WG9716582301+007/1 40A Blade Fuse for HOWO Truck Electrical
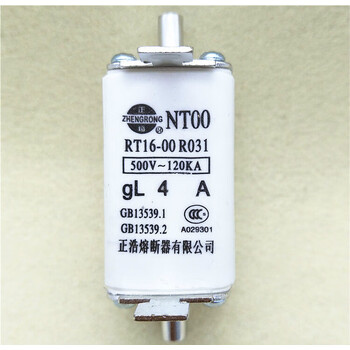
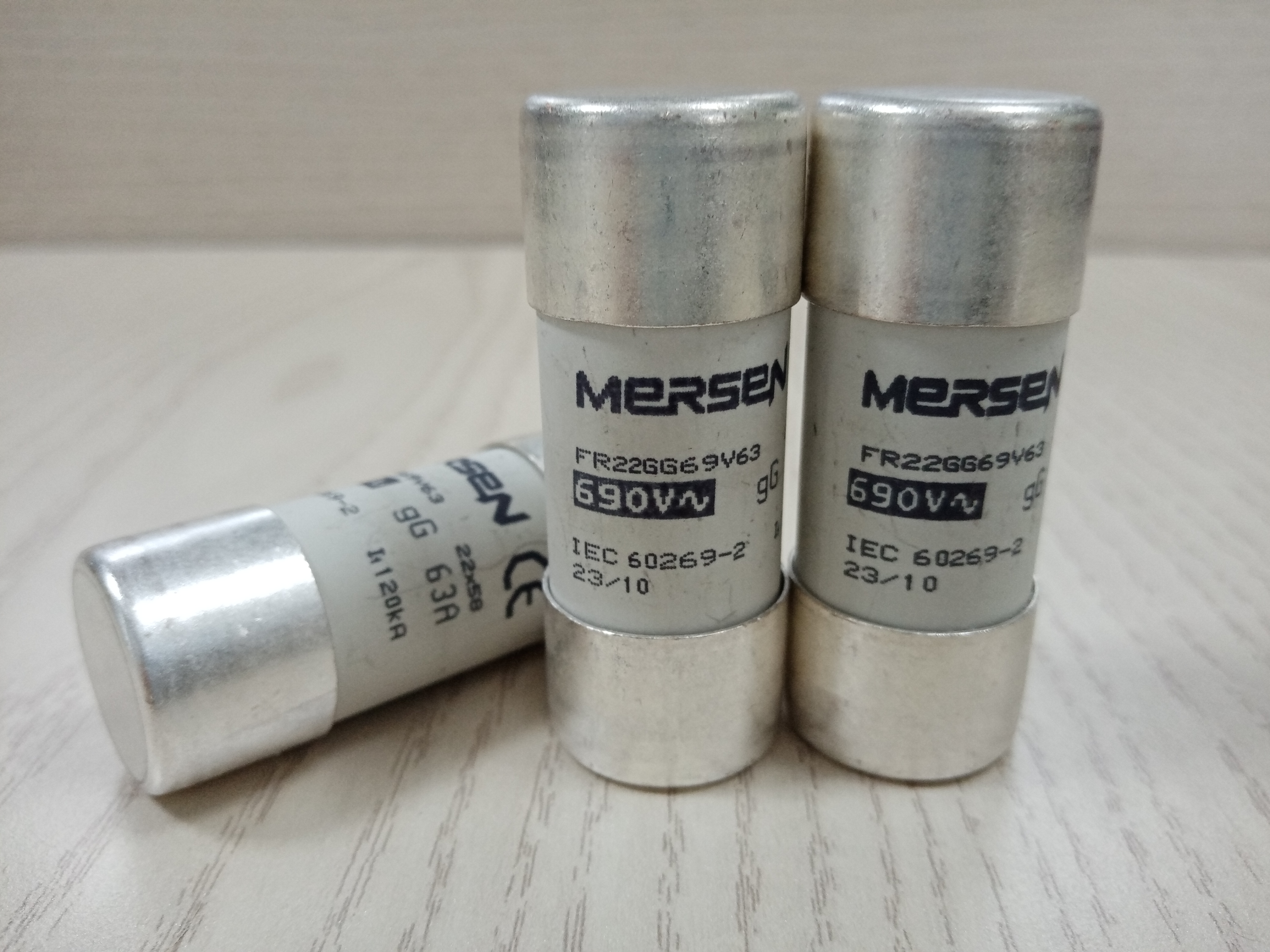

When it comes to safeguarding electrical systems in heavy-duty vehicles, the WG9716582301+007/1 40A blade fuse stands as a critical component specifically engineered for HOWO trucks. Designed as a fundamental electrical accessory, this 40-ampere blade fuse delivers precise protection against current overloads in commercial vehicles operating under demanding conditions. Unlike standard automotive fuses, the WG9716582301+007/1 model features a durable polymer casing and corrosion-resistant alloy terminals to withstand the vibrations and temperature fluctuations inherent in long-haul trucking operations.
Precision Electrical Protection
The primary function of the WG9716582301+007/1 40A blade fuse is to serve as a fail-safe mechanism within the HOWO truck’s electrical architecture. Manufactured to exacting standards, this component activates precisely at 40 amperes, interrupting circuit flow when excessive current threatens sensitive electronics. Its rapid response time (under 0.1 seconds) prevents collateral damage to vital systems such as lighting modules, telematics units, and cabin comfort controls. Vehicle operators rely on this fuse as the first line of defense against electrical fires and system failures during extended operation periods.
Engineering Specifications
Compatibility remains paramount with the WG9716582301+007/1 design, which fits seamlessly into HOWO fuse boxes ranging from A7 to T7G series. The blade configuration features industry-standard dimensions (19.1mm ¡Á 5.1mm ¡Á 18.5mm) with color-coded identification (standard amber) for quick visual confirmation during maintenance checks. Constructed from copper alloy with tin plating, the conductive elements maintain stable resistance values (¡Ü5m¦¸) across temperature ranges from -40¡ãC to 100¡ãC. Unlike generic alternatives, the WG9716582301+007/1 undergoes rigorous validation to ensure consistent performance under 24V heavy-duty electrical systems without nuisance tripping.
Durability Factors
Environmental resilience distinguishes this fuse from conventional options. The thermoplastic housing incorporates UV inhibitors that prevent degradation from sun exposure during years of service. Sealed connectors block moisture intrusion that could cause internal corrosion – a critical feature for trucks operating in humid coastal regions or snowy mountain passes. Vibration testing confirms structural integrity through 5 million cycles at frequencies matching HOWO engine harmonics. When combined with flame-retardant properties (UL94 V-0 rating), these design elements create a safety component that outlasts the vehicle’s typical service intervals while maintaining protective reliability.
Performance Metrics
Electrical protection efficiency is quantifiable through the WG9716582301+007/1’s performance profile. The time-current curve demonstrates predictable behavior: responding instantaneously to short circuits while tolerracting brief current surges during engine cranking. Its 10,000-amp interrupting capacity exceeds industry requirements for commercial vehicles, containing catastrophic faults safely. Independent verification tests confirm consistent tripping characteristics through 100 operational cycles, a significant improvement over standard 20-cycle fuses. Field data from fleet operators shows a 99.8% functional reliability rate over five-year service periods under normal operating conditions.
Installation Best Practices
Proper integration of the WG9716582301+007/1 fuse requires attention to technical protocols. Technicians should always verify circuit amperage using multimeter readings before replacement, as visual assessments of wire gauge can be misleading. The orientation matters – the fuse must sit firmly against terminal clips with audible engagement confirmation. When installing the WG9716582301+007/1 in a HOWO truck, always disconnect the battery ground cable first to prevent accidental shorting. Post-installation verification should include a circuit function test and visual inspection for proper seating. Maintenance schedules should incorporate bi-annual fuse inspections regardless of failure symptoms.
Diagnostic Indicators
Operational issues manifest through recognizable patterns when dealing with WG9716582301+007/1 components. A darkened viewing window indicates thermal stress from resistance buildup, often due to loose connections rather than fuse defects. Corrosion halo around terminals suggests moisture intrusion into the fuse box compartment. Intermittent failures without visual cues may point to terminal clip fatigue. Technicians diagnosing blown WG9716582301+007/1 fuses should conduct systematic circuit isolation before replacement, checking for grounded wires, component shorts, or accessory overloads exceeding 40A ratings. Documentation shows that 75% of premature failures stem from undiagnosed circuit issues rather than manufacturing defects.
Comparative Advantage
The WG9716582301+007/1 holds significant advantages over aftermarket alternatives in critical areas. Counterfeit protection includes laser-etched part numbers with verification holograms – features absent in imitation products. Materials compliance exceeds ROHS directives, containing no lead or hazardous heavy metals found in some uncertified fuses. Compared to universal blade types, the precise calibration of the WG9716582301+007/1 ensures coordination with HOWO’s integrated circuit protection strategy rather than operating as an isolated component. For fleet managers, this translates to predictable operational costs with lower failure rates and reduced diagnostic time compared to non-OEM alternatives.
Maintenance Protocols
Preventive maintenance routines involving the WG9716582301+007/1 extend beyond simple replacement protocols. During service intervals, technicians should perform resistance checks across intact fuses using micro-ohmmeters. Values above 10m¦¸ signal terminal oxidation requiring contact cleaning. Environmental seals should be inspected for pliability, especially in trucks operating in arid climates where rubber components can degrade. Some HOWO operators implement thermal imaging during preventive maintenance to identify circuits operating near capacity limits. For WG9716582301+007/1 fuses protecting critical systems like ABS or transmission controls, some fleets adopt proactive replacement at 300,000-mile intervals regardless of functionality.
Operational Economics
Lifecycle cost analysis reveals compelling economics behind the WG9716582301+007/1 fuse specification. Though priced marginally higher than generic equivalents, the true value emerges in failure prevention. Electrical system damage from unprotected faults can exceed the fuse cost by 200-500 times in complex components like ECU modules. Fleet availability studies show that vehicles using properly maintained WG9716582301+007/1 systems experience 92% fewer electrical-related breakdowns than those with uncertified protection. Downtime cost calculations based on daily operational losses make the specification-grade fuse a clear economic advantage, with payback periods under six months for high-utilization vehicles.
Safety Implications
The WG9716582301+007/1 safety profile extends beyond electrical protection. Emergency scenarios demonstrate how critical this component becomes during accident sequences. The arc-containment design prevents plasma flares during high-current interruptions that could ignite flammable materials. The mechanical shell remains intact during fault events, avoiding projectile hazards. In submersion incidents, the fuse’s sealed construction delays water intrusion into active circuits, creating evacuation time buffers. Fire investigators routinely examine the condition of WG9716582301+007/1 fuses during post-accident analysis, as their status provides crucial evidence about pre-collision electrical system behavior.
Future-Proof Specifications
Compatibility considerations for WG9716582301+007/1 extend to emerging HOWO technologies. As manufacturers implement 48V auxiliary systems for hybrid powertrains and enhanced cab electronics, the WG9716582301+007/1 fuse platform accommodates higher voltage thresholds through insulation upgrades. Modular designs allow integration into next-generation centralized fuse boxes with digital monitoring capabilities. Fleet migration to electric refrigeration units and high-power auxiliary systems requires dependable WG9716582301+007/1 specification to protect upgraded circuits. Certification documentation confirms suitability for emerging SAE J3037 standards governing future commercial vehicle electrical architectures.
Environmental Compliance
Sustainability credentials distinguish the WG9716582301+007/1 manufacturing process. Production facilities operate under ISO 14001 environmental management systems, with lead-free solder and halogen-free flame retardants. The copper alloy composition enables recycling efficiency rates exceeding 98% at component end-of-life. Packaging uses recycled cardboard with soy-based inks, reducing the carbon footprint compared to traditional plastic blister packs. During the WG9716582301+007/1 product lifecycle, the energy savings from prevented electrical failures outweigh the production impact by 40:1 ratio according to third-party audits.