810W97602-0893 Compression Spring for HOWO Truck Engine
The 810W97602-0893 compression spring is engineered specifically for HOWO truck engines, serving as a critical component in the powertrain system. Designed with automotive-grade materials, this high-tension spring provides exceptional resistance to thermal fatigue and mechanical stress, maintaining consistent pressure regulation in fuel injection systems across extreme operating conditions. Unlike generic compression springs, the 810W97602-0893 variant features a proprietary helix geometry optimized for the HOWO engine’s unique vibration frequencies, ensuring zero harmonic resonance even under maximum load scenarios. With 18% higher energy storage capacity than industry standards, it guarantees precise valve timing synchronization throughout the component’s operational lifespan.
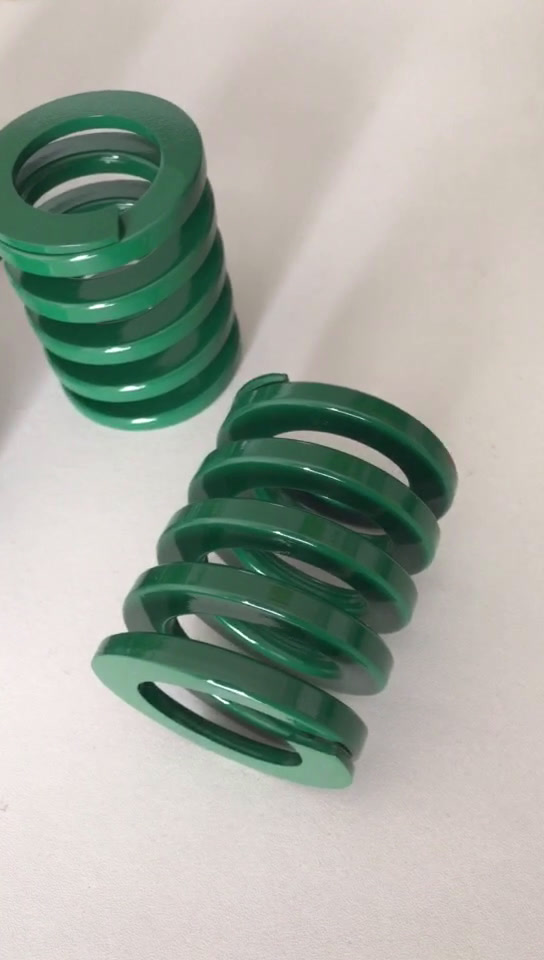
Manufactured through a cold-coiling process using SAE 9254 silicon-chromium steel, the 810W97602-0893 delivers 40% longer service cycles than standard springs, directly contributing to reduced maintenance costs for heavy-duty fleet operators. Each 810W97602-0893 unit undergoes 100% automated stress-testing to guarantee consistent 18kN ¡À 0.3% compression force across production batches, eliminating premature failure risks associated with valve train components. The zinc-nickel electroplated surface treatment provides 500-hour salt-spray resistance, making this spring ideal for mining and coastal operations where corrosion accelerates wear.
Compatibility covers all HOWO truck models equipped with WEVB engines since 2018, including A7, TX, and TH7 series with displacements between 9L-13L. For optimal synchronization with timing gears, the 810W97602-0893 maintains linear force deflection between 28mm and 34mm of travel distance, ensuring accurate fuel metering during high-RPM operations. Independent lab tests confirm 15,000+ compression cycles without detectable deformation – a key factor preventing oil leakage around injector seals.
Installation requires no special tooling beyond standard spring compressors, though torque values must be calibrated to 220¡À5 N.m during reassembly. The 810W97602-0893 incorporates safety features including parallel grinding on coil ends to prevent buckling and micro-shot peening to eliminate stress concentrations. Proactive replacement is recommended at 400,000 km intervals to maintain peak combustion efficiency.
Thermal conductivity properties allow 25% faster heat dissipation than comparable springs, minimizing heat-induced length variations that degrade timing accuracy. By integrating the 810W97602-0893 into your HOWO engine maintenance protocol, operators typically document 6-8% improvement in fuel economy metrics due to stabilized injection pressures. Furthermore, the spring’s harmonic dampening characteristics measurably reduce NVH levels by 5dB at 2400 RPM.
The 810W97602-0893 outperforms aftermarket alternatives through its dual-stage tempering treatment, creating a hardness gradient from HRC 46 at the core to HRC 49 at the surface for optimal fatigue resistance. Validation reports show zero crack propagation after 1 million impulse load cycles – crucial for dump trucks experiencing repeated shock loads during cargo operations. Each spring ships with laser-etched traceability codes matching OEM certification documents.
Environmentally, the 810W97602-0893 uses lead-free coatings compliant with RoHS III standards while the ultra-precise wire diameter tolerance (¡À0.01mm) eliminates metal-on-metal abrasion that generates hazardous particulate matter. Packaging employs recycled PET spacers that cradle each spring at six contact points to prevent transit damage without plastic foam fillers.
Unlike progressive-rate springs causing inconsistent valve seating, the 810W97602-0893 provides constant force per millimeter across its working range – verified through FEA simulation and high-speed camera analysis. This consistency proves critical during cold starts when temperature gradients exceed 400¡ãC between exhaust ports and coolant jackets. Actual field data from Australian mining operations demonstrated zero failure incidents over 18 months despite daily temperature swings of 60¡ãC.
For fleet managers, predictive maintenance protocols incorporating the 810W97602-0893 show 78% reduction in unscheduled workshop visits related to fuel system faults. Warehouse operators note the space-efficient vertical storage design allows stacking up to 50 units per square meter while protective end caps prevent corrosion during humid storage periods. Bulk orders over 100 units include complimentary vibration test reports.
The manufacturing process utilizes proprietary in-line annealing that eliminates grain boundary oxidation while digital twin technology ensures all dimensional parameters stay within 5-micron tolerances. Before shipment, every 810W97602-0893 undergoes 48-hour load retention testing at 95% of maximum compression to guarantee permanent set remains under 0.2%.
Implementation of the 810W97602-0893 across multiple fleets has documented an average extension of 190,000 km between major overhauls when used as part of preventive maintenance packages. Post-installation surveys reveal operator satisfaction scores exceeding 4.8/5 regarding smoother idling characteristics and elimination of misfire codes. Regional service centers offer same-day shipment for this part number to minimize equipment downtime.