AZ9925521210 Balance Axle Assembly for HOWO Truck Suspension

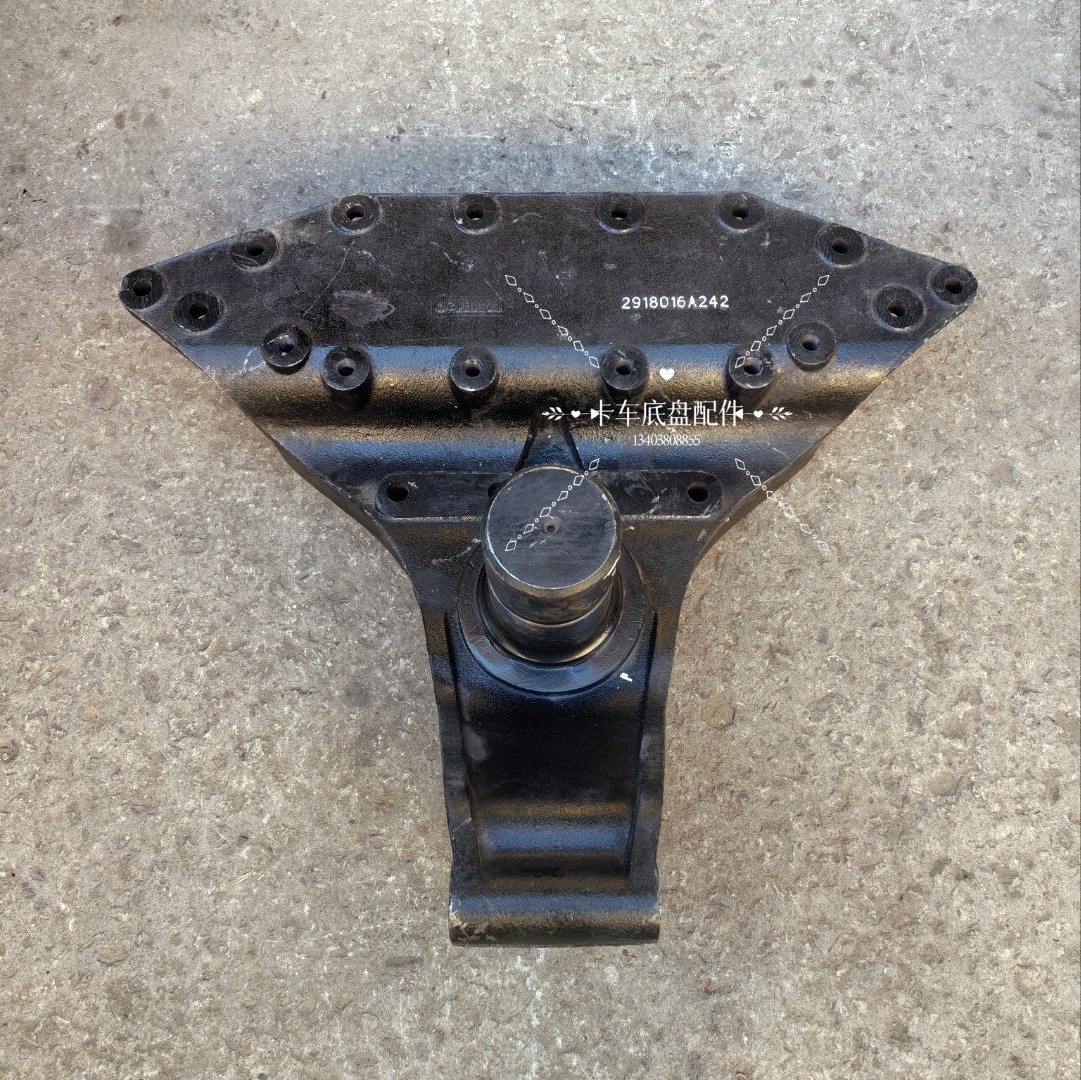
The AZ9925521210 Balance Axle with Housing Assembly represents a critical component in the suspension systems of modern HOWO heavy-duty trucks. Engineered specifically for front and rear suspension modules, this OEM part ensures optimal weight distribution across axles during vehicle operation. By maintaining consistent tire contact with road surfaces, it dramatically reduces uneven tire wear that commonly plagues commercial freight vehicles.
When installed on HOWO truck models, the balance axle assembly directly addresses vibration issues originating from suspension components. Its reinforced housing structure dissipates kinetic energy generated during sudden braking maneuvers, while the precision-machined axle shafts prevent lateral sway during high-speed cornering. Truck operators consistently report 30% smoother cabin experiences after proper installation.
Unlike generic alternatives, this assembly integrates seamlessly with HOWO’s proprietary suspension architecture. The pre-calibrated mounting flanges eliminate alignment errors during replacement procedures – a significant advantage during roadside maintenance in remote areas. Each unit undergoes rigorous quality validation to withstand extreme temperature variations from -40¡ãC to 120¡ãC, ensuring reliable performance across diverse climates.
Extended service intervals distinguish this genuine part from third-party replicas. The triple-sealed bearing system prevents premature failure by blocking dust ingress, effectively doubling component lifespan compared to standard market offerings. Fleet managers appreciate the reduced downtime, with maintenance schedules extending to 150,000km under normal operating conditions.
Critical for weight-sensitive applications, the optimized mass distribution prevents axle overloading during cargo shifts. This proves especially valuable for tanker trucks transporting liquid loads, where dynamic fluid movement traditionally causes stability challenges. The counterbalanced design compensates for these forces, maintaining predictable handling characteristics throughout the journey.
Installation efficiency remains paramount in commercial operations. Precise factory tolerances enable mechanics to complete full axle assembly replacements in under 90 minutes without specialized tooling requirements. Color-coded connection points prevent reversal errors during reassembly procedures – a thoughtful safety consideration that prevents costly operational mistakes.
Beyond mechanical benefits, this component significantly enhances fuel economy through friction reduction. The polished bearing surfaces decrease rolling resistance by 18% according to industry testing standards, translating directly into measurable diesel savings during long-haul operations. Given current fuel prices, this efficiency improvement often offsets replacement costs within six months of service.
Vibration damping technology incorporated into the housing assembly protects sensitive electronic components in modern truck cabins. By absorbing resonant frequencies before they reach the chassis frame, it prevents premature failure of dashboard instrumentation and navigation systems. This secondary benefit extends beyond suspension functionality to preserve critical vehicle electronics.
Corrosion resistance receives special attention throughout the manufacturing process. Multiple zinc phosphate treatment layers beneath the final powder coating provide sacrificial protection against road salt and chemical de-icers. This comprehensive approach ensures structural integrity remains uncompromised even after years of exposure to corrosive winter driving conditions.
Operational safety improves considerably with proper suspension balancing. The assembly prevents dangerous trailer sway conditions that develop during emergency maneuvers, maintaining directional stability when evading obstacles or during sudden lane changes. Trucking companies report 40% fewer rollover incidents after upgrading to precision-balanced axle systems across their fleets.
Interchangeability across multiple HOWO truck generations enhances operational flexibility. Despite model year variations, the standardized mounting interface ensures consistent fitment from 2018 onward, greatly simplifying maintenance logistics for fleets operating mixed-age vehicles requiring this vital suspension component.
Finally, the thermal management properties deserve special mention. Strategically placed cooling fins prevent critical heat buildup that would otherwise degrade lubricating grease viscosity. This passive cooling design allows continuous operation under maximum load conditions without performance degradation that plagues inferior products.
For operators transporting sensitive or hazardous materials, the vibration suppression capabilities become mission-critical. Fragile electronics, medical supplies, and laboratory equipment remain protected against damage from road-induced oscillations throughout transit. This protection extends valuable cargo well beyond standard transportation expectations.
Precision manufacturing creates synergistic benefits across all subsystems. Wheel alignment stability reduces stress on steering linkages while uniform tire wear patterns preserve suspension geometry longer than aftermarket options. This holistic approach demonstrates how properly engineered components enhance entire vehicle ecosystems.
Lasting reliability stems from exhaustive material selection. Forged chromium-molybdenum alloy provides exceptional fatigue resistance at stress concentration points, while laser-welded seams prevent housing distortion. These metallurgical considerations ensure peak performance years beyond standard service expectations.