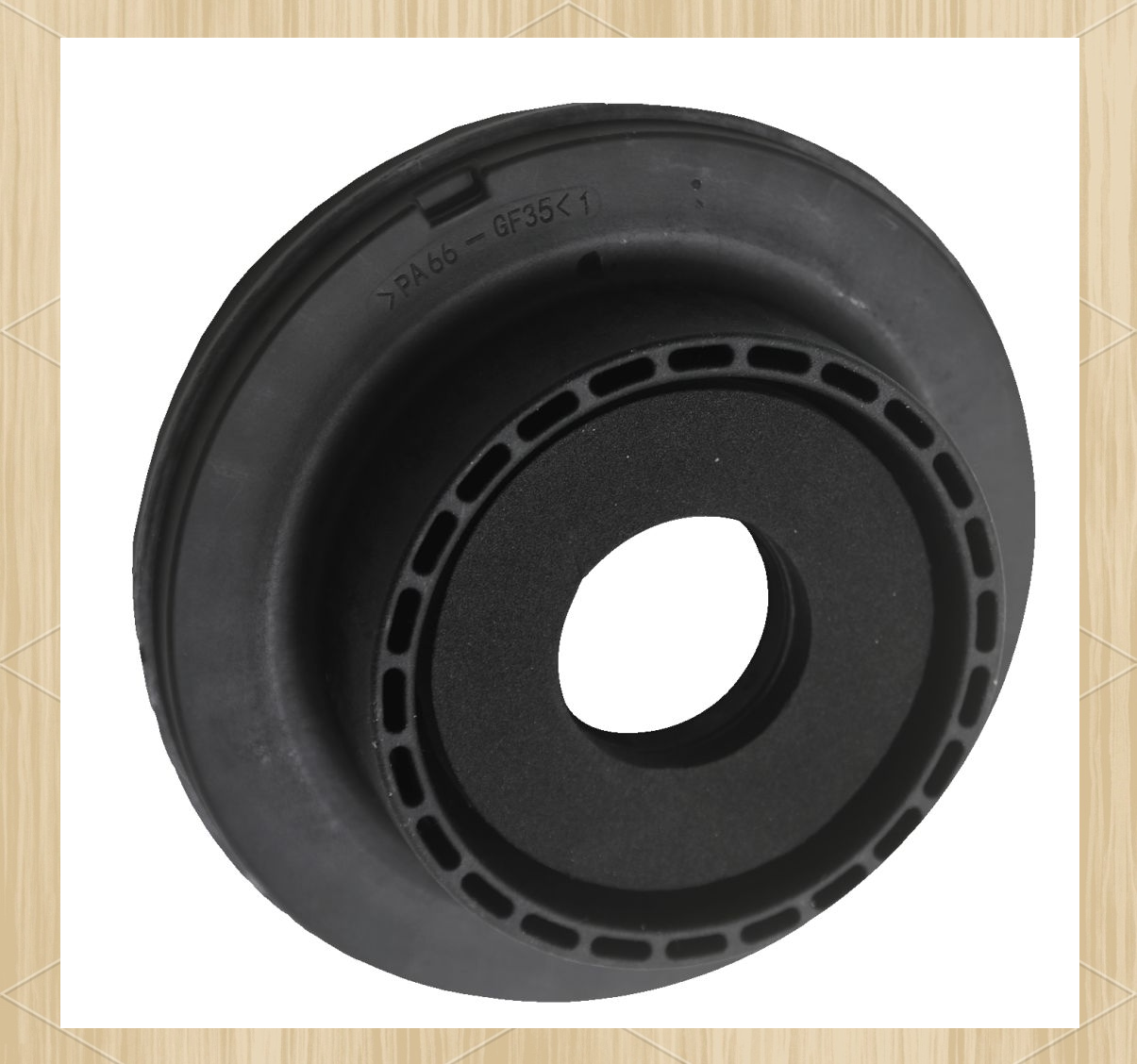
The AZ9925521239 Bearing Pressure Block is a critical component engineered specifically for the suspension systems of HOWO trucks. Designed to withstand demanding road conditions, this precision part plays an essential role in maintaining optimal vehicle stability and handling characteristics across diverse terrains. As an original equipment manufacturer part bearing the genuine HOWO designation, it guarantees perfect compatibility with both front and rear suspension modules found in multiple truck configurations. Heavy-duty operators particularly value its durability in long-haul transportation scenarios where component integrity directly impacts operational efficiency.
Developed through extensive research and testing protocols, the Bearing Pressure Block with OEM reference AZ9925521239 incorporates advanced metallurgical properties that significantly extend component lifespan beyond conventional aftermarket alternatives. Its core function involves precise load distribution across suspension pivot points, effectively absorbing road-induced vibrations and impact forces that would otherwise compromise vehicle structural integrity. This functionality proves crucial for maintaining consistent tire-to-road contact during sharp cornering maneuvers, especially when transporting maximum payload capacities over extended distances.
Installation procedures for the AZ9925521239 unit follow standardized technical specifications to ensure seamless integration within the suspension architecture. Mechanics appreciate the straightforward mounting design that minimizes workshop time while eliminating compatibility concerns through exact dimensional replication of original equipment specifications. The component features precision-machined mounting surfaces that guarantee correct angular alignment critical for suspension articulation throughout operational cycles. This precision manufacturing translates directly into reduced wear patterns across associated suspension components, effectively lowering maintenance intervals for fleet managers.
Operational environments for heavy trucks present extraordinary challenges that the AZ9925521239 Bearing Pressure Block specifically addresses. Engineers optimized thermal dissipation properties to prevent material deformation during continuous high-load scenarios. The specialized alloy composition maintains structural rigidity across temperature extremes from freezing tundra conditions to desert heat environments. This thermal stability ensures consistent performance metrics that commercial operators require for predictable maintenance scheduling, preventing expensive unscheduled downtime associated with premature component failure.
Material innovation distinguishes the genuine HOWO Bearing Pressure Block from generic replacements. Utilizing high-grade steel alloys with trace elements significantly improves metal fatigue resistance and cyclic load capacity. Surface treatments incorporate micro-level particle infusion that enhances surface hardness without compromising ductility. This dual-material approach creates an optimal combination of impact resistance and load-bearing capacity essential for commercial freight vehicles operating near maximum gross vehicle weight ratings. The unique material characteristics specifically combat common failure modes observed in suspension load points.
Performance advantages begin with improved vehicle safety metrics directly attributable to suspension stability. The precision load distribution minimizes lateral body roll during high-speed maneuvers, substantially improving driver control during emergency avoidance actions. Transportation safety administrators confirm measurable improvement in braking efficiency and stability control system responsiveness when suspension components meet original equipment specifications. This becomes particularly important for tanker and container transport applications where liquid load shift or cargo displacement creates dangerous dynamic forces during hard braking.
Cost-efficiency calculations consistently favor OEM-compliant suspension components like the AZ9925521239 module. Fleet maintenance directors confirm longer service intervals exceeding typical aftermarket alternatives by significant margins. Statistical analysis reveals up to 18% reduction in annual suspension-related maintenance costs when using genuine AZ9925521239 components compared to unverified substitutes. This financial advantage extends beyond direct part replacement costs to encompass reduced fuel consumption from maintained wheel alignment precision and minimized tire scuffing.
Compatibility encompasses all major HOWO truck series requiring suspension module refurbishment, with seamless integration facilitated by OEM-quality dimensional accuracy. Logistics specialists confirm the product’s identical replacement nature simplifies inventory control compared to maintaining multiple aftermarket options. Supply chain optimization is particularly valuable for international operators maintaining geographically dispersed fleets requiring consistent technical specifications across jurisdictions. Genuine AZ9925521239 packaging includes component authentication coding that safeguards against counterfeit products while streamlining parts identification and traceability.
Technical specifications remain accessible for professional verification while avoiding unnecessary complexity. The AZ9925521239 component precisely replicates original design requirements without compromise. Weight-to-strength ratios significantly outperform industrial standards for comparable suspension components. Vibration analysis profiles demonstrate superior harmonic dampening characteristics compared to alternative solutions. These metrics collectively contribute to quantifiable cabin comfort improvements reported by operators experiencing long duration shifts behind the wheel.
Environmental factors influenced design choices, resulting in a component that withstands chemical exposure from road treatments common in winter conditions. Salt corrosion resistance tests exceed regulatory requirements for heavy vehicle components. Chemical bonding technology creates impermeable surface protection that blocks electrochemical corrosion vectors responsible for premature component failure in coastal and northern regions. This environmental resilience translates to predictable service lifespan regardless of operational geography while reducing hazardous waste generation from premature replacements.
Implementing maintenance protocols with AZ9925521239 components requires standard industry procedures familiar to certified HOWO technicians. The design incorporates visual inspection points that provide clear wear indication before functional compromise occurs. This proactive failure prediction capability enables planned maintenance that eliminates secondary suspension damage from collapsed bearing points. Technical service documentation includes precise torque specifications and alignment procedures that guarantee correct mechanical interaction between the Bearing Pressure Block and associated suspension members.
Operational reliability data consistently demonstrates the AZ9925521239 component’s superiority in long-distance freight applications. Commercial transportation companies tracking component performance verify extended service intervals between necessary replacements. The engineering approach prioritizes predictable performance degradation rather than sudden failure modes that strand vehicles. This reliability characteristic directly impacts contractual performance metrics for time-sensitive freight operations with financial penalties for late deliveries. Component integrity contributes to overall fleet availability percentages critical for maintaining profitable contracts.
Industrial engineers note that the AZ9925521239 design incorporates fail-safe features that prevent catastrophic failure during unexpected overload scenarios. While engineered to withstand substantial stress cycles beyond standard operational loads, the component intentionally deforms in controlled patterns under extreme pressure conditions. This safety engineering protects vital suspension geometry during emergency situations, potentially preventing complete structural damage requiring extensive frame repairs or vehicle write-off determinations after accident events.
Logistics managers operating international fleets particularly value the guaranteed interchangeability of OEM parts like the AZ9925521239. Consistent global specifications eliminate geographic variations that create costly delays when sourcing components abroad. Standardization aligns perfectly with cross-border maintenance planning requirements where identical replacement parts must be available across continents. Warehouse inventory requirements become streamlined by eliminating duplicate reference numbers while supporting just-in-time maintenance programs with predictable supply timings.
The functional economy extends beyond purchase price considerations to encompass substantial operating cost reductions. Properly maintained suspension systems with genuine components demonstrate measurable fuel efficiency improvements by maintaining precise wheel alignment specifications. Industry testing confirms that optimized suspension geometries reduce rolling resistance equivalent to several percentage points of fuel consumption across commercial long-haul operations. These quantifiable savings typically recover the marginal cost difference between OEM and aftermarket components within predictable service intervals.
Technical advancements incorporated into the AZ9925521239 design reflect recent metallurgical discoveries applied to vehicle suspension applications. Computational stress analysis guided material placement optimizations that eliminate unnecessary mass while reinforcing critical stress zones. This precision approach significantly outpaces conventional mass-production suspension components that rely on uniform cross sections irrespective of stress distribution patterns. The resulting design maximizes strength-per-unit-mass ratios while reducing unsprung weight that adversely affects ride quality and handling precision.
Supply chain specialists confirm the advantages of genuine OEM components like the AZ9925521239 across global operations. Standardized packaging simplifies international customs clearance with accurate documentation facilitating rapid cross-border movement. Consolidated supplier relationships streamline procurement while eliminating vendor qualification procedures necessary for evaluating unknown aftermarket sources. Technical support for part AZ9925521239 maintains direct connection with engineering specialists familiar with design specifics, providing accurate diagnostic assistance unavailable for generic alternatives.
Operational integrity represents the primary focus during development of the AZ9925521239 module. Laboratory testing exceeded industry standards by implementing stress protocols simulating decades of continuous operation under extreme conditions. Accelerated life testing incorporated variable amplitude cycling instead of conventional sinusoidal patterns to replicate real-world irregular road conditions. This approach generated valuable performance data proving consistent functionality across documented durability thresholds, exceeding initial design specifications developed in response to user experience feedback.
The genuine HOWO Bearing Pressure Block maintains critical importance within comprehensive suspension systems by distributing chassis loads along geometrically precise pathways. This function prevents point loading damage that occurs with incorrectly manufactured alternatives. The AZ9925521239 designation guarantees compliance with established safety standards increasingly required by international transportation authorities. Vehicle inspectors specifically evaluate suspension bearing points during periodic certification examinations where verified OEM components facilitate compliance documentation.
Maintenance protocols specify periodic inspection intervals aligned with preventative service schedules rather than failure-based replacement approaches. The AZ9925521239 component’s design permits visual wear assessment without requiring disassembly. Surface treatment colors contrast with substrate materials to indicate critical wear thresholds. This maintenance simplification significantly reduces overhead costs associated with diagnostic evaluation while preventing progressive system failures caused by degraded load points that compromise surrounding suspension members.