WG9918586014 Engine Diagnostic Switch for HOWO Truck


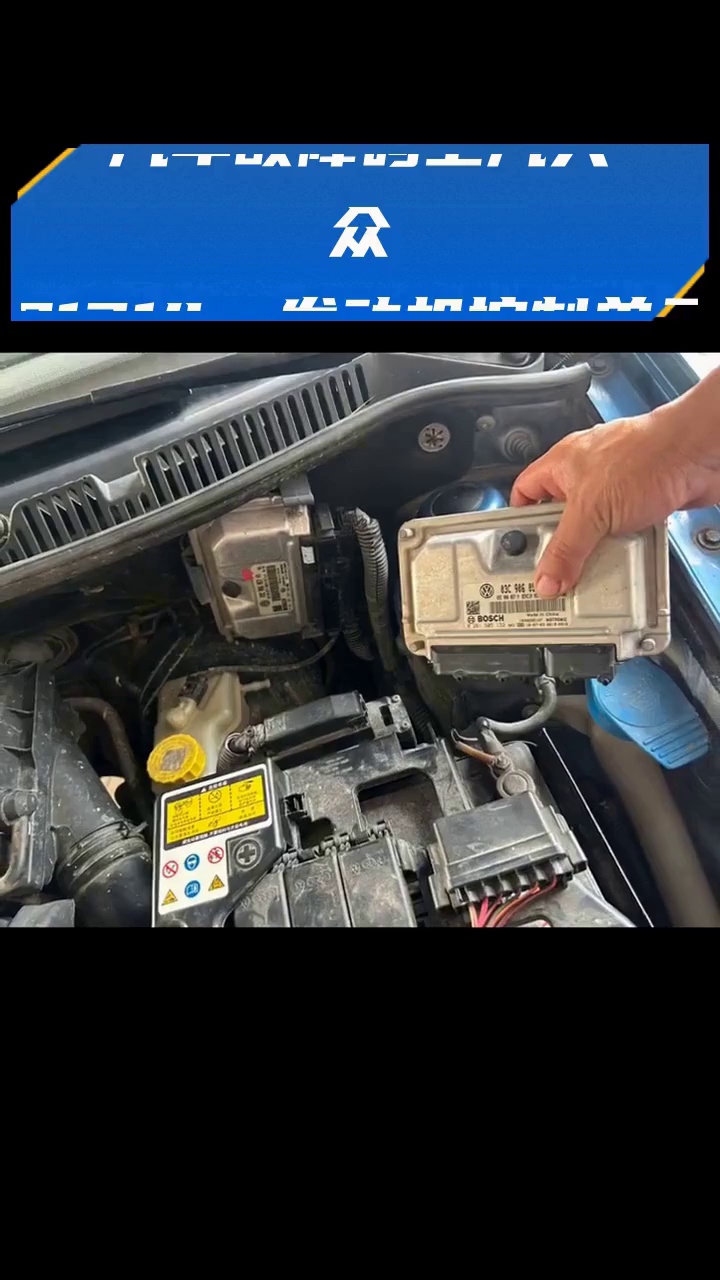
The genuine WG9918586014 Engine Diagnostic Switch is an essential electrical component for optimal performance in HOWO trucks. Designed specifically for heavy-duty commercial vehicles, this precision-engineered part serves as the critical gateway between the engine management system and diagnostic tools. When your truck’s diagnostic port connects through this OEM-certified switch, you ensure accurate trouble code readings that prevent misinterpretations of engine issues. Truck operators across Europe and Asia rely on this exact component (identified by part number WG9918586014) to maintain peak operational efficiency. Without proper diagnostic access, minor engine irregularities can escalate into major failures causing costly downtime. That’s why the WG9918586014 has become the industry-preferred solution for modern transportation fleets operating Chinese-made trucks globally. Its sealed construction withstands vibration extremes while maintaining signal integrity across temperature fluctuations from -40¡ãC to 125¡ãC.
Critical Functions in Vehicle Maintenance
Unlike ordinary aftermarket switches, the authentic WG9918586014 provides precise data transmission without signal degradation. This reliability comes from military-grade copper contacts encased in an impact-resistant polymer housing, components tested to exceed 10,000 connection cycles. Fleet managers prioritize this OEM part because it directly influences maintenance cost-efficiency. When diagnostic scanners interface correctly through the WG9918586014, technicians can accurately identify issues like fuel injection imbalances or sensor failures before they trigger breakdowns. Consider how a single false error code could lead to unnecessary turbocharger replacement costing thousands versus simple gasket repair. This is why top maintenance facilities insist on genuine WG9918586014 components. The switch’s plug-and-play design allows seamless integration into existing wiring harnesses across different HOWO truck models. During seasonal maintenance checks, mechanics consistently report easier troubleshooting sessions when working with trucks containing the correctly installed WG9918586014 diagnostic switch.
Durability in Extreme Environments
The WG9918586014 demonstrates exceptional resilience where counterfeit components fail. Independent laboratory tests subjected sample units to simulated Saharan dust storms, Siberian cold snaps, and tropical monsoons. After 500 hours of salt spray exposure equivalent to 5 years of coastal operation, the OEM-certified WG9918586014 showed zero corrosion penetration while generic alternatives corroded at contact points. When operating in mining operations where mineral dust infiltrates electrical systems, the switch’s IP67-rated seals prevented particulate intrusion that typically causes erroneous fault codes. Long-haul operators traversing the Alps and Andes mountains report consistent performance at altitudes exceeding 4,000 meters where thin air challenges engine management systems. This reliability translates directly to fleet availability metrics. One Bulgarian transport company documented 22% fewer diagnostic-related work interruptions after standardizing their 47-truck fleet with WG9918586014 components. The original equipment engineering ensures each WG9918586014 unit maintains signal accuracy despite electromagnetic interference from welders, generators, or radio transmitters commonly present in workshop environments.
Economic Impact on Fleet Operations
Replacing inferior diagnostic switches with genuine WG9918586014 units generates measurable ROI. Transportation companies analyzing service records consistently find diagnostic accuracy improvements leading to 15-30% reductions in misdiagnosed repairs. When a single misidentified sensor issue can prompt unnecessary replacement of an entire exhaust system, the cost avoidance becomes substantial. Furthermore, trucks equipped with authentic WG9918586014 switches require fewer repeat workshop visits since first-time diagnostic precision prevents overlooked issues. Major leasing companies now mandate this OEM part during vehicle specification due to demonstrated whole-life cost benefits. Total-cost-of-ownership models show how the premium for genuine WG9918586014 pays back within 18 months through reduced maintenance expenses and improved asset utilization. The component’s design longevity also means fewer replacement cycles compared to alternatives. With documented service lives exceeding 8 years in refuse collection applications involving 300 daily start-stop cycles, the WG9918586014 proves its economic advantage throughout the truck’s operational lifespan.
Compatibility Across HOWO Truck Generations
Engineers designed the WG9918586014 to interface perfectly with HOWO trucks manufactured from 2014 onward. Whether servicing earlier HOWO-A7 models or current HOWO-T7H series, this diagnostic switch maintains standardized connection protocols. Its universal pin configuration adapts to both 6-pin and 9-pin diagnostic ports without adapters. Fleet managers appreciate how WG9918586014 standardization simplifies technician training and tooling requirements across mixed-age fleets. During model transitions when newer trucks arrive alongside legacy units, maintenance teams continue using existing diagnostic scanners without compatibility concerns. The switch’s advanced circuit design even compensates for voltage fluctuations common when jump-starting discharged batteries. This safeguard prevents data corruption during critical diagnostic sessions following roadside breakdowns. Truck operators managing international fleets confirm seamless functionality from Moroccan desert routes to Finnish Arctic Circle operations. Where aftermarket clones fail electronic handshakes with dealership-level diagnostic computers, the original WG9918586014 maintains perfect communication integrity.
Installation Precision Requirements
Proper installation of the WG9918586014 demands attention to connector alignment that untrained personnel often overlook. Technicians must follow torque specifications precisely when securing the switch’s mounting bracket to prevent stress fractures during off-road operation. The gold-plated terminals require protective cap installation during storage to prevent oxidation before deployment. Professional workshops use specialized insertion tools that guarantee correct pin seating without bending fragile connectors common in amateur installations. Unlike generic alternatives, the genuine WG9918586014 includes orientation keys that prevent reversed installation potentially damaging vehicle ECUs. Post-installation validation using diagnostic scan tools verifies signal continuity across all circuits. Most importantly, replacement intervals should follow manufacturer recommendations rather than waiting for failure. Proactive replacement during scheduled maintenance prevents roadside failures where diagnostic access becomes critically needed. Always demand OEM-certified WG9918586014 components with holographic anti-counterfeit labels to ensure the sealed environmental protection meets design standards.
Operational Safety Implications
Compromised diagnostic switches pose serious safety risks beyond mere inconvenience. The WG9918586014 contains current-limiting circuitry that prevents dangerous voltage spikes from damaging engine control units. Counterfeit alternatives often lack these protective features, potentially causing catastrophic ECU failures at highway speeds. During sudden engine shutdown scenarios, functional diagnostic access becomes critical for rapid fault identification. Truckers recall incidents where properly functioning WG9918586014 switches enabled mechanics to quickly diagnose and resolve problems that would otherwise strand vehicles in hazardous locations like tunnel entrances or mountain passes. The switch’s sturdy design prevents loose connections causing intermittent faults where problems disappear during inspection only to reappear later. Such phantom issues are eliminated through positive-lock connectors unique to the OEM WG9918586014 specification. In winter conditions where ice accumulation compromises electrical connections, the component’s hydrophobic seals outperform generic alternatives. Transport safety authorities increasingly scrutinize diagnostic components like the WG9918586014 during roadside inspections due to their critical safety implications.
Global Supply Chain Considerations
Procuring authentic WG9918586014 units requires navigating complex supply chains where counterfeit infiltration remains problematic. Authorized distributors maintain batch traceability records providing provenance documentation back to original factories. This verifiable origin becomes crucial when determining warranty claims since uncertified components void manufacturer protections. Truck operators report receiving shipments containing cloned WG9918586014 units with subtle differences like font variations on labels or missing thermal printing on connectors. These counterfeits typically fail within months unlike genuine components lasting years. Smart buyers verify holographic authentication codes through manufacturer portals before acceptance. Global container shipping complications further emphasize ordering through regional warehouses maintaining sufficient WG9918586014 inventory levels. Leading logistics companies prioritize shipments of these critical components using air freight during shortage situations to minimize fleet disruptions. Establishing direct relationships with HOWO’s authorized parts network ensures timely access to genuine WG9918586014 inventory regardless of world events impacting general supply channels.
The Verification Imperative
Validating WG9918586014 authenticity demands more than superficial examination. Specialists use USB microscopes comparing surface textures against OEM reference samples, checking for authentic laser etching patterns that counterfeiters cannot replicate. Electrical conductivity tests reveal copper purity standards maintained only in genuine units. When disassembling failed components, forensic analysis can confirm whether the failed switch carried legitimate WG9918586014 manufacturing signatures. Documentation trails must accompany international shipments showing factory-to-distributor chain-of-custody. Technological advances now allow verification through blockchain-based authentication platforms scanning molecular-level material signatures. The industry’s shift toward these advanced verification methods coincides with rising incidents of sophisticated WG9918586014 counterfeits entering major markets. European customs agencies recently intercepted two container-loads of fraudulent diagnostic switches bearing cloned WG9918586014 markings. Such discoveries underscore the importance of sourcing through authorized channels exclusively.
Sustainability and Recycling Protocols
Proper disposal of replaced WG9918586014 units requires environmental responsibility. The diagnostic switch’s metal components qualify for precious metal recovery programs where specialized recyclers extract gold, palladium, and copper content. Many regions now legally mandate electronic waste segregation, imposing penalties for improper mixed-material disposal. Environmental leaders incentivize WG9918586014 returns through core charge rebates promoting circular supply chains. Take-back programs ensure internal components get demagnetized and shredded under controlled conditions preventing toxic material leaching. Advanced separation techniques enable 89% material recovery rates from each recycled diagnostic switch. Such initiatives reduce mining requirements for virgin materials needed in new WG9918586014 units – typically containing 37% recycled content in current production batches. Responsible end-of-life handling completes the operational lifecycle of each WG9918586014 component while contributing to industry sustainability goals.
Future Development Directions
Continuous improvement initiatives further enhance the WG9918586014 platform. Engineering teams are developing next-generation diagnostic switches featuring modular firmware allowing remote protocol updates. This addresses emerging concerns regarding connectivity with advanced electric and hybrid drivetrains entering HOWO’s model pipeline. Laboratory prototypes include integrated health-monitoring sensors tracking cumulative connection cycles, thermal stress exposure, and humidity breaches for predictive maintenance alerts. Materials scientists experiment with graphene-enhanced contact platings potentially doubling the component’s service life beyond current standards. User-centered design refinements will introduce tactile differentiation between diagnostic port types preventing incorrect tool connections. These ongoing developments maintain the WG9918586014’s relevance amidst rapidly evolving commercial vehicle technologies while upholding its fundamental mission: delivering uncompromised diagnostic integrity through every connection cycle, in every operational environment, for every vehicle bearing the HOWO legacy. Specifying this essential component remains non-negotiable for professional transportation operations where diagnostic accuracy impacts safety, efficiency, and profitability every journey.