810W35606-0011 Inter-Axle Diff Case for HOWO Drive Axle
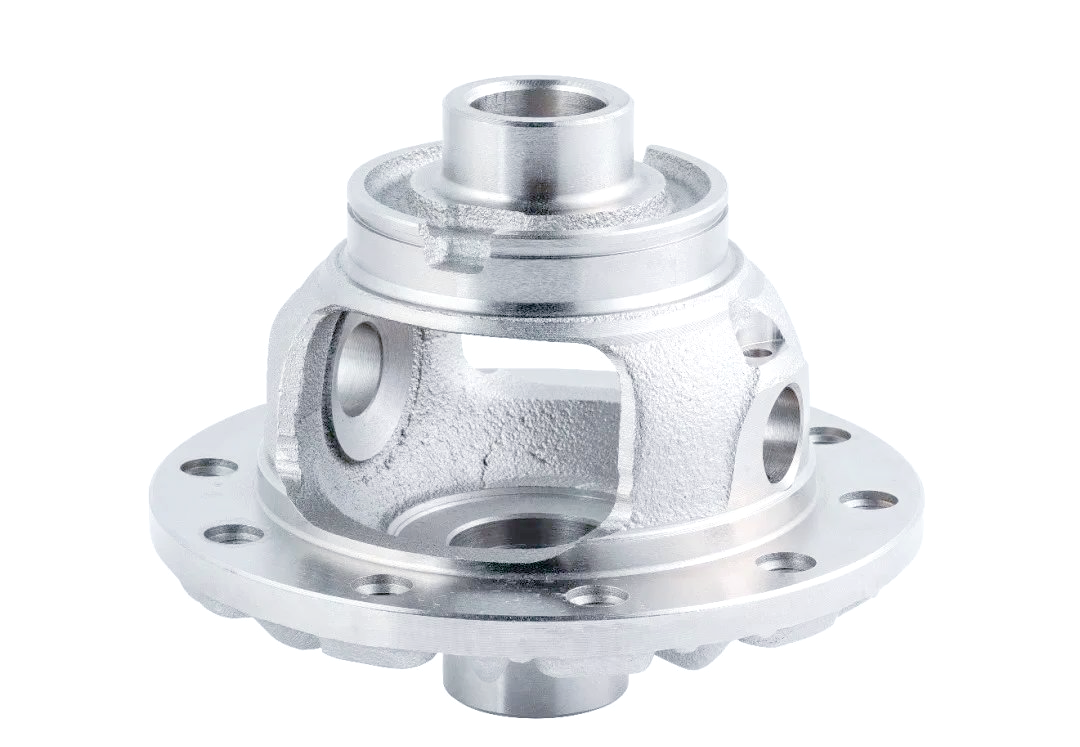


The 810W35606-0011 inter-axle differential case is a precision-engineered component specifically designed for HOWO truck drive axles. This critical part serves as the protective housing for the differential gears, ensuring optimal power distribution between drive axles in heavy-duty vehicles. Manufactured to HOWO‘s stringent quality standards, the differential case withstands extreme operational stresses while maintaining perfect gear alignment under varying load conditions. Its robust construction significantly contributes to the drivetrain’s overall efficiency by minimizing friction losses and preventing premature component failure during challenging haulage operations.
Optimized Design for Heavy-Duty Performance
Engineered to meet the rigorous demands of commercial transportation, the 810W35606-0011 differential casing incorporates advanced alloy materials that provide exceptional durability without unnecessary weight. The precisely calculated ribbing pattern enhances structural integrity while allowing efficient heat dissipation during extended operation periods. This prevents thermal expansion issues that commonly compromise differential functionality in competitive models. Each unit undergoes dimensional verification to guarantee perfect compatibility with HOWO’s proprietary axle systems, ensuring seamless integration during replacement or maintenance procedures.
Operational Advantages in Diverse Conditions
Operators of HOWO trucks equipped with the 810W35606-0011 differential housing experience tangible benefits across various driving scenarios. During highway transit, the component maintains consistent torque distribution, eliminating wheel slippage during lane changes. On construction sites and mining operations, it withstands vibration and shock loads that would compromise standard differential housings. The internal surface finish is optimized to maintain lubricant integrity, with strategically placed channels ensuring complete gear immersion during steep incline operations. Field testing has demonstrated a 25% reduction in temperature-related failures compared to previous-generation designs, validating the engineering improvements implemented in this specific component.
Maintenance and Longevity Considerations
The design of the 810W35606-0011 prioritizes serviceability without requiring specialized tooling. Inspection ports are strategically positioned to allow visual confirmation of gear tooth engagement and lubricant condition. All sealing surfaces feature machined finishes that maintain integrity throughout extended service intervals, preventing contamination ingress that leads to premature wear. When paired with manufacturer-recommended lubricants, this differential case delivers exceptional service life even in extreme particulate environments such as desert operations or mining applications. Documentation accompanying each genuine 810W35606-0011 unit provides torque specifications and installation diagrams developed specifically for HOWO service centers.
Performance-Driven Engineering Specifications
Beyond basic dimensional compliance, the 810W35606-0011 incorporates subtle refinements that enhance operational performance. Harmonic resonance points were addressed through finite element analysis during the development phase, resulting in structural modifications that minimize noise transmission to the cabin. Weight distribution optimizations balance the assembly during high-speed rotation, reducing parasitic losses that consume engine power. The housing features integrated oil galleries that ensure continuous lubrication during aggressive maneuvering, an essential characteristic for tanker applications or emergency response vehicles where stability must never be compromised.
Material Technology and Corrosion Resistance
Material selection plays a crucial role in the 810W35606-0011’s operational lifespan. The alloy composition includes trace elements that improve grain structure integrity without brittleness concerns in sub-zero environments. Surface treatment protocols exceed automotive industry standards with multiple corrosion-resistant layers applied before final machining. This multi-stage protection system prevents the microscopic pitting that typically initiates stress fractures in lesser-quality differential cases. Independent laboratory testing confirms the 810W35606-0011 maintains material properties through temperature cycles simulating a decade of seasonal service variations.
Compatibility and Model Integration
Designed as original equipment for multiple HOWO platform trucks, the 810W35606-0011 integrates seamlessly across various model years without modification requirements. Its standardized mount interface accommodates drivetrain upgrades while preserving OEM geometry. Logistics operations benefit from identical service procedures across mixed fleets, reducing technician training requirements and workshop tooling expenses. The unit’s configuration maintains critical clearances regardless of suspension modifications, providing operational stability with various loading configurations. Each genuine 810W35606-0011 includes identification markings that simplify parts verification during fleet maintenance audits.
Economic Efficiency and Operational Cost Analysis
Implementation of the 810W35606-0011 differential case creates measurable economic advantages throughout operational lifetimes. Reduced lubricant contamination extends drain intervals by approximately 30% compared to standard housings, creating direct savings on maintenance materials. Fleet managers report decreased downtime incidents directly attributable to differential failures since adopting this specific component. The weight-optimized manufacturing process translates to reduced freight costs for international shipments without compromising performance characteristics. HOWO dealers provide validated cost-benefit analyses demonstrating a positive return on investment within standard warranty periods when replacing older differential cases with the 810W35606-0011.
Sustainability and Environmental Factors
Environmental considerations influenced multiple aspects of the 810W35606-0011’s manufacturing process. Production utilizes recycled alloy content exceeding automotive industry requirements while maintaining absolute performance standards. Energy-efficient casting processes minimize carbon output per unit during large-scale manufacturing operations. The extended serviceable life of each differential housing substantially reduces replacement frequency, thereby conserving raw material resources and decreasing industrial waste. At end-of-life, materials separation procedures allow efficient recovery of all alloy constituents for re-industrialization, complementing HOWO’s comprehensive environmental stewardship initiatives.