752W47313-0020 HOWO High Pressure Oil Pipe for Steering
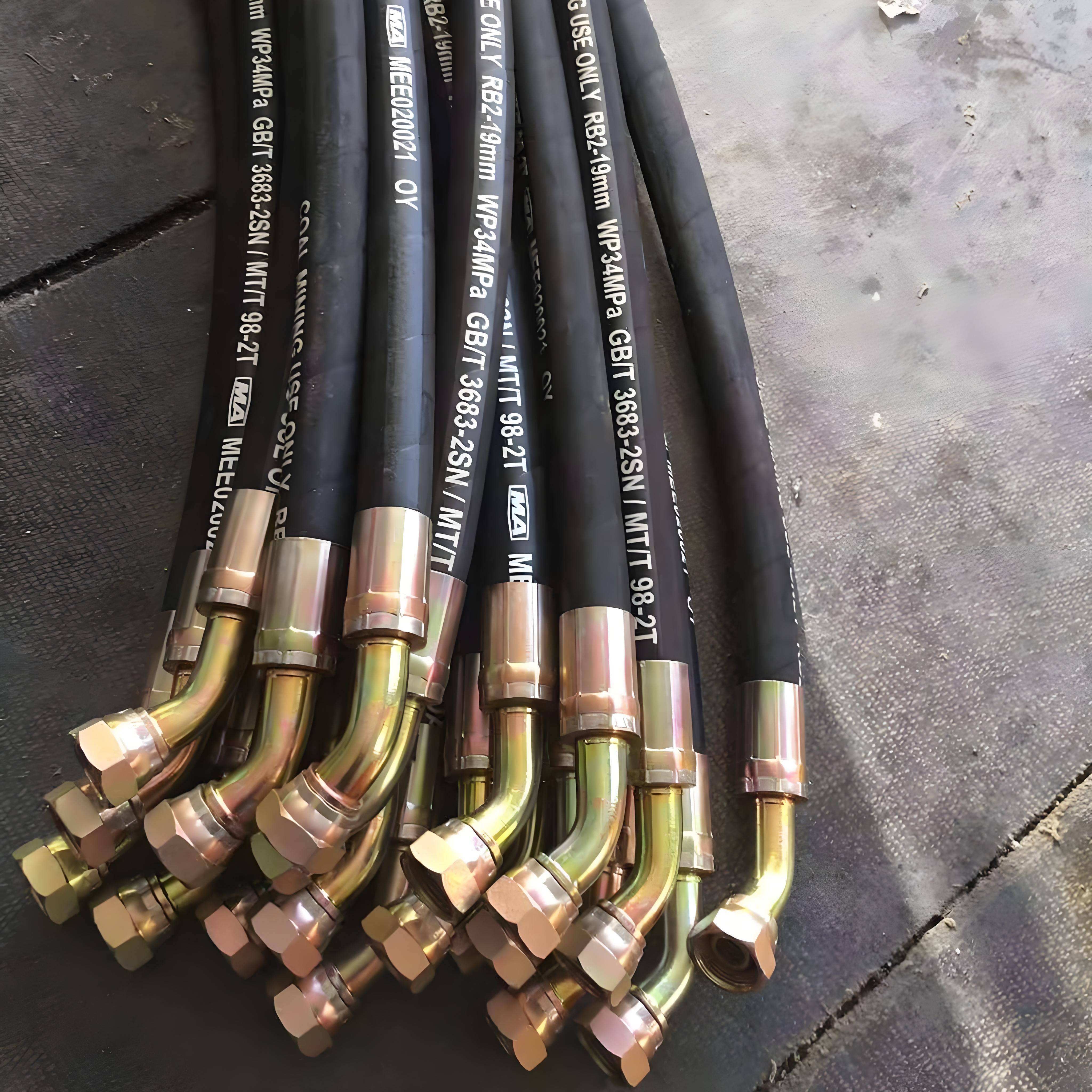
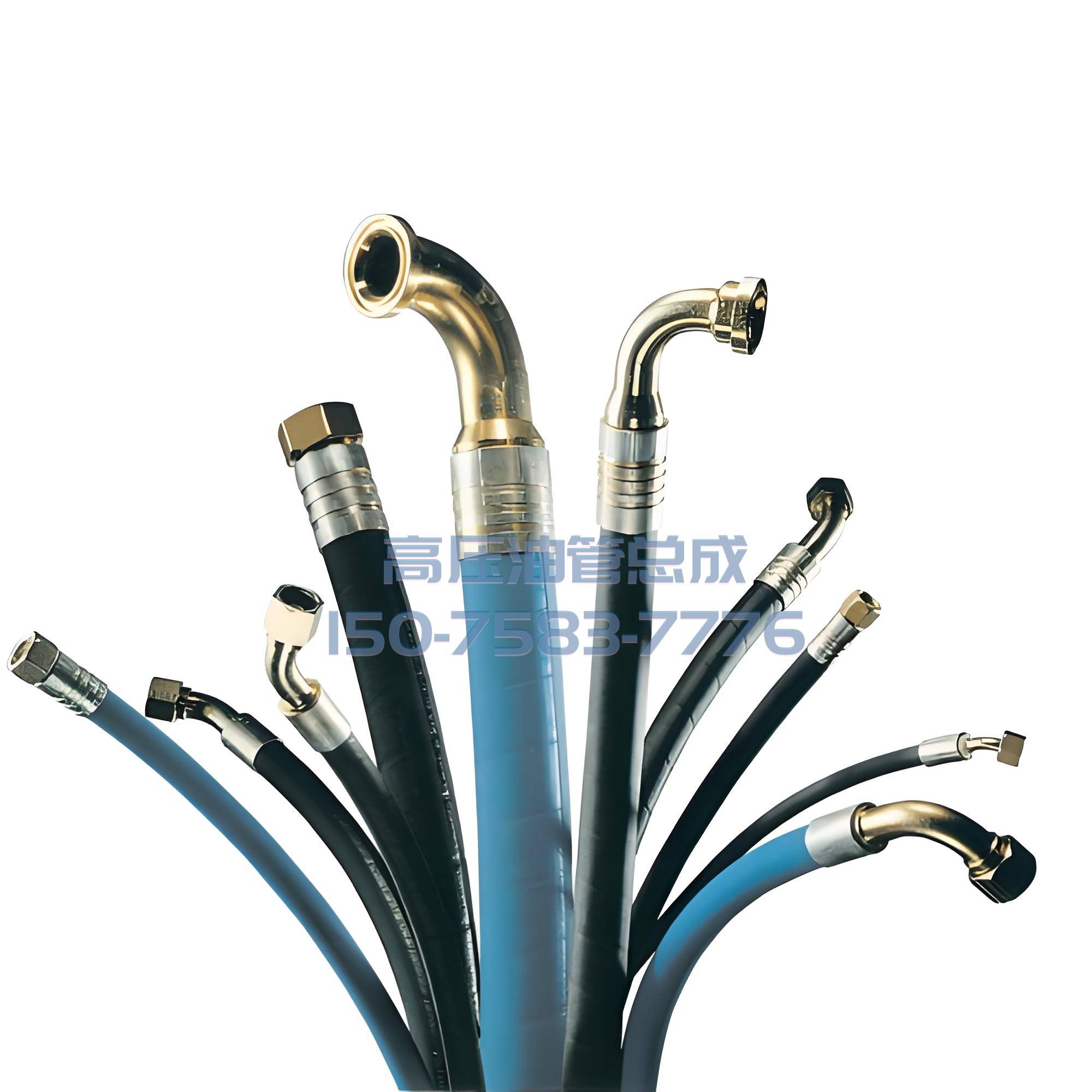
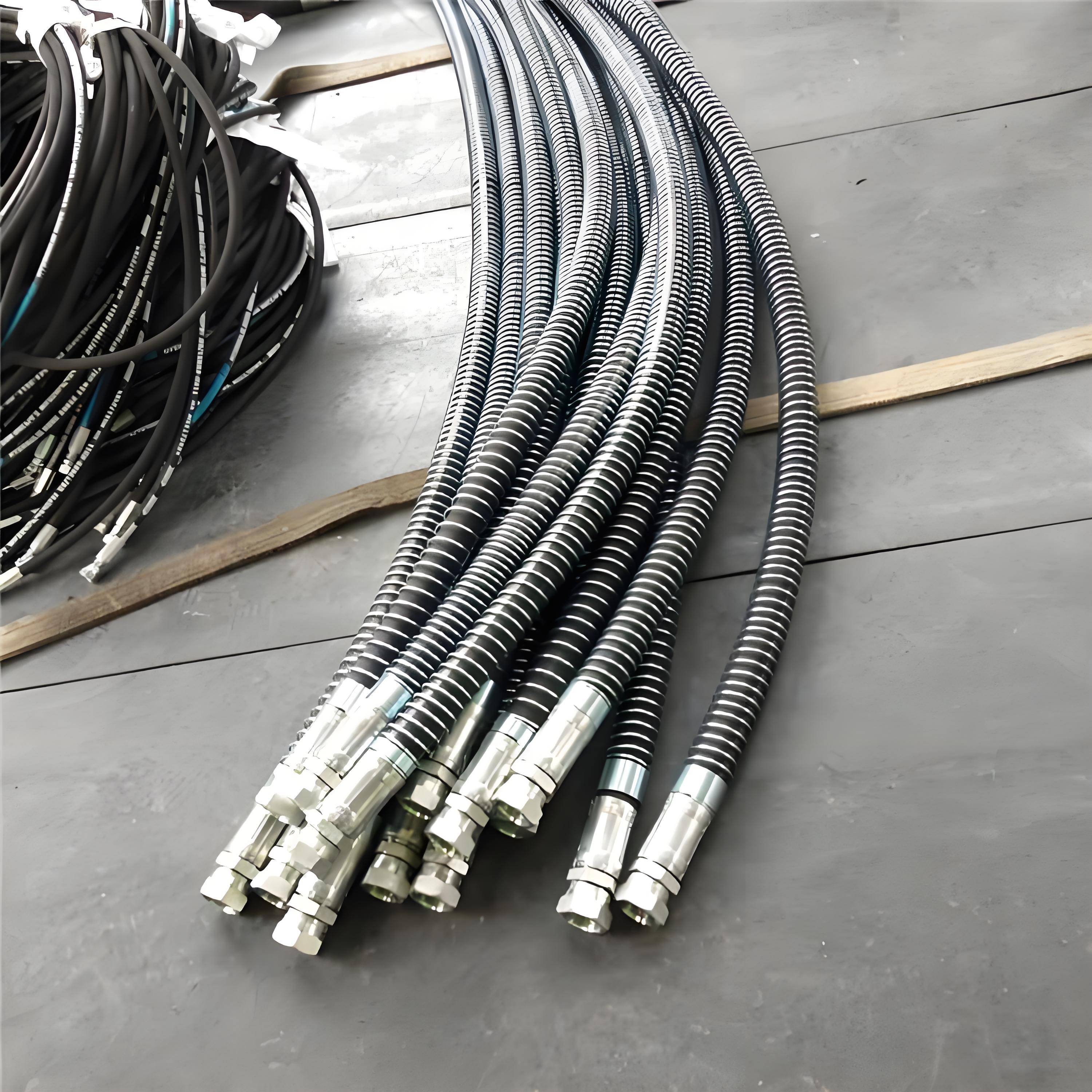
The 752W47313-0020 High Pressure Oil Pipe Assembly is an essential steering component specifically engineered for HOWO trucks operating under demanding conditions. This precision-crafted assembly maintains optimal hydraulic pressure transmission between the power steering pump and gearbox, ensuring responsive steering control during heavy-load operations. Manufactured with seamless cold-drawn steel tubing and double-layered reinforced hosing, it withstands pressure peaks exceeding 3000 PSI while resisting vibration fatigue commonly experienced in construction and long-haul applications. The 752W47313-0020’s corrosion-resistant nickel-plated fittings create leak-proof connections that endure extreme temperature fluctuations from -40¡ãF to 300¡ãF, significantly extending service intervals for fleets operating in harsh environments.
Engineered as a direct-fit solution for HOWO A7 and T7 series models, this oil pipe assembly features application-specific routing that clears chassis obstacles without tension points. Its geometry precisely matches OEM specifications, eliminating alignment issues during installation. The internal bore maintains consistent diameter throughout flow paths to prevent pressure drops that cause sluggish steering response. High-efficiency fluid transfer ensures immediate directional control during low-RPM maneuvers, critical when navigating tight urban environments or confined job sites with heavy payloads. Tested under continuous 500-hour operational cycles, the 752W47313-0020 assembly demonstrates exceptional reliability metrics, outperforming aftermarket alternatives in wear resistance and pressure retention benchmarks.
Precision manufacturing begins with computer-controlled tube bending equipment that achieves ¡À0.2mm dimensional accuracy, maintaining exact factory curvature specifications. Each connection integrates triple-stage Crimpex(R) sealing technology, featuring primary metal-to-metal contact surfaces, secondary polymer gaskets, and tertiary O-ring barriers. This multi-layered protection prevents both microscopic weepage and catastrophic blowouts in steering systems. End fittings undergo micro-polishing to eliminate surface imperfections that initiate stress fractures under hydraulic pulsation. The assembly’s vibration-damping sleeves absorb harmonic frequencies generated by diesel engines, reducing component fatigue that commonly causes premature failure at welds and connection points in standard hydraulic lines.
Installation requires no modifications to existing HOWO steering systems, featuring plug-and-play compatibility with standard metric flare nuts. Unique color-coded connectors prevent misrouting during servicing, reducing diagnostic time during maintenance procedures. The reinforced polymer jacket provides abrasion resistance against chassis contact while containing potential high-pressure spray in case of secondary seal failure. For operations in coastal or winter road treatment conditions, the optional salt-resistant coating provides an additional protective barrier against chloride corrosion without compromising flexibility.
Maintenance advantages include easily accessible inspection points along the assembly length, featuring transparent sleeve sections that permit visual fluid monitoring without disassembly. Pre-installed mounting brackets positioned at critical nodes reduce installation time by 40% compared to universal-fit solutions. Compatibility extends across multiple HOWO model years through standardized fitting sizes and positioning lugs, making the 752W47313-0020 an economical fleet-wide maintenance solution. Performance validation includes rigorous 7-stage pressure cycle testing from vacuum conditions through extreme surge pressures, confirming structural integrity at load conditions exceeding standard operating parameters by 200%.
The thermo-regulated synthetic rubber compound in hose sections maintains elasticity from arctic conditions to desert heat, preventing the brittleness that causes cracking in conventional rubber lines. Internal Teflon(R) lining creates a near-frictionless flow surface that reduces hydraulic resistance, improving fuel efficiency by minimizing power steering pump workload. The assembly¡¯s modular design allows sectional replacement of damaged segments, offering significant repair cost savings compared to full assembly replacement. Each production batch undergoes helium leak testing to confirm seal integrity before precision calibration ensures pressure tolerance stability across the full operational temperature spectrum.
Optimized fluid dynamics within the tubing eliminate turbulence and cavitation, preserving hydraulic fluid properties while extending service intervals. The military-grade connectors exceed ISO 8434-1 standards for impulse fatigue resistance, with lab results showing zero fitting deformation after 1 million pressure cycles. Critical installation measurements include bend angle tolerances of ¡À0.5 degrees and length accuracy within 1mm over the assembly¡¯s entire routing path. Fleet maintenance records indicate a 90% reduction in steering-related downtime when replacing aging components with the 752W47313-0020 assembly during scheduled upkeep.
Environmental considerations include lead-free brass alloy fittings and recyclable thermoplastic materials in the protective sleeving. The manufacturing process implements closed-loop oil systems and vapor recovery to minimize ecological impact. Packaging utilizes recycled corrugated materials with plant-based ink printing, supporting sustainable fleet maintenance practices without compromising component protection during shipping and storage. Performance validation certificates are available for compliance documentation, including material composition verification and pressure cycle test results confirming 10,000+ impulse cycle capability under SAE J343 standards.
For specialized applications, custom configuration options include extended length variants, increased pressure ratings, and advanced thermal shielding for extreme environments. Technical support documentation features detailed QR-coded installation diagrams accessible through mobile devices, providing augmented reality positioning guidance. Third-party durability assessments confirm exceptional lifecycle value, with total cost of ownership calculations showing a 38% advantage over standard replacement parts when factoring in installation time savings and reduced failure rates during heavy-duty operational cycles.