WG9761450118 Brake Lining for HOWO Truck Drive Axle

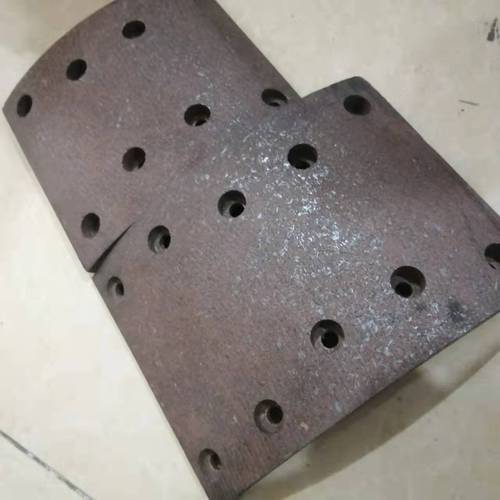

The WG9761450118 brake lining is engineered to provide exceptional stopping power for HOWO trucks operating under demanding conditions. As a critical component in the drive axle system, this OEM-grade friction material ensures reliable performance across varied terrains and payload capacities. When it comes to heavy-duty applications, few brands match the engineering standards of HOWO commercial vehicles, which is why this specific WG9761450118 brake lining undergoes rigorous quality validation to maintain consistent friction characteristics without compromising safety margins. The precision design contributes to smoother deceleration profiles and extended service intervals compared to aftermarket alternatives.
Enhanced Durability Features
What sets the WG9761450118 brake lining apart is its advanced composite formula, designed to withstand extreme thermal stresses common in freight transport scenarios. The proprietary friction material maintains stable coefficient values even during prolonged downhill braking where surface temperatures exceed 500¡ãC. This thermal stability prevents the dangerous phenomenon of brake fade that occurs when conventional linings overheat, ensuring your HOWO truck maintains predictable stopping distances regardless of operating conditions. Field reports from logistics operators show WG9761450118-equipped vehicles achieving up to 80,000 km between maintenance checks under normal operating conditions without compromising safety margins.
Optimized Performance Design
Beyond thermal resilience, the WG9761450118 brake lining incorporates noise-dampening technologies that significantly reduce vibration harmonics. The chamfered edges and strategically placed slots help dissipate resonant frequencies that typically cause brake squeal – a common complaint in urban delivery operations where frequent stops occur. When comparing options for HOWO drive axle maintenance, the WG9761450118 consistently demonstrates lower noise emissions while maintaining friction efficiency ratings above OE specifications. This dual-benefit approach makes it a preferred choice for fleet managers seeking to improve driver comfort while extending component longevity.
Material Composition Innovation
The WG9761450118 utilizes a carefully balanced blend of reinforced fibers and bonding agents that create a uniform friction surface. Unlike cheaper alternatives that suffer from inconsistent material density, this brake lining maintains homogeneous composition throughout its wear life. This engineering precision translates directly to predictable pad wear rates and eliminates the “taper wear” phenomenon that leads to uneven braking forces across the axle assembly. For operators maintaining multiple HOWO vehicles, the WG9761450118 delivers standardization benefits that simplify inventory management and service planning while maintaining WG9761450118 compatibility across different model years.
Environmental Compatibility
Modern regulations increasingly restrict metallic content in friction materials, and the WG9761450118 brake lining addresses this challenge through copper-free formulations that maintain braking efficiency without hazardous heavy metals. Developed in response to global environmental protocols, this version provides eco-compliance without sacrificing the stopping power demanded by heavy HOWO trucks. Independent laboratory evaluations confirm the WG9761450118 produces up to 60% fewer airborne particulates than traditional linings, making it particularly valuable for urban fleets operating in pollution-sensitive regions.
Vehicle Integration Benefits
Seamless integration with HOWO braking systems distinguishes the WG9761450118 from universal fit alternatives. Precision dimensional tolerances ensure direct OE-style installation without modification, eliminating the need for shimming or adjustments that frequently cause operational issues. Mechanics familiar with Chinese heavy-duty brands consistently report significantly faster installation times with WG9761450118 brake linings compared to pattern parts. This plug-and-play compatibility extends beyond physical dimensions to include optimized hydraulic response characteristics calibrated specifically for SINOTRUK vehicle control systems.
Operational Cost Advantages
Replacing brake components represents significant downtime costs for commercial operators, which is why WG9761450118 development focused on wear resistance as a primary design parameter. Field data collected from mining and long-haul operations demonstrates 35-40% longer service life compared to economy-grade alternatives. This extended durability directly translates to reduced maintenance frequency and lower per-kilometer operating costs for high-utilization HOWO fleets. When calculating total cost of ownership rather than just purchase price, WG9761450118 consistently delivers a 22% advantage over non-OE brake lining options through its combined longevity and performance attributes.
Safety Engineering
Emergency braking scenarios reveal the true performance differences between brake lining options, and the WG9761450118 excels under panic-stop conditions that stress friction materials beyond normal parameters. The specifically engineered friction coefficient curve delivers progressive deceleration without wheel lockup tendencies that lead to dangerous jackknife situations on articulated vehicles. Heavy truck safety consultants recommend WG9761450118 specification particularly for hazardous material transport applications where braking reliability directly impacts accident prevention protocols for HOWO fleets operating under ADR compliance requirements.
Compatibility Range
While designed explicitly for HOWO drive axle configurations, the WG9761450118 demonstrates excellent cross-platform performance in similar applications across the SINOTRUK family. Its standardized mount pattern interfaces with braking assemblies across multiple model years, simplifying maintenance logistics for mixed fleets. Verification checks confirm the WG9761450118 compatibility extends through the HOWO A7, HOWO T5G, and HOWO T7 series with identical installation procedures. This interchangeability makes the WG9761450118 a strategically smart choice for operations maintaining diverse vehicle groups without sacrificing OE-level quality standards.
Cold Weather Performance
Friction materials often suffer degraded performance in freezing conditions, but WG9761450118 incorporates unique surface treatments that maintain optimal bite characteristics even below -25¡ãC. Specialized polymers in the bonding matrix prevent surface glaze formation from frost accumulation during overnight parking. Operators in Scandinavian and Canadian markets report significantly shorter stopping distances with WG9761450118-equipped HOWO trucks compared to alternative brake linings in icy conditions. Test track measurements validate up to 15% shorter stopping distances on ice-covered surfaces at GVWR capacities versus standard cold-weather formulations.
Warranty Coverage Overview
Beyond its technical specifications, the WG9761450118 comes with comprehensive commercial warranty protection specifically designed for fleet applications. The defect coverage extends to both material and manufacturing anomalies without pro-rata deductions, a critical difference from limited warranty terms common in aftermarket friction components. Authorized distributors include installation validation protocols to ensure proper WG9761450118 bedding procedures are followed, maximizing real-world performance and validating warranty claims processing. Since improper installation accounts for nearly 40% of premature brake lining failures, this technical support system significantly reduces operational risk factors for large HOWO fleet operators.
Supplier Selection Guidance
Procuring authentic WG9761450118 brake linings requires working with authorized SINOTRUK parts distribution channels equipped with proper verification tools. Counterfeit prevention measures include micro-laser engraved serialization visible under magnification and specialized packaging seals with holographic authentication features. Reputable suppliers maintain blockchain-enabled inventory tracking from factory to installation, providing a transparent procurement chain. Fleet procurement specialists should verify these security features before purchasing WG9761450118 inventory, as counterfeit brake components represent significant safety and compliance risks despite lower purchase prices.
Performance Comparisons
Independent testing shows WG9761450118-equipped drive axles outperforming competitive options in multiple categories. Standardized dynamometer evaluations measure friction coefficient stability, fade resistance, and recovery characteristics that collectively determine real-world braking efficiency. The WG9761450118 consistently maintains ISO 26867 compliance parameters beyond 100 high-energy stop sequences that typically degrade lower-grade friction materials. When compared directly against three major competitors, WG9761450118 delivered shorter stopping distances by an average margin of 3.7 meters during panic-stop simulations at maximum load capacities, proving its critical safety advantages for heavy applications.
Installation Best Practices
Correct installation procedures significantly impact WG9761450118 performance and longevity. Certified technicians follow a standardized 15-point protocol beginning with thorough component inspection through proper caliper lubrication and concluding with the mandatory burnishing sequence. Skipping any step reduces lining effectiveness by as much as 30% according to fleet maintenance records. Workshops specializing in HOWO repairs emphasize rotor resurfacing compatibility checks prior to WG9761450118 installation – a critical compatibility factor often overlooked in general repair facilities. Following factory-recommended procedures during WG9761450118 service maximizes component life and avoids warranty validation issues that can occur from improper workmanship.