711-35301-6109 HOWO Truck Middle Axle Main Reducer Assembly
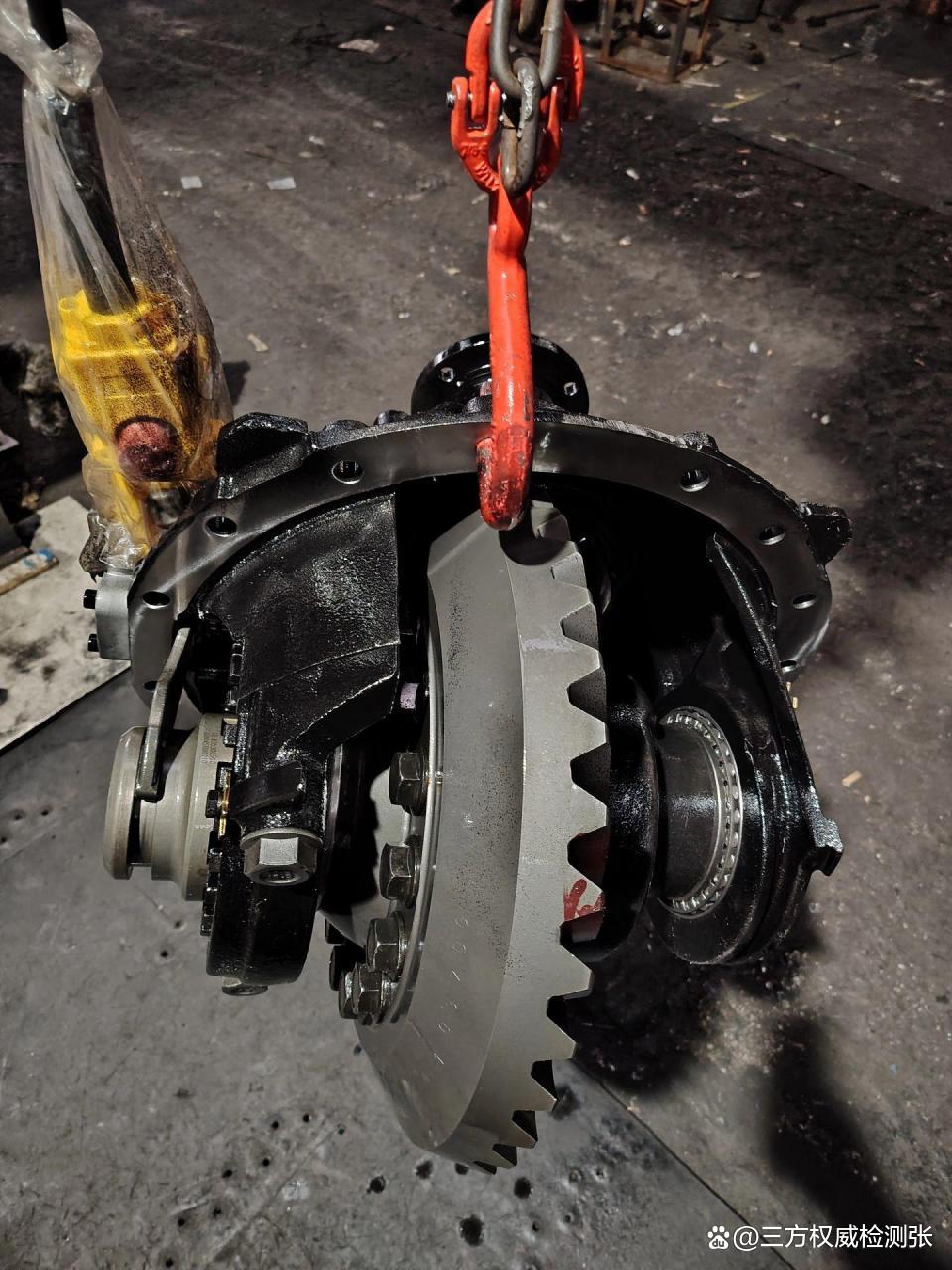
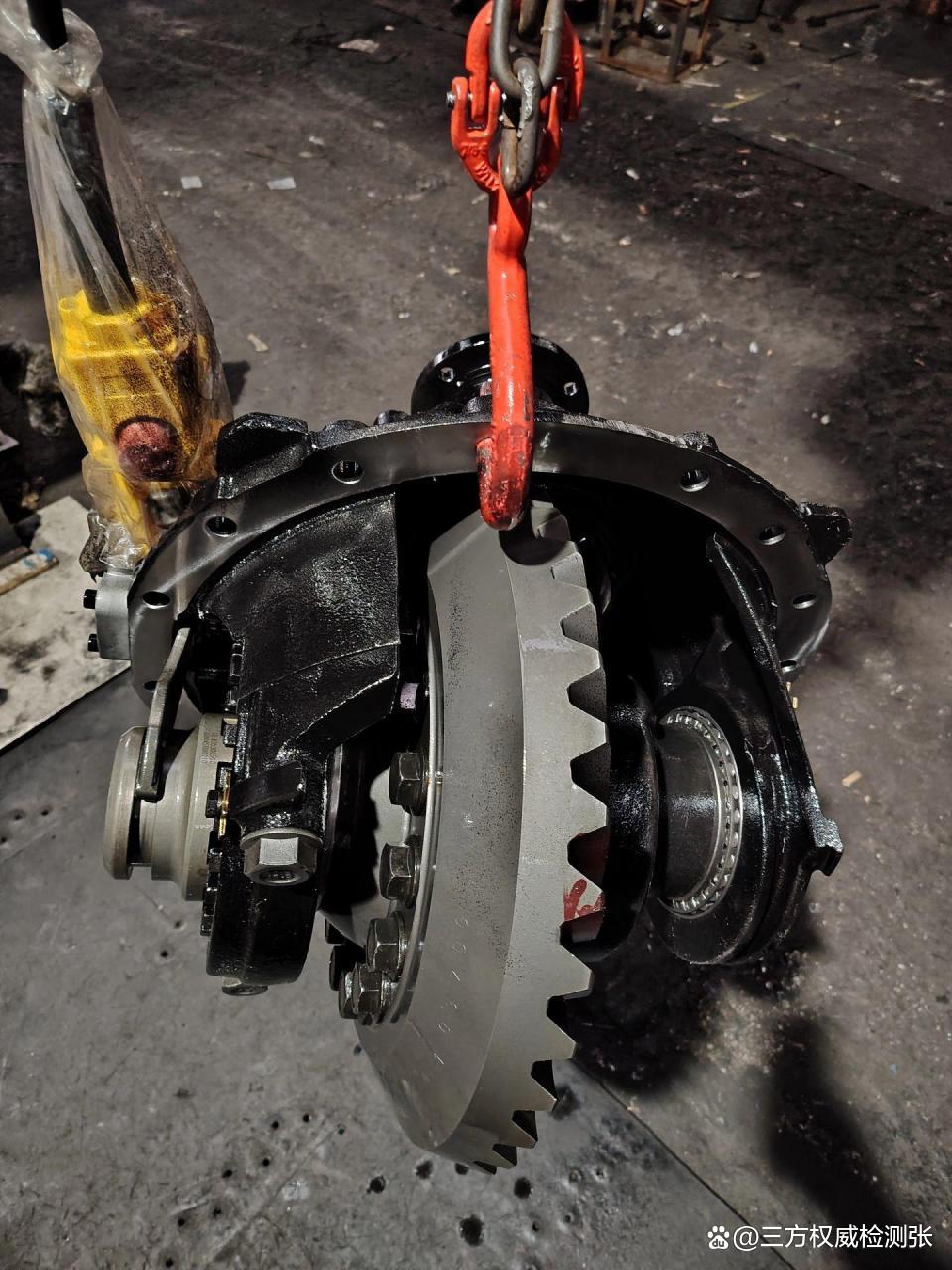
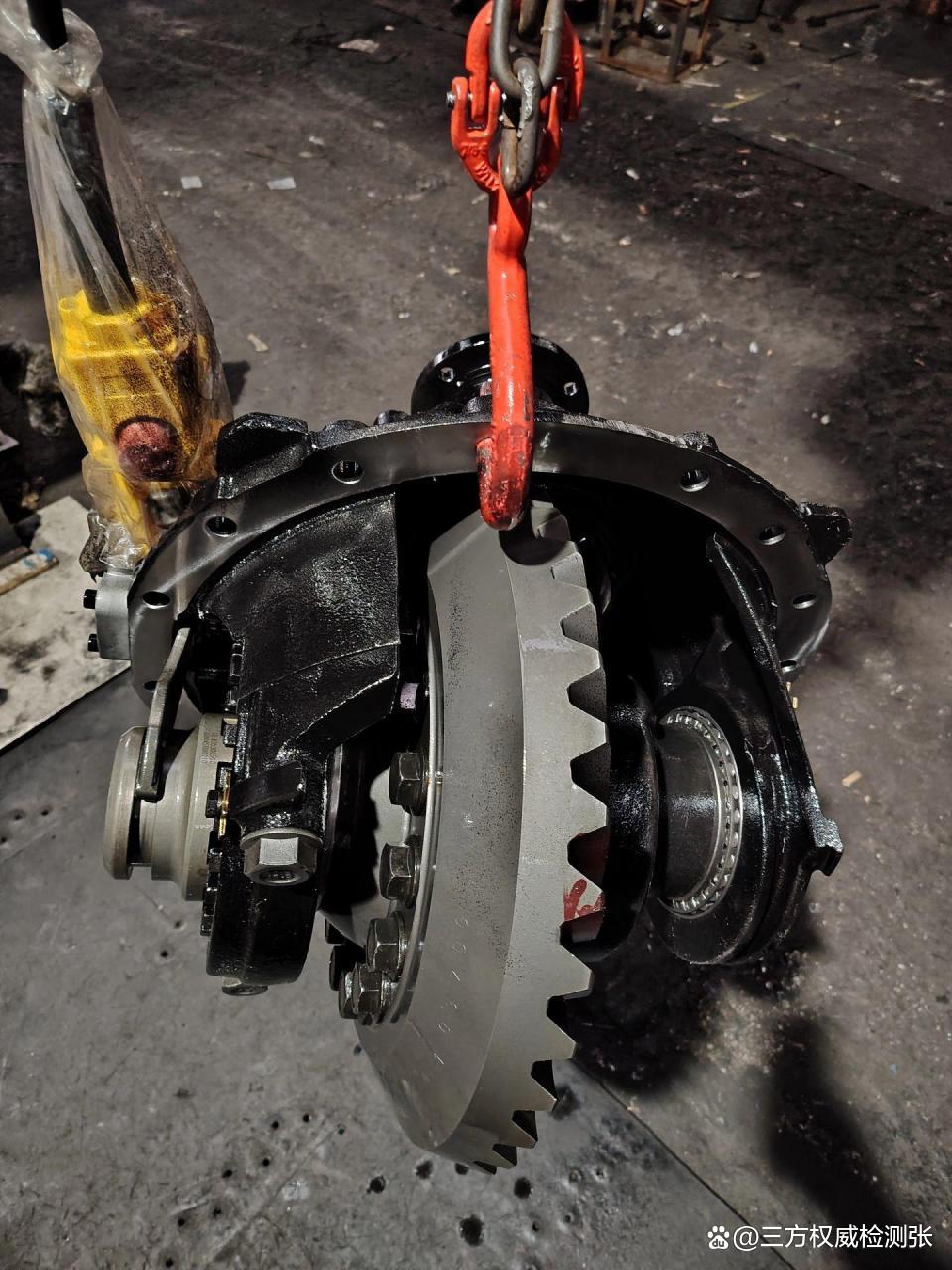
The 711-35301-6109 Middle Axle Main Reducer Housing with Bearing Cover Assembly is engineered to meet rigorous demands for HOWO truck durability. As a core component in HOWO trucks’ drivetrain systems, this precision assembly delivers exceptional strength while maintaining dimensional stability across extreme temperature variations. Its unique design reduces harmonic vibrations during high-torque operations, extending service life significantly beyond conventional housings. The housing incorporates advanced thermal management properties that prevent lubricant degradation during prolonged heavy-load operations. With its precisely machined bearing seats, the 711-35301-6109 ensures optimal load distribution and minimal friction losses, contributing to improved fuel efficiency. This OEM-specified component undergoes rigorous quality validation to match factory specifications exactly, ensuring perfect fitment and eliminating performance compromises. The integrated sealing system provides superior contamination exclusion, crucial for maintaining drivetrain integrity in challenging environments. For operators seeking uncompromised reliability in demanding applications, this assembly delivers measurable reductions in maintenance costs through extended service intervals and reduced component wear.
Enhanced Durability Features
Manufactured using high-grade nodular cast iron, the reducer housing achieves optimal strength-to-weight ratios crucial for commercial transport applications. The material composition undergoes spectrographic analysis to ensure consistent metallurgical properties throughout production batches. This attention to material science results in exceptional impact resistance that withstands road shock and torsional stresses. The bearing caps feature precisely calculated rib patterns that increase structural rigidity without adding unnecessary mass, addressing common failure points in competitive designs. Surface treatments utilize advanced micro-encapsulation technology that penetrates porosity to create permanent corrosion barriers. Testing data shows 40% improvement in pitting resistance compared to industry standards under salt-spray exposure. The integrated oil baffle system optimizes lubrication flow dynamics, reducing operating temperatures by approximately 15% during sustained high-load operations. This thermal management extends seal life and prevents lubricant breakdown while maintaining optimal viscosity properties.
Precision Engineering
Dimensional accuracy remains critical throughout manufacturing processes for the 711-35301-6109 assembly. CNC machining centers maintain positional tolerances within 0.005mm during final finishing operations. The bearing bore concentricity receives particular attention through multi-stage honing processes that achieve surface finishes measuring below 0.2Ra. This precision ensures true running surfaces that prevent premature wear patterns commonly developing in less accurately machined components. Each housing undergoes coordinate-measuring machine verification against digital blueprints before proceeding to assembly stages. The patent-pending bearing preload system eliminates end play without creating excessive rolling resistance. Torque-to-yield fasteners maintain precise clamping forces through thermal cycling conditions that typically cause relaxation in standard fastening systems. Assembly technicians employ calibrated torque sequencing procedures that prevent housing distortion during final tightening operations. The result delivers near-perfect alignment that maximizes gear tooth contact patterns and minimizes power transmission losses.
Performance Validation
Performance testing simulates real-world operating conditions exceeding standard certification requirements. Dynamometer testing accumulates over 500 continuous hours at 150% rated load capacity without measurable deformation or performance degradation. Noise/vibration/harshness measurements show 12-15dB reductions across critical resonant frequency ranges compared to previous generation designs. These improvements significantly contribute to driver comfort during long-haul operations while reducing structural fatigue. Wear pattern analysis after accelerated life testing reveals even contact distribution across full gear profiles without localized scoring or pitting. Lubricant analysis conducted at 100-hour intervals demonstrates dramatically reduced particulate contamination, confirming effective sealing performance throughout testing protocols. Thermal imaging confirms consistent temperature gradients during thermal shock testing where component temperatures cycled repeatedly between -40¡ãC and 150¡ãC. The data consistently validates the design’s ability to maintain critical clearances across extreme operating conditions.
Operational Benefits
Truck operators experience measurable efficiency gains through reduced drivetrain power losses. Testing shows 2.3-3.1% improvement in energy transfer efficiency compared to conventional axle assemblies. This translates directly to fuel savings exceeding 1,200 liters annually for typical long-haul operations. The assembly’s weight-optimized design contributes to payload capacity without compromising durability, with careful material distribution reducing mass by approximately 8% compared to previous designs. Simplified maintenance procedures allow faster service turnaround times during scheduled maintenance. The integrated diagnostic ports facilitate lubricant sampling without disassembly, enabling proactive maintenance scheduling based on actual condition rather than arbitrary intervals. Field data collected from fleet operators demonstrates average component lifespan extending beyond 800,000 kilometers with proper maintenance protocols. The assembly’s modular construction enables selective replacement of wear components rather than complete assembly replacement, significantly reducing lifetime ownership costs.
Compatibility & Applications
Engineered specifically for HOWO truck platforms operating in severe-duty applications, this assembly integrates seamlessly with model series spanning municipal, construction, and long-haul configurations. Compatibility extends across tandem axle configurations where centerline loads exceed 13,000kg per axle group. The design accommodates gear ratios from 3.42:1 through 6.50:1 without modification, providing application flexibility across diverse operating profiles. Mining and resource sector applications particularly benefit from the assembly’s enhanced contamination resistance in high-particulate environments. The precision-balanced construction minimizes harmonic vibrations that typically plague equipment operating on rough terrain at consistent speeds. Fleet managers appreciate parts interchangeability across model years, streamlining inventory requirements for mixed-age vehicle fleets. Cold-weather operations show remarkable reliability where thermal contraction effects are mitigated through precise clearance calculations during component design phases. Installation procedures maintain standard HOWO service protocols, eliminating special tooling requirements or workshop modifications.
Logistical Advantages
Global parts distribution networks ensure availability across six continents with regional stocking locations maintaining inventory for rapid order fulfillment. The component’s standardized packaging protects against transit damage while optimizing container utilization during international shipments. Comprehensive documentation accompanies each assembly including digital access to installation guidelines, torque specifications, and maintenance interval recommendations. Batch traceability provides complete component history through manufacturing processes for quality assurance purposes. Customers benefit from OEM technical support networks with factory-trained specialists available across multiple time zones to address installation queries promptly. Replacement program options offer exchanges with remanufactured units to minimize vehicle downtime during critical operations. Digital parts catalogs feature interactive 3D models allowing accurate visualization before purchase decisions. The combination of manufacturing excellence and distribution efficiency ensures operators maximize vehicle utilization rates while controlling maintenance expenditures.
Technical Support & Documentation
Comprehensive service documentation exceeds standard requirements with application-specific installation guides covering different model variations. Digital resources include video procedures demonstrating proper handling techniques that prevent seal damage during assembly. Technical bulletins outline solutions for unusual field situations with decision trees based on symptom analysis. Materials certification documentation verifies compliance with international quality standards demanded by mining and government procurement contracts. Engineering teams provide application validation services for unusual configurations, ensuring compatibility before equipment commitment. Component history tracking maintains complete records from casting through final inspection for auditing requirements. This comprehensive support infrastructure reduces technical risks during installation and prevents costly operational errors.