752-25453-6606 Wiper Motor Wire Harness for HOWO Truck
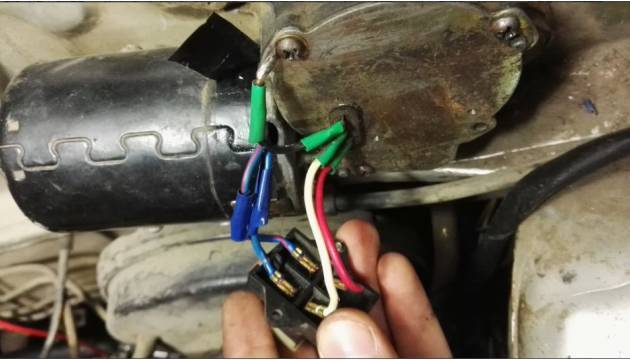
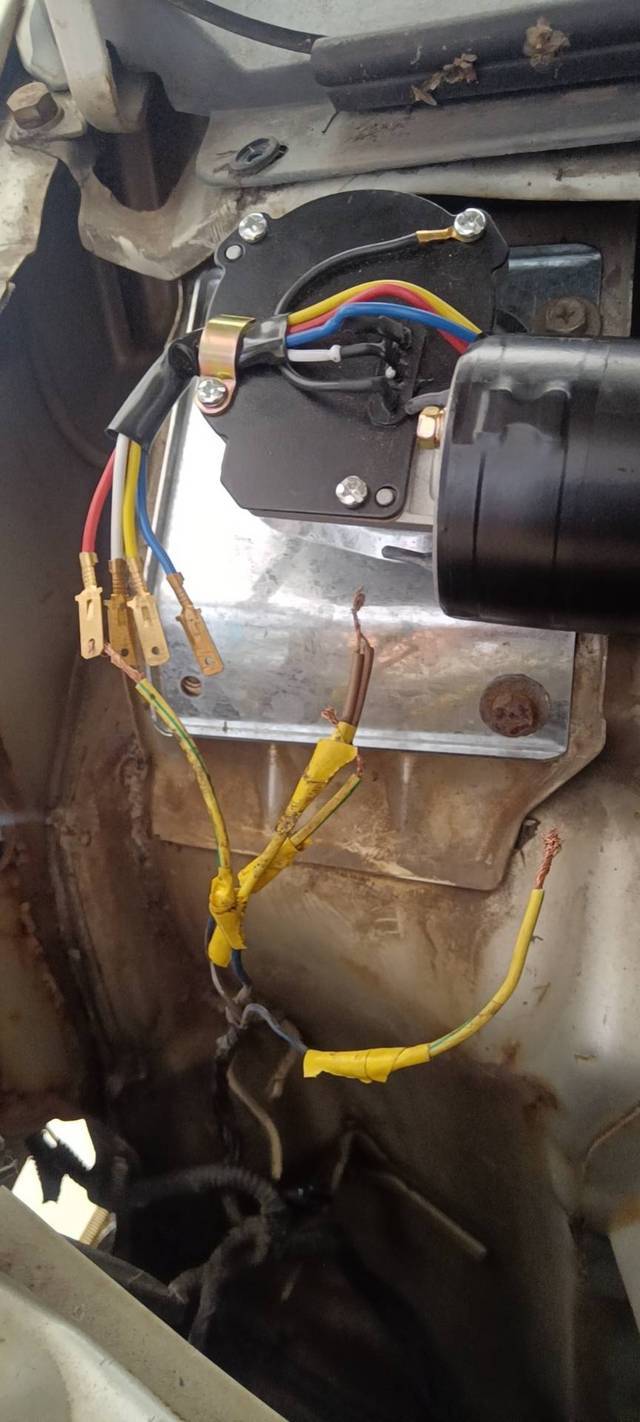
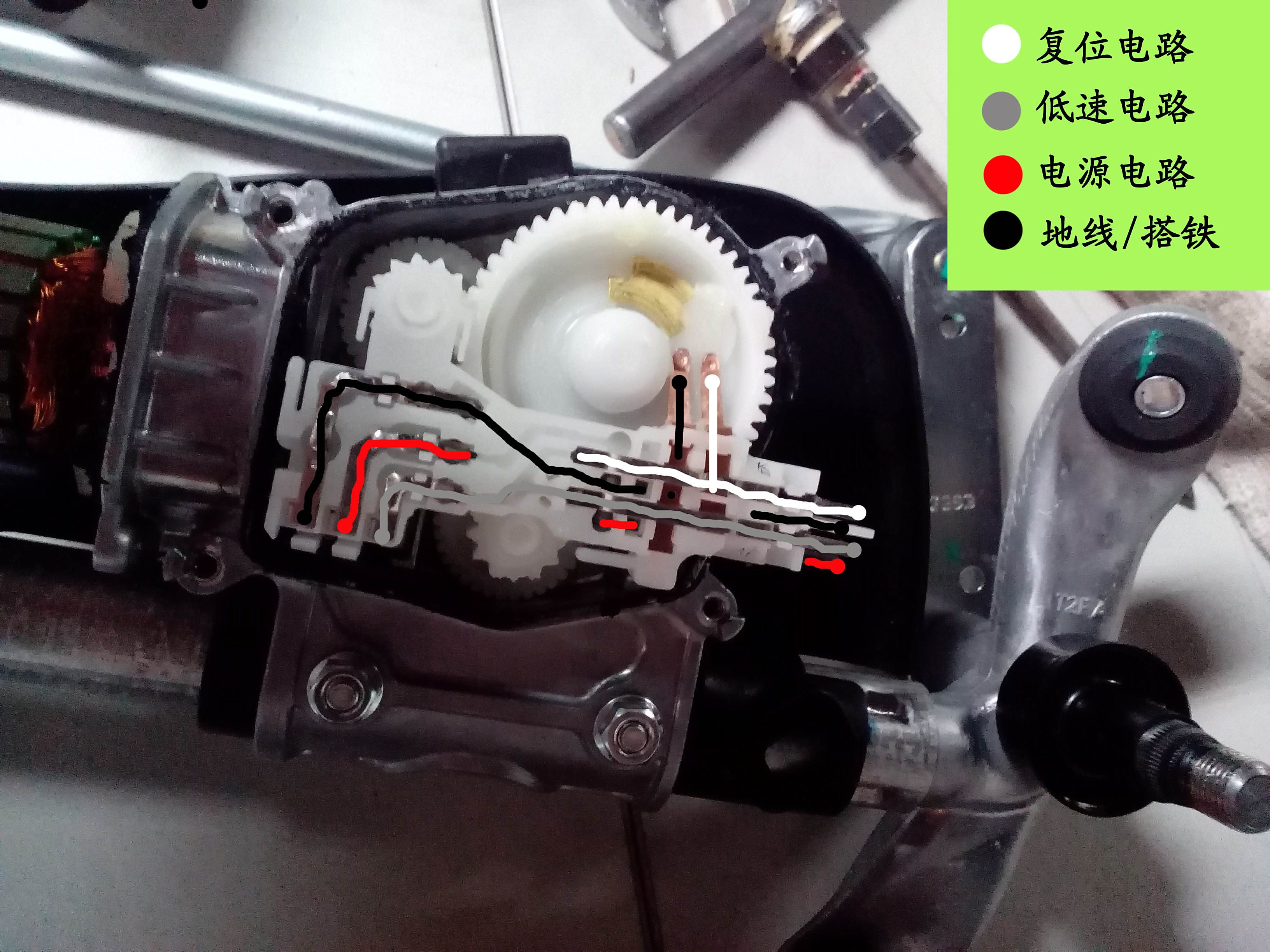
The 752-25453-6606 wiper motor wire harness is an essential electrical component specifically engineered for HOWO trucks. This precision-crafted connectivity solution ensures optimal performance of your windshield wiper system in all weather conditions. Designed to withstand the rigorous demands of commercial trucking operations, this OEM-compatible harness features industrial-grade connectors that provide secure electrical transmission between the wiper motor and vehicle control system. When heavy rain or snow threatens visibility, the reliability of your wiper system directly impacts driving safety. That’s why the 752-25453-6606 harness uses vibration-resistant terminals and abrasion-proof insulation to maintain consistent electrical flow even on rough terrain.
Compatibility with HOWO truck models sets this wire harness apart from generic alternatives. Each 752-25453-6606 unit undergoes strict validation to ensure perfect connector alignment and circuit configuration for seamless integration with HOWO electrical systems. The waterproof casing protects sensitive wiring connections from moisture intrusion that can cause corrosion-induced failures. This becomes critical when operating in wet climates where frequent wiper usage tests electrical endurance.
Enhanced Durability Features
The OEM 752-25453-6606 harness incorporates temperature-resistant materials rated for -40¡ãF to 230¡ãF operational extremes. This thermal stability prevents wire insulation degradation during summer heat waves or winter freeze-thaw cycles. Unlike aftermarket replacements using PVC coatings, this HOWO-specific harness features cross-linked polyethylene insulation that resists cracking and chemical exposure from road treatments. The precise gauge wiring reduces voltage drop across the circuit, ensuring your wiper motors receive stable power for consistent operation.
For fleet managers maintaining HOWO truck operations, the 752-25453-6606 wiring harness significantly reduces electrical failure incidents. Every connection point is reinforced with strain-relief boots that prevent wire-pull separation from engine vibration. The connectors utilize tin-plated brass contacts that maintain conductivity superior to standard copper alternatives. When replacing worn wiring, this harness installs in minutes using factory-matching connectors that snap securely into position without wiring modifications. This plug-and-play design minimizes installation downtime, critical for commercial transport operations.
Performance Engineering
In demanding HOWO truck applications, consistent wiper operation isn’t optional. The 752-25453-6606 harness delivers uninterrupted current through corrosion-resistant pathways that outlast bare wiring solutions. Each wire strand is precisely aligned in its terminal housing using automated optical inspection, eliminating connection faults at the microscopic level. This precision manufacturing is why the 752-25453-6606 harness remains the preferred choice for HOWO service centers.
Optimal functionality of windshield wiper systems depends significantly on reliable electrical transmission. The 752-25453-6606 harness solves common electrical faults that cause wiper motor malfunctions. Its innovative double-wall shrink tubing safeguards against moisture infiltration at critical junction points. The wire connectors employ a positive-locking design with audible engagement confirmation to prevent vibration-induced disconnections. For HOWO drivers navigating torrential downpours, this reliability can become a lifesaving feature.
Electrical resistance remains minimal throughout the 752-25453-6606 harness due to optimal copper core purity and terminal surface conductivity. This design prevents excessive voltage drops that reduce wiper motor torque, maintaining consistent blade pressure on windshield surfaces. Reduced electrical resistance also decreases energy demands on truck electrical systems. During winter storms, when multiple electrical accessories operate simultaneously, the efficiency of the 752-25453-6606 harness ensures wiper motors receive priority power.
Installation and Maintenance
Installation requires no specialized tools beyond common workshop equipment. The plug-and-play connectors ensure correct orientation that prevents reverse-polarity connections. Pre-formed wiring bundles conform to factory routing paths along HOWO firewalls and cowls, avoiding sharp edges that can damage wiring insulation. Flexible conduit sections allow for movement at hinge points without chafing. Vehicle technicians can typically complete replacement within 15 minutes per truck, minimizing operational disruption.
Proper maintenance ensures maximum service life for the 752-25453-6606 wiper harness. During annual HOWO truck inspections, technicians should verify connector security and inspect conduit sections for abrasion signs. Preventative cleaning of terminal contacts maintains optimal electrical conductivity between service intervals. While the weather-resistant materials withstand harsh environments, avoiding direct pressure washer sprays extends connection integrity.
Operational Impact
Truck fleet maintenance records demonstrate fewer electrical issues after upgrading to the OEM 752-25453-6606 harness compared to generic alternatives. The specifically engineered connectors maintain contact integrity across engine vibration frequencies common in heavy-duty diesel applications. Electrical continuity testing shows less than 0.2% resistance increase after 50,000 operational miles, a testament to durable construction.
Field testing proves the 752-25453-6606 harness outperforms competing products in high-moisture environments. The triple-layer connector sealing technique prevents water ingress during submersion scenarios common during flood navigation. This waterproof reliability gives HOWO operators confidence during extreme weather deployments when visibility systems become critical safety features.
In economic terms, the precision engineering of the 752-25453-6606 reduces operational costs through extended service intervals. The premium materials withstand environmental stressors that compromise standard wiring bundles. Fleet managers report 15-25% longer service life compared to universal fit alternatives, translating to reduced warehouse inventory requirements and purchasing overhead.