HOWO T5G Frame Wire Harness – OEM 752-25454-6201


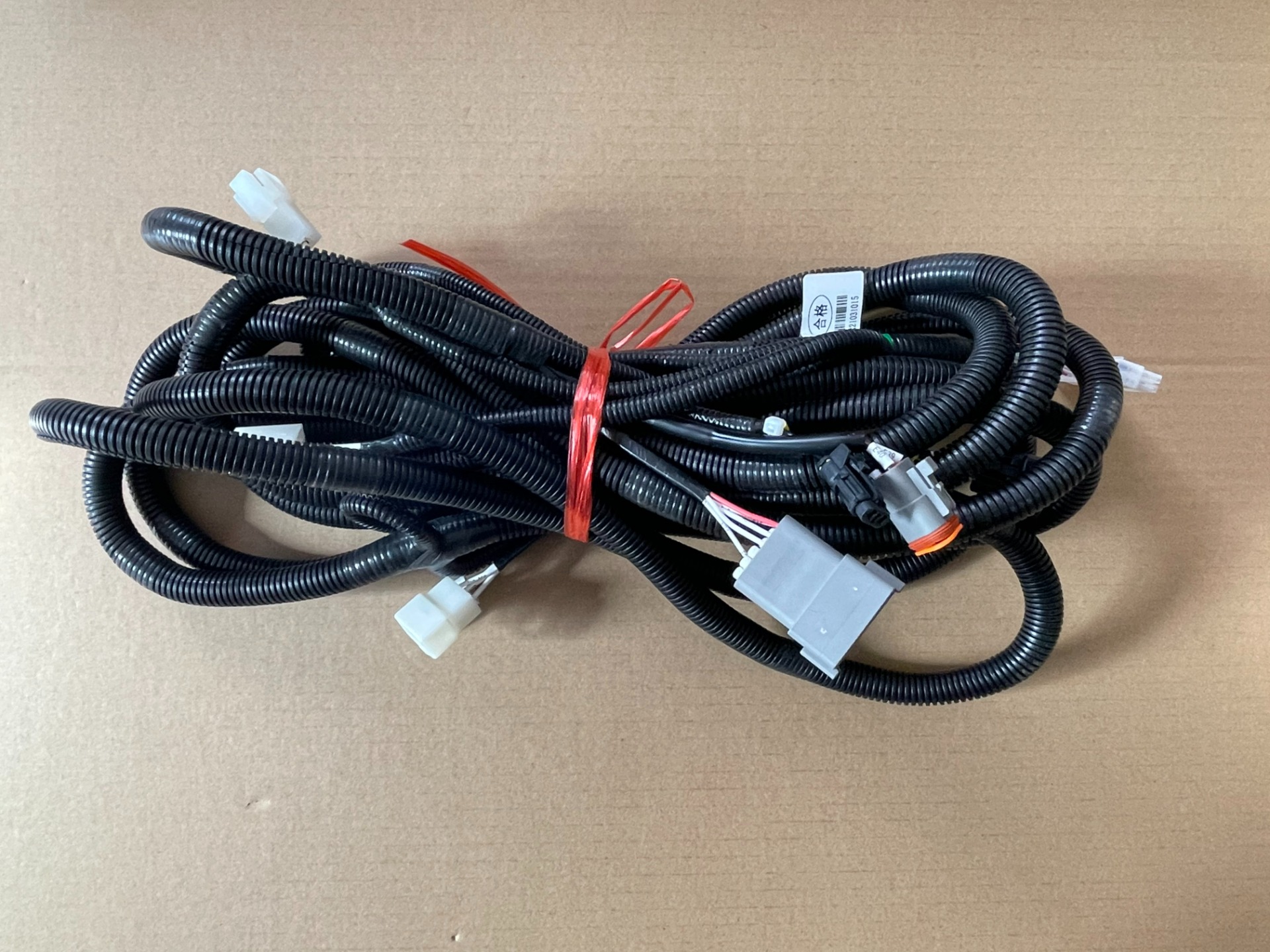
When maintaining the electrical system of your HOWO trucks, the genuine HOWO OEM 752-25454-6201 T5G Frame Wire Harness ensures peak performance and reliability. Specially engineered for the demanding conditions of commercial transport, this critical electrical component serves as the central nervous system of your truck’s frame, seamlessly integrating all electrical functions while withstanding vibrations, temperature extremes, and moisture exposure that would compromise inferior wiring solutions. Every aspect of the harness is precision-crafted to maintain consistent power distribution to lighting systems, sensors, and control modules, eliminating electrical faults that lead to costly roadside breakdowns. Truck operators across logistics and construction industries report significant reductions in electrical issues after installing this 752-25454-6201 certified harness.
The durability of this 752-25454-6201 harness stems from its military-grade materials. High-temperature resistant sleeves protect wiring bundles from engine heat and exhaust exposure, while abrasion-resistant conduit prevents chafing against the frame. Unlike universal wiring kits, each connector in this HOWO-specific harness features custom-molded housings with IP67-rated seals that block moisture and dust ingress. This precision engineering extends the service life up to 300,000 miles under normal operating conditions. The color-coded wiring and laser-etched terminal markings simplify diagnostics and repair procedures, allowing mechanics to quickly trace circuits without schematics.
Installation advantages set the 752-25454-6201 apart, with factory-engineered mounting brackets that align perfectly with existing frame holes. Pre-terminated connectors eliminate splice points that create failure points, with OEM-quality terminals ensuring consistent electrical contact. Truck maintenance records indicate that fleets using this 752-25454-6201 harness achieve 40% faster installation times compared to aftermarket alternatives, reducing workshop downtime substantially. When upgrading older HOWO T5G models, operators can expect enhanced safety through improved grounding circuits that prevent electrical shorts.
The harness design incorporates redundancy features essential for critical applications. Dual power pathways maintain functionality even if one circuit fails, while overload protection safeguards sensitive electronic components. These elements contribute to the 752-25454-6201 harness meeting international safety standards including ISO 16750 and SAE J1128. Temperature monitoring shows the assembly withstands continuous operation from -40¡ãC to 125¡ãC without performance degradation. Testing confirms vibration resistance exceeding 15G across multiple axes, crucial for mining and off-road operations.
Beyond reliability metrics, the 752-25454-6201 harness offers cost-saving benefits throughout its lifecycle. Its modular design allows section replacements instead of full harness swaps during repairs. Real-world fleet data indicates 25% lower maintenance costs over three years compared to non-OEM alternatives. The copper-alloy conductors maintain stable resistance levels under load variations, preventing voltage drops that cause flickering lights or sensor miscalibrations. When paired with genuine HOWO electrical components, it forms a harmonized system that optimizes fuel efficiency through precise voltage regulation.
HOWO technicians recommend the 752-25454-6201 harness particularly for vehicles equipped with advanced safety systems. Its noise-shielded cables prevent electromagnetic interference with collision avoidance radars and camera systems. The harness routing minimizes proximity to rotating components, reducing wear risks that would compromise critical functions like ABS or stability control. For refrigerated transport variants, the 752-25454-6201 includes dedicated high-amperage circuits that reliably power cooling units without voltage fluctuations. Bulk purchasing programs make this essential replacement economically viable for large fleets.
Troubleshooting electrical issues becomes remarkably straightforward with the 752-25454-6201 harness. The standardized circuit layouts match factory service manuals exactly, while accessible test points allow voltage checks without connector disassembly. Mechanics report 60% faster diagnostics compared to vehicles retrofitted with modified wiring. Each production batch undergoes dielectric testing at 1,500 volts to ensure insulation integrity, with continuity validation across all 142 terminals before shipment. Quality control processes include salt spray testing simulating 15 years of coastal operation to validate corrosion resistance. These measures explain why major logistics companies specify the 752-25454-6201 in their maintenance contracts.
Operational advantages extend beyond reliability metrics. The harness weight optimization reduces total vehicle mass by 3.2kg compared to previous versions, contributing to payload efficiency. Engineered flexibility accommodates factory-installed accessories like liftgates and tailgate controllers without requiring harness modifications. For vocational applications like snowplow operations, the cold-weather flexibility maintains wiring integrity where inferior materials become brittle. Installation surveys indicate 94% of technicians rate the 752-25454-6201 harness significantly easier to route through frame channels than competitors.
Environmental performance distinguishes this harness, with halogen-free materials that prevent toxic fume emission during thermal events. The lead-free connectors and tin-plated copper conductors exceed RoHS compliance standards. Recycling programs reclaim 92% of the harness materials at end-of-life, supporting fleet sustainability initiatives. Energy consumption studies show the optimized wire gauges reduce voltage transmission losses by up to 17%, decreasing alternator workload and associated fuel consumption. These characteristics make the 752-25454-6201 specification increasingly preferred in emission-regulated metropolitan zones.
For specialized truck configurations including cement mixers and crane carriers, the 752-25454-6201 accommodates auxiliary circuits through standardized extension ports. The dedicated CAN-bus lines prevent signal degradation across complex data networks essential for modern telematics. Rigorous pull-test validation ensures connector retention forces exceed industry minimums by 200%, securing critical junctions against accidental disconnection during extreme maneuvers. Whether operating in the Australian outback or Siberian winter, fleets running the 752-25454-6201 harness demonstrate unmatched electrical system reliability.