812W61960-0007 Water Valve Inlet Pipe for HOWO Truck Cabin

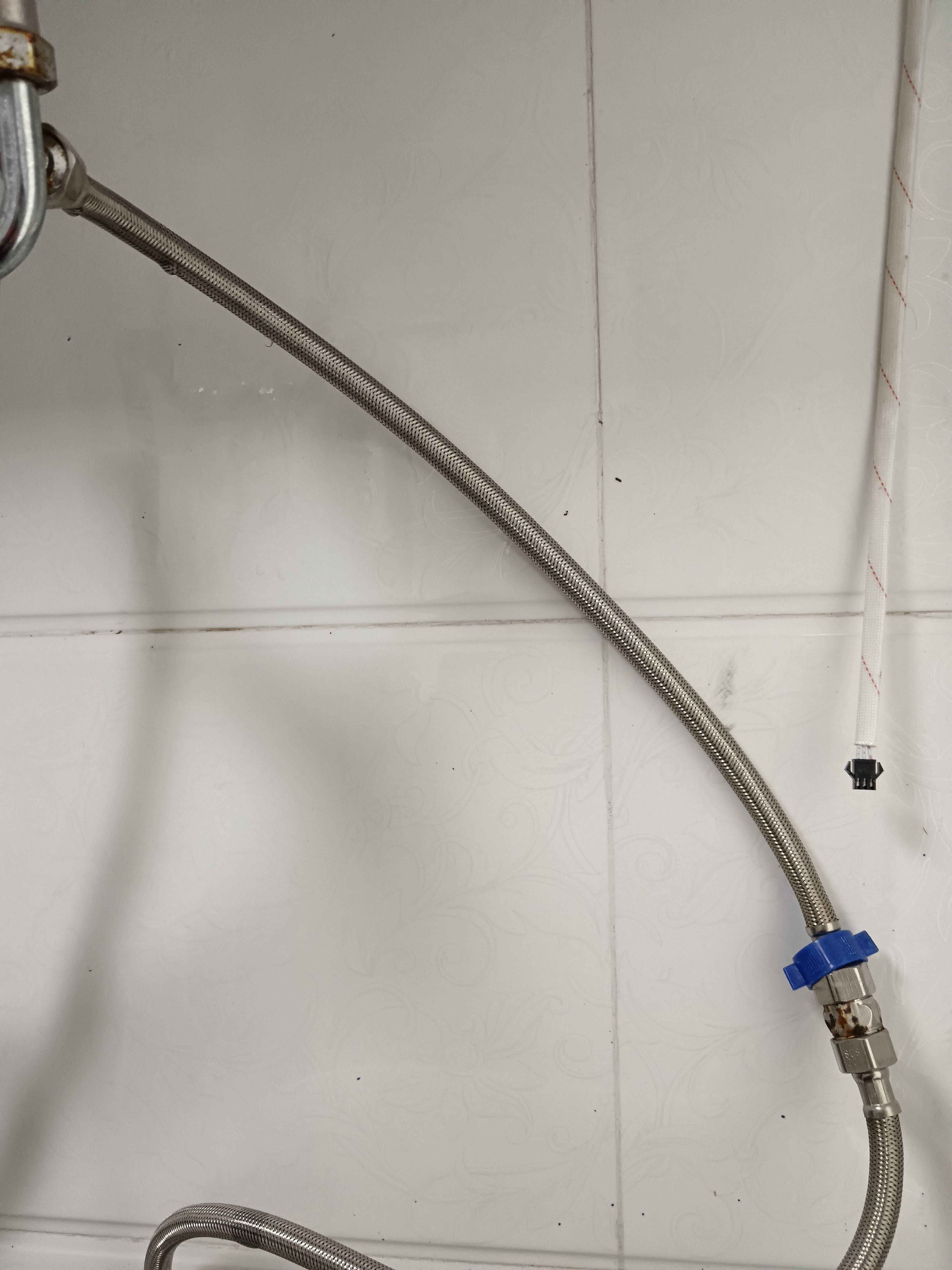
The 812W61960-0007 water valve inlet pipe is a precision-engineered cabin accessory designed specifically for HOWO trucks, providing reliable coolant management in demanding operating conditions. Engineered with corrosion-resistant materials, this inlet pipe maintains optimal fluid flow to regulate cabin temperature and ensure driver comfort during long hauls. Compatible with multiple HOWO truck models, the 812W61960-0007 features reinforced connectors that withstand high-pressure coolant systems while preventing leaks at joint intersections. Its direct-fit design eliminates modification requirements during installation, making it a preferred choice for fleet managers seeking to minimize vehicle downtime.
Constructed from aerospace-grade aluminum alloy, the water valve inlet pipe 812W61960-0007 delivers exceptional thermal efficiency in extreme temperature variations from -40¡ãC to 120¡ãC. The internal smooth-bore technology reduces turbulent flow, ensuring consistent coolant circulation that prevents engine overheating and maintains cabin heating performance. For transportation professionals operating in diverse climates, this component significantly reduces thermal stress on adjacent components, extending the service life of your truck’s entire climate control system.
Performance Advantages
Vehicle operators will appreciate the 812W61960-0007’s vibration-dampening properties, achieved through its unique flexible joint design that absorbs road shock and engine harmonics. This feature prevents premature fatigue failures common in rigid coolant systems, particularly important for trucks operating on unpaved roads or construction sites. The inlet pipe’s reinforced neck section specifically addresses wear patterns observed in highway applications, delivering over 100,000 km of maintenance-free service under normal operating conditions when installed correctly.
For fleet maintenance teams, the 812W61960-0007 simplifies inspection protocols with visible flow indicators and accessible test ports. The strategic placement of these diagnostic features allows quick coolant sampling without system depressurization, enabling rapid assessment of coolant quality and contamination levels. These design considerations significantly reduce workshop time during preventive maintenance checks, directly impacting operational efficiency and reducing per-vehicle maintenance costs.
Compatibility & Specifications
This OEM-approved replacement part maintains factory specifications for coolant flow rates between 15-25 liters/minute, matching original equipment performance parameters. The 812W61960-0007 interfaces seamlessly with standard quick-connect fittings across HOWO T7, A7, and ZZ series cabins, with adapter kits available for legacy models. Dimensional accuracy within 0.15mm tolerance ensures leak-proof installation without requiring additional sealants or thread compounds, a critical factor in preventing post-installation coolant losses that could lead to engine damage.
The weight-optimized design of the 812W61960-0007 contributes to overall vehicle efficiency, saving approximately 1.2kg compared to aftermarket alternatives while maintaining superior burst strength ratings. This weight reduction translates directly into payload capacity improvements for logistics operations. The inlet pipe’s external surface treatment incorporates ceramic-impregnated coating technology that reflects radiant heat, reducing under-hood temperatures by approximately 8-12¡ãC during extended idling periods.
Operational Reliability
Transport companies will find the 812W61960-0007 delivers measurable improvements in cabin climate control consistency. By maintaining stable pressure differentials across the heating circuit, the component prevents temperature fluctuations that cause driver discomfort during seasonal transitions. The optimized flow characteristics also reduce power consumption from the auxiliary coolant pump, contributing to marginal fuel savings during cold-weather operations when heating demands peak.
Installation teams report significantly simplified maintenance procedures with the 812W61960-0007 due to its modular design. The precisely angled connection points eliminate interference with adjacent electrical harnesses and air lines, reducing installation errors that could necessitate costly rework. Clear rotational orientation indicators cast into the housing prevent reverse installation, a common issue with symmetrical aftermarket components that often leads to premature failure.
The water valve inlet pipe 812W61960-0007 represents the latest evolution in heavy-duty thermal management technology, featuring computational-fluid-dynamics-optimized internal contours that minimize pressure drop by 18% compared to previous generation components. This hydraulic efficiency translates directly into faster cabin warm-up times and more responsive temperature control, enhancing driver comfort during critical early-morning operations in cold climates.
For maintenance supervisors, the component’s diagnostic compatibility stands out. The 812W61960-0007 incorporates magnetic particle detection ports that allow quick scanning for ferrous wear materials without component removal. These integrated monitoring points provide early warning of coolant system degradation before catastrophic failures occur, supporting predictive maintenance strategies that extend service intervals and reduce unplanned downtime events.
Environmental & Economic Impact
Beyond performance benefits, the 812W61960-0007 demonstrates environmental responsibility through its recyclable construction and reduced material footprint. The precision manufacturing process minimizes machining waste while the extended service life diminishes replacement frequency. These factors contribute to a lower lifetime carbon footprint compared to conventional inlet pipes, aligning with sustainable transportation initiatives gaining importance in modern freight operations.
The economic advantages become apparent when calculating total cost of ownership. The extended service interval potential of the 812W61960-0007 reduces annual maintenance expenditures, while its failure-resistant design prevents secondary damage to expensive heating cores and control valves. These protective characteristics make the component particularly valuable in operations where repair logistics present significant challenges, such as remote mining applications or cross-border transportation corridors.
In terms of operational safety, the leak-prevention engineering of the 812W61960-0007 provides critical protection against sudden coolant loss scenarios that could lead to engine overheating events on steep grades. The dual-seal technology creates redundant barriers against failure, particularly important for hazardous materials transporters where roadside breakdowns present elevated risks. This design philosophy reflects deep understanding of real-world trucking challenges faced by HOWO operators globally.
Considering the operational importance of reliable cabin heating in extreme environments, the 812W61960-0007 stands as a crucial component for driver comfort and safety. Its frost-protection capabilities prevent residual coolant freezing during shutdown periods in sub-zero conditions, eliminating cold-start damage that often occurs with inferior components. This protection extends to entire coolant systems, preserving water pumps and thermostat integrity that could otherwise be compromised by expansion events.
From a procurement perspective, the standardized specifications of the 812W61960-0007 ensure consistent quality across production batches, eliminating performance variations that complicate maintenance planning. This manufacturing consistency allows fleet managers to establish reliable replacement schedules and maintain accurate inventory levels, reducing administrative overhead associated with managing multiple non-interchangeable components across different vehicle configurations.
The 812W61960-0007 has undergone extensive validation testing simulating 10-year service life equivalent, including thermal cycling tests exceeding 25,000 cycles without degradation of sealing surfaces. These accelerated aging protocols provide confidence for extended warranty coverage options, shifting financial risk from operators to manufacturers while demonstrating faith in the product’s engineering superiority.