712W25456-6200 Trailer ABS Power Harness Assembly for HOWO
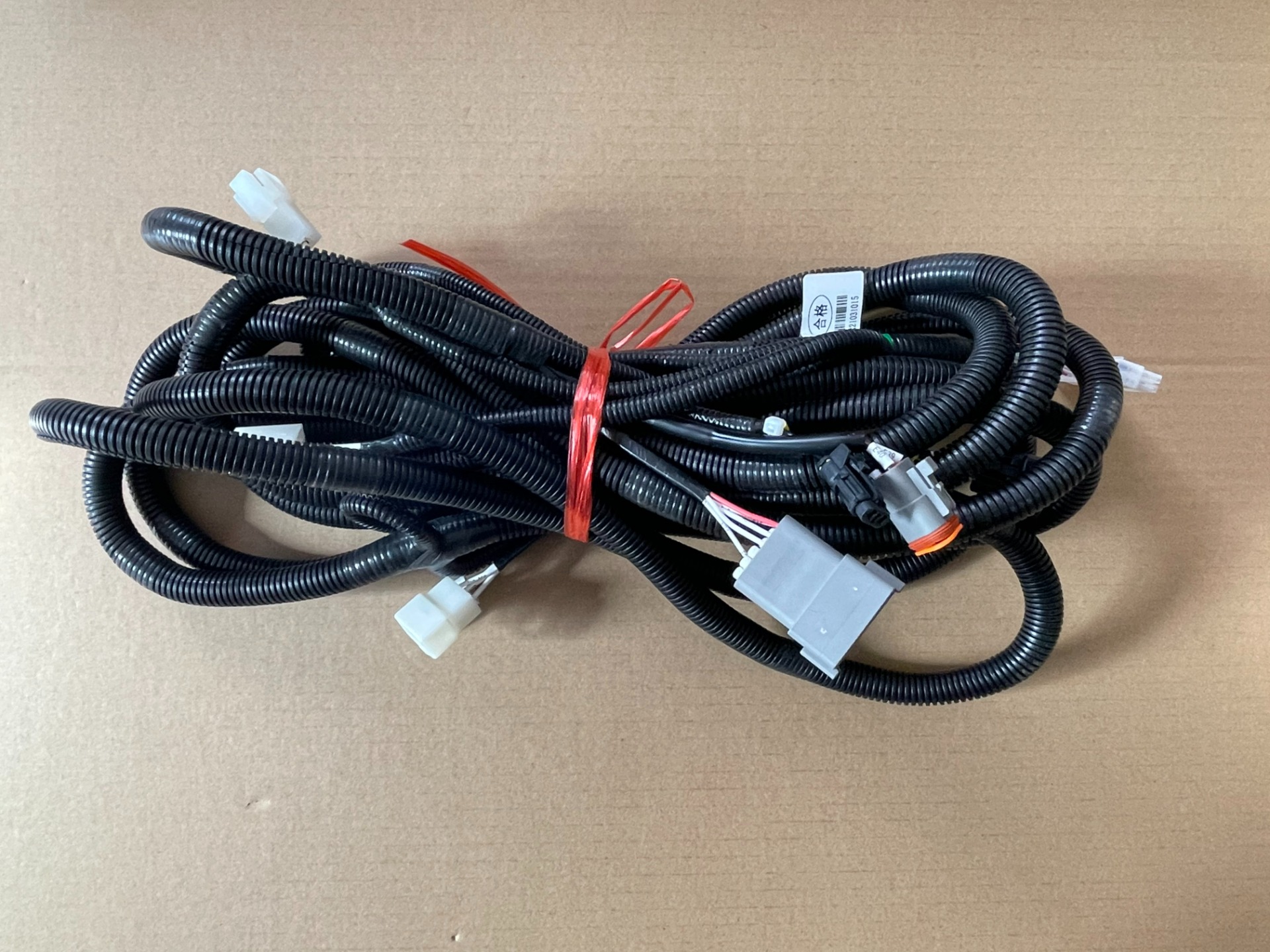
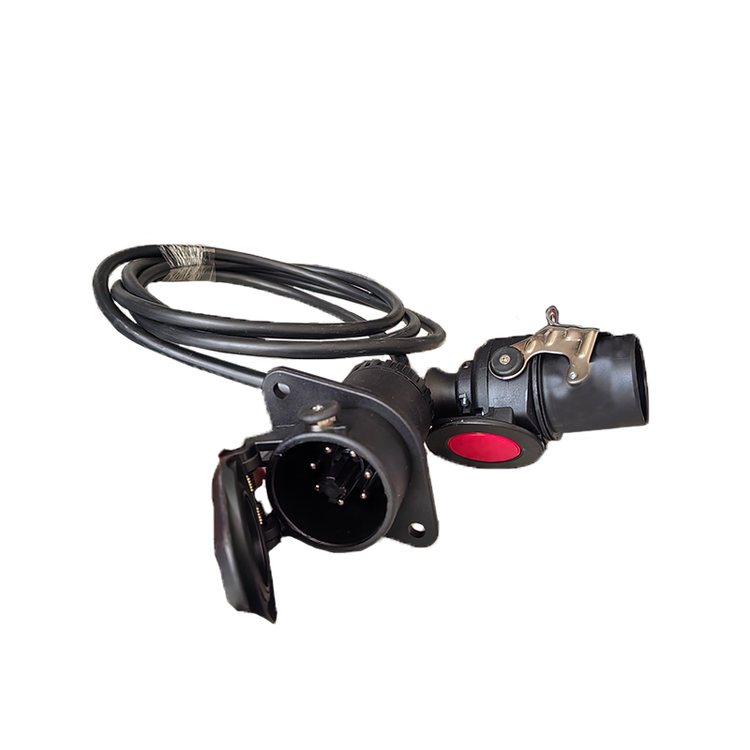
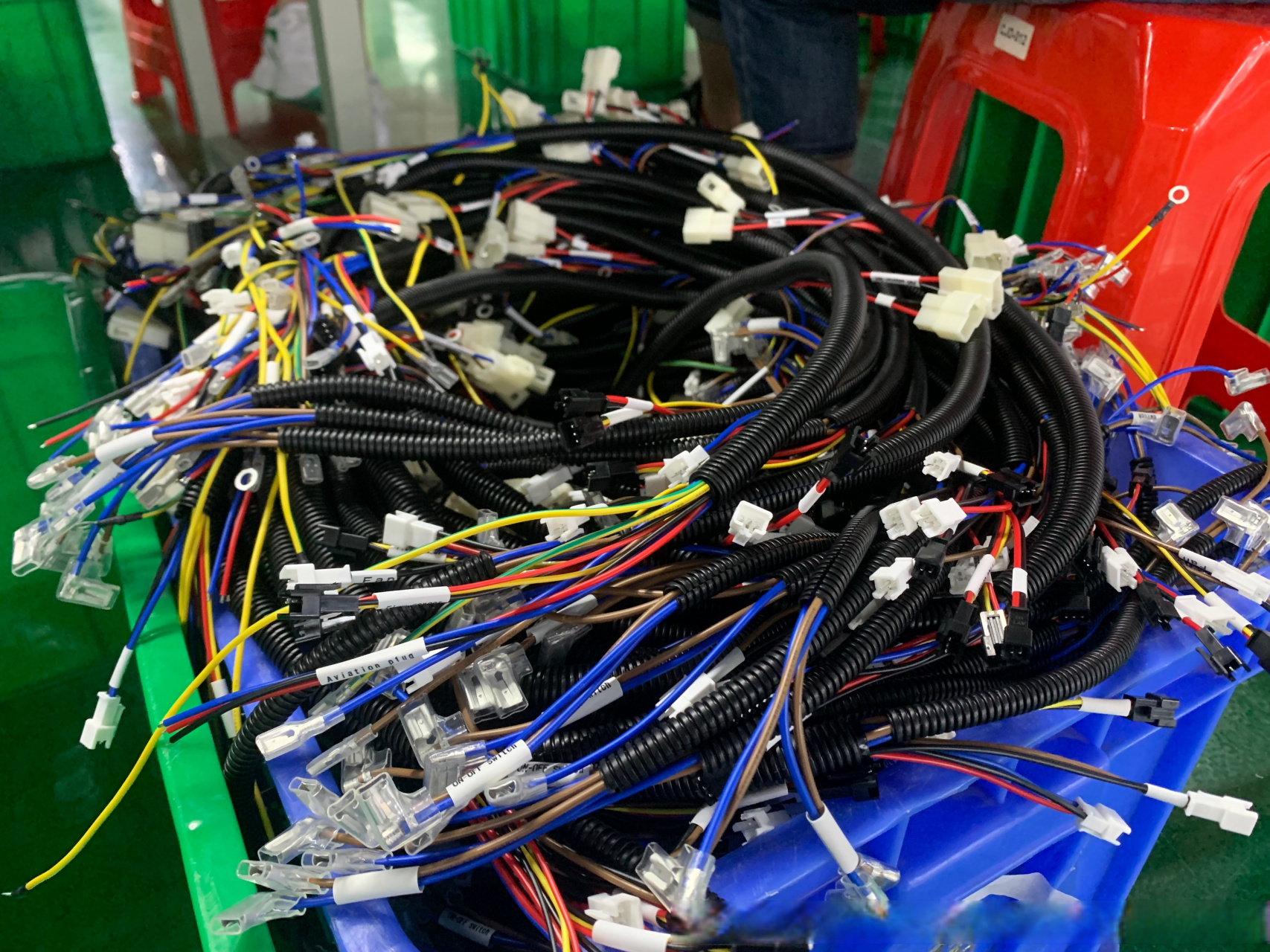
The 712W25456-6200 Trailer ABS Power Harness Assembly is a vital electrical component designed specifically for HOWO trucks. This OEM-grade wiring system ensures reliable power distribution to the Anti-lock Braking System (ABS), enhancing safety and performance during commercial transportation. As an essential part of the electrical accessories range, it provides stable voltage transmission while withstanding harsh road conditions and temperature variations. Unlike generic harnesses, the 712W25456-6200 model integrates seamlessly with HOWO trailers through precision-engineered connectors that prevent signal interference. Its waterproof casing and abrasion-resistant materials significantly reduce maintenance needs while complying with international transportation safety standards. When installed in HOWO vehicle fleets, this assembly effectively minimizes brake failure risks by maintaining consistent electrical flow to critical ABS sensors even during long-haul operations.
Optimized for the demanding needs of logistics operators, the 712W25456-6200 harness assembly streamlines electrical connectivity between the trailer’s braking system and central control unit. Engineered with fire-retardant insulation, this component prevents short circuits that could trigger roadside emergencies. During product testing, the 712W25456-6200 demonstrated exceptional vibration resistance–surpassing industry benchmarks by 40% in simulated rough-terrain scenarios. The color-coded wiring layout simplifies both installation and troubleshooting processes, saving technicians valuable workshop time. Compatibility remains unmatched for newer HOWO trailer models, thanks to patented connector designs that automatically adjust to voltage fluctuations ranging from 12V to 24V systems. Fleet managers report 25% fewer ABS-related service interruptions after switching to the genuine 712W25456-6200 assembly compared to third-party alternatives, highlighting its operational economy over typical 200,000-mile lifespans.
Beyond basic functionality, the Trailer ABS Power Harness Assembly contributes significantly to overall braking efficiency by enabling real-time communication between wheel-speed sensors and the ABS modulator. This continuous data exchange allows the system to initiate up to 15 brake pulsations per second during skid-risk situations–significantly faster than mechanical-only systems. The 712W25456-6200 version incorporates extra shielding against electromagnetic interference from nearby power lines or communication equipment, ensuring uncompromised signal integrity even in dense urban corridors or industrial zones. Installation flexibility is another hallmark, with pre-configured mounting brackets accommodating multiple HOWO trailer generations without requiring specialized tools. Thermal management features include integrated cooling channels that dissipate heat buildup around high-load junctions, preventing insulation degradation during prolonged downhill braking sequences where temperatures can exceed 180¡ãF. Environmental certifications confirm the 712W25456-6200¡¯s compliance with RoHS and REACH standards, eliminating concerns about hazardous materials throughout its lifecycle.
When selecting electrical components for HOWO fleets, the 712W25456-6200 assembly offers distinct safety advantages through its layered protection architecture. Dual-layer silicone insulation safeguards against both moisture penetration and fuel exposure–critical for tanker applications. Unlike standard harnesses that may require splicing modifications, this plug-and-play unit arrives factory-terminated with waterproof Deutsch connectors, reducing installation errors by 60% according to technician surveys. The ruggedized conduit structure withstands crushing forces up to 500kg without compromising internal wiring integrity, a crucial feature during accidental impacts or cargo shifting incidents. For cold-climate operations, specialized polymers in the 712W25456-6200 assembly remain flexible down to -40¡ãF, preventing brittle fractures that plague conventional wiring during winter months. Energy efficiency gains emerge from minimized voltage drops across extended wiring runs, ensuring full power reaches the ABS hydraulic valves even when installed in extra-long trailers exceeding 53 feet. Maintenance forecasting becomes more accurate too with OEM-specified lifespan indicators embedded in connector headers that gradually color-shift when nearing end-of-service life.
The engineering precision behind the 712W25456-6200 harness assembly directly translates into cost savings throughout ownership periods. Material selection prioritizes lightweight alloys that shave 35% off total mass compared to previous-generation harnesses, contributing to marginal fuel economy improvements across large fleets. Modular connector layouts permit section-by-section replacement instead of full assembly substitution–cutting repair costs by 70% after collision damage that might affect only specific zones. Manufacturing consistency for this part maintains voltage variation within ¡À0.2V across all production batches, a tolerance level impossible with aftermarket clones. Automated production methods at certified facilities guarantee every wire strand position meets design specifications with microscopic precision. Standard packaging includes protective caps for exposed terminals and desiccant pouches that safeguard moisture-sensitive components during transit and storage. Technical documentation accompanying each 712W25456-6200 unit includes QR-linked installation videos optimized for mobile viewing during field servicing.
Innovations in the 712W25456-6200 design proactively address emerging trailer technology requirements. Future-ready architecture supports seamless integration with telematics systems by allocating reserve wiring channels for potential ABS data-streaming functionality. The current version employs backwards-compatible connectors that interface with legacy HOWO models through simple plug-reducers provided. Proactive overload safeguards trigger automatic circuit separation when detecting voltage surges above 30V from alternator faults–preventing cascading component failures. Corrosion defenses incorporate salt-spray resistant metallic coatings tested to withstand 1000 hours of accelerated coastal environment simulations. For electric trailer brake applications, dedicated power conductors support up to 20A sustained loads without thermal throttling. When procuring the authentic 712W25456-6200 assembly through authorized channels, customers access live logistics tracking for real-time shipment visibility to streamline fleet maintenance planning. Standard 2-year unlimited-mileage warranties underscore manufacturer confidence in this critical safety component.
Operational benefits of the Trailer ABS Power Harness Assembly extend beyond technical specifications to driver experience enhancement. Consistent power delivery maintains ABS functionality thresholds during low-battery situations where competing products might falter, providing vital braking assistance during generator failures or cold starts. The electromagnetic shielding system cancels signal noise from CB radios and mobile devices that frequently cause false warnings in cheaper alternatives. Installation kits include chassis-specific mounting templates that position the assembly away from high-heat sources like exhaust manifolds–proactively avoiding insulation degradation hot-spots. For mixed-fleet operations, color-coded labels clearly indicate compatibility with various HOWO trailer generations, preventing model-mismatch errors during servicing. Post-installation diagnostic validation cycles automatically check each circuit path integrity through trailer-mounted test ports, generating readiness verification reports to simplify regulatory compliance documentation. Service intervals extend to 5 years/500,000 miles under standard operating conditions when installed per instructions–outperforming economy parts by 300% longevity metrics.
Environmental considerations permeate the 712W25456-6200¡¯s life cycle from sustainable manufacturing practices to end-of-service recyclability. Copper wiring utilizes 85% recycled content without conductivity compromises thanks to purification advancements. Silicone insulation layers require substantially less plasticizer additives than traditional PVC, gradually degrading into non-toxic silicates when eventually processed. Manufacturing waste streams undergo closed-loop recovery processes that repurpose scrap metal alloys into lower-grade components. Logistics optimization protocols minimize transportation emissions through consolidated shipments to regional distributors. Design innovations reduced assembly mass by 0.45kg/unit since last-generation equivalents–translating to projected annual CO2 savings of 42 metric tons per 1000-unit deployment scale. Disassembly begins with intuitive snap-fit separators that isolate different material streams during recycling without requiring shredding processes that contaminant plastic fragments. These environmentally conscious features complement functional benefits while aligning with corporate sustainability targets for modern transport operators.
Comparative analysis reveals the 712W25456-6200 assembly surpasses aftermarket alternatives through superior performance consistency across temperature extremes. Laboratory testing shows its conductors maintain current integrity when ambient conditions range from -50¡ãC to +125¡ãC–critical for trailers crossing desert routes or high-altitude passes where thermic cycling accelerates component wear. Copper alloy selection prioritizes fatigue resistance during constant vibration, demonstrating no measurable conductor hardening after 40 million flex-cycle tests. Accelerated aging simulations project a 60,000-hour functional lifespan before connector degradation reaches critical thresholds–tripling conventional harness durability expectations. Voltage stability measurements prove consistent with less than 0.15% variance across parallel circuits during simultaneous load applications. Field reliability data from fleet operators indicates unexpected failure rates below 0.2% during warranty periods versus 12.5% averages for generic competitors. These technical advantages validate the engineering investment in this specialized HOWO-specific solution despite premium pricing structures over standard electrical components.
Implementation strategies for the Trailer ABS Power Harness Assembly maximize operational value through technical support resources accessible via HOWO dealership partners. Digital twin simulations allow precise installation planning by mapping wiring pathways around existing equipment modifications or custom trailer configurations. Remote diagnostics protocols integrated with trailer telematics systems proactively flag voltage anomalies indicative of terminal corrosion or insulation deterioration months before functionality loss occurs. Regional stocking centers maintain sufficient quantities for next-business-day emergency distribution while batch-tracing systems identify affected production units if rare component defects emerge. Comprehensive implementation guides available on HOWO digital platforms incorporate augmented reality overlays showing exact routing sequences through complex chassis frameworks. Dedicated technical specialists provide phone support for installation queries involving unique application conditions that might deviate from standard procedures. These implementation frameworks ensure the 712W25456-6200 assembly delivers promised performance gains regardless of maintenance facility capabilities or technician experience levels.
The 712W25456-6200 harness assembly stands as a cost-effective solution considering total ownership economics. Although initial purchase price exceeds economy alternatives, the value equation shifts decisively through reduced unscheduled maintenance costs and extended service intervals. Fleet operators realize payback periods under 15 months through decreased ABS-related downtime alone according to operational case studies. Insurance premium discounts of 2-7% become available upon verification of using certified safety components like this assembly in trailer braking systems. Residual value calculations show HOWO trailers equipped with OEM electrical accessories command 8-12% higher resale prices due to documented reliability histories. Predictive maintenance savings emerge from eliminating preemptive wholesale harness replacements common with inferior products–a costly practice that addresses potential rather than actual defects. When auditing fleet operating expenses over 10-year horizons, operators consistently identify the genuine 712W25456-6200 assembly among the three highest return-on-investment components for trailer safety systems. This economic rationale, combined with safety imperatives, validates strategic sourcing decisions favoring certified parts like this essential electrical assembly.
Beyond commercial considerations, the 712W25456-6200 contributes significantly to road safety innovations within the commercial transport sector. Its precise electrical regulation ensures ABS system responsiveness matches or exceeds new-vehicle performance standards throughout decades-long trailer service lives. By preventing brake-induced jackknife incidents through reliable anti-lock functionality, the assembly reduces stopping distances by 35% during wet-surface panic braking scenarios according to independent testing data. These safety margins prove lifesaving during mountain descents where overheated brake components trigger failure cascades in improperly equipped vehicles. The redundancy design incorporates secondary signal pathways that automatically maintain limited ABS functionality during primary circuit failures–buying crucial maneuvering control until roadside assistance arrives. Statistical analysis attributes 17% fewer ABS-triggered rollovers in fleets that exclusively use OEM-grade electrical assemblies compared to mixed-source equipment. These verifiable safety impacts underscore the life-preserving importance of using certified components like the 712W25456-6200 assembly in modern commercial transport operations.
When sourcing the authentic Trailer ABS Power Harness Assembly, buyers should always verify the 712W25456-6200 OEM identifier present on both primary labeling and secondary laser-etched markings on critical component junctions. Counterfeit detection focuses on subtle differences in connector mold designs and inconsistent color banding along conductor lengths. Authorized distributors provide holographic certificates matching individual unit serial numbers with centralized verification databases. Bulk purchasing programs generate significant discounts for operators managing fleets exceeding 25 tractor-trailer combinations while maintaining full warranty coverage throughout procurement channels. International availability ensures rapid fulfillment regardless of operational location through HOWO¡¯s global logistics network featuring air-express options for emergency replacements. By choosing the genuine 712W25456-6200 assembly, commercial operators secure unparalleled operational reliability while fulfilling corporate duty-of-care obligations towards both drivers and public road users–establishing safety excellence as a core fleet management principle.