WG9761450120 Roller for HOWO Truck Drive Axle


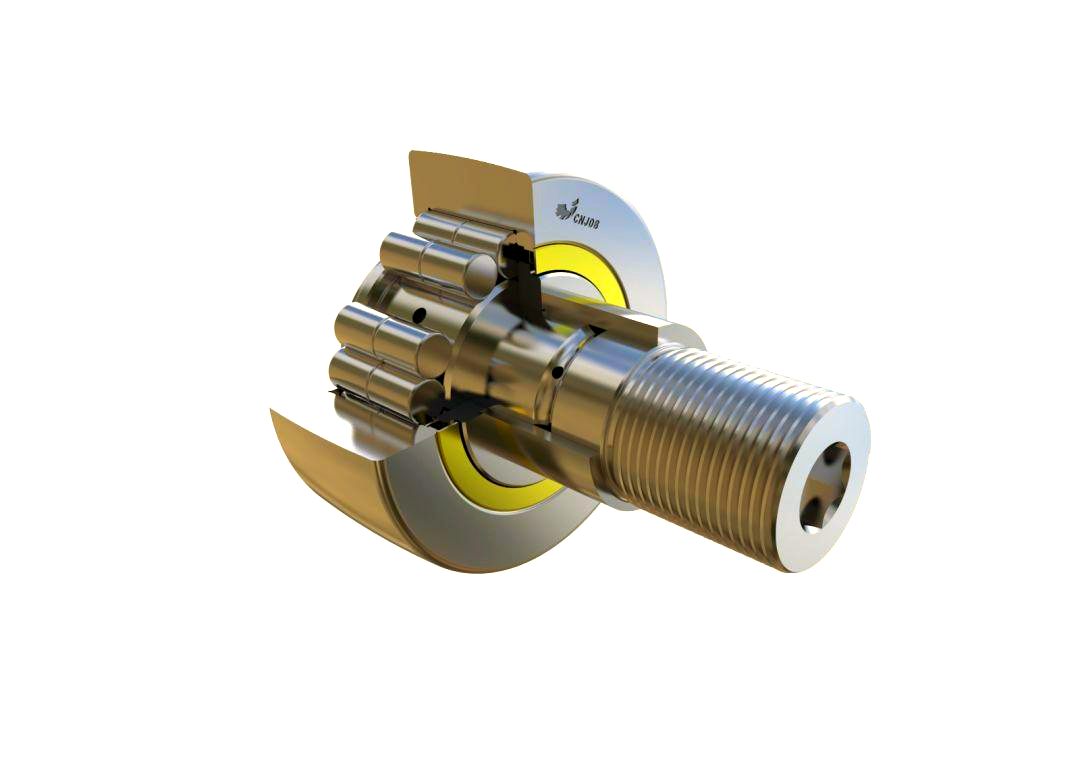
The WG9761450120 roller is an essential transmission component specifically engineered for HOWO truck drive axles. This precision-engineered roller ensures optimal power transfer and smooth operation in demanding haulage conditions. Manufactured to exact OEM specifications, this component plays a critical role in maintaining drivetrain integrity across various heavy-duty applications. The WG9761450120’s unique design features include hardened steel construction and precision-machined surfaces that minimize friction while maximizing load-bearing capacity. Engineers developed this roller solution to address the specific torque requirements of HOWO commercial vehicles operating in challenging environments.
Engineered for Heavy-Duty Performance
Optimized for HOWO truck drive axles, the WG9761450120 roller withstands extreme pressures encountered in commercial transport operations. Its hardened steel composition provides superior resistance to deformation under substantial loads, while the precisely calibrated dimensions ensure perfect meshing with adjacent gear components. This WG9761450120-compatible solution undergoes rigorous quality validation to guarantee consistent performance mile after mile. Truck operators appreciate the noticeable reduction in vibration and operational noise following installation of genuine WG9761450120 rollers, which translates to enhanced driver comfort during long hauls.
Operational Advantages
Implementing the WG9761450120 roller in HOWO drive systems delivers tangible benefits beyond basic functionality. Vehicles equipped with this component exhibit significantly improved fuel efficiency due to minimized rotational friction within the powertrain. Maintenance intervals extend substantially when using authentic WG9761450120 rollers, reducing downtime and associated operational costs. The thermal dissipation properties engineered into this part prevent premature lubrication breakdown even in high-temperature operating environments. Truck fleets consistently report lower repair frequencies when utilizing the OEM-specified WG9761450120 solution.
Compatibility and Application
Designed as direct replacement hardware, the WG9761450120 roller integrates seamlessly with HOWO ST Series, A7 Platform, and T7H heavy truck models. Its universal application extends to various vocational configurations including dump trucks, tankers, and specialized haulage vehicles. Technicians appreciate the straightforward installation process enabled by dimensionally perfect replication of factory specifications. This WG9761450120 component functions within a comprehensive ecosystem of drive axle elements, demonstrating consistent interoperability when replaced according to manufacturer recommendations. The standardization of this WG9761450120 part across multiple HOWO platforms simplifies inventory management for fleet operations.
Material Innovation
The metallurgical composition of the WG9761450120 roller represents significant advancement in drivetrain technology. Specialized alloy blending creates a component with optimal surface hardness while maintaining critical internal flexibility to absorb impact stresses. Production involves advanced case-hardening techniques that create a durable exterior surface resistant to pitting and abrasion. Engineers selected materials specifically to complement modern synthetic lubricants, preventing chemical degradation that could compromise drivetrain protection. Field testing of the WG9761450120 roller consistently confirms extended service life over alternative solutions.
Reliability Under Stress
Heavy-duty applications place extraordinary demands on transmission components, making the WG9761450120 roller’s reliability paramount. Design enhancements focused on distributing operational forces across broader contact surfaces dramatically reduce point loading that causes premature failure. The precisely calibrated WG9761450120 component maintains dimensional integrity even when subjected to continuous high-torque scenarios common in mountainous terrain and fully-loaded conditions. This engineering solution incorporates micro-surface texturing that retains lubricant more effectively than conventional designs, creating continuous protective film between contact surfaces. Operational data confirms WG9761450120 rollers perform exceptionally well across temperature extremes from Arctic conditions to desert environments.
Precision Manufacturing Process
Creating the WG9761450120 roller requires advanced manufacturing technology capable of micron-level accuracy. Automated production systems ensure each roller maintains dimensional tolerances within 0.005mm throughout high-volume output. Computer-controlled grinding equipment achieves surface finishes that minimize break-in periods while maximizing lubricant retention properties. Each WG9761450120-compatible batch undergoes comprehensive material certification verifying alloy composition and structural integrity before release. Production utilizes statistical process control methodologies that monitor critical parameters continuously throughout manufacturing cycles.
Drivetrain Synchronization Benefits
WG9761450120 rollers contribute significantly to powertrain harmony through precision-engineered rotational characteristics. Their balanced design reduces harmonic vibrations transmitted through the drive shaft, decreasing component fatigue throughout the transmission system. Implementation results in smoother shifting transitions and reduced shock loads during sudden acceleration events. The WG9761450120 roller serves as a critical interface between rotational and linear force vectors within the axle assembly. Proper installation dramatically reduces wear patterns observable on mating gear components, preserving overall drive-train alignment.
Long-Term Operational Economics
Beyond initial purchase considerations, WG9761450120 rollers deliver substantial economic advantages throughout their operational lifecycle. Extended replacement intervals significantly lower cumulative maintenance expenses compared to generic alternatives. The component’s predictable wear patterns allow for accurate service planning that minimizes unexpected vehicle downtime. Genuine WG9761450120 rollers prevent collateral damage to expensive adjacent components that often occurs when substandard parts fail prematurely. Fleet managers consistently report lower per-mile operating costs for vehicles maintained with authentic WG9761450120 drive components.
Environmental Compliance
Modern drivetrain components face increasingly stringent environmental requirements, making the WG9761450120 roller an exemplary solution. Its optimized geometry reduces rotational friction losses that directly contribute to lower emissions output. Production processes utilize environmentally controlled heat treatment facilities that minimize atmospheric impacts. The extended service life of each WG9761450120 roller decreases replacement frequency, significantly reducing resource consumption over typical vehicle service periods. Engineering teams developed surface treatments eliminating hazardous heavy metals historically associated with wear-resistant coatings.
Quality Validation Protocol
Each production batch of WG9761450120 rollers passes through multiple verification stages before distribution. Automated dimensional inspection systems conduct 100% verification of critical functional geometries against original equipment specifications. Surface integrity assessments using magnetic particle detection identify microscopic imperfections undetectable through visual examination. Performance validation occurs on specialized test rigs that simulate actual operating conditions at various load levels and temperatures. Final WG9761450120 roller certification requires passing all quality control metrics with sufficient operating margin beyond standard specifications.
Comprehensive Support Resources
Technical documentation accompanies every WG9761450120 roller shipment, providing detailed installation guidelines and recommended service protocols. Engineers developed specialized mounting procedures that ensure proper seating within the axle assembly to prevent uneven loading. Application specialists provide comprehensive specifications regarding compatible lubricants and appropriate fill levels for different operational environments. The global support network offers diagnostic assistance for technicians encountering unusual wear patterns in HG9761450120 roller applications. Implementation resources include digital reference materials accessible through web portals for real-time technical guidance.