810W35107-0032 Planetary Gear Pin for HOWO Drive Axle

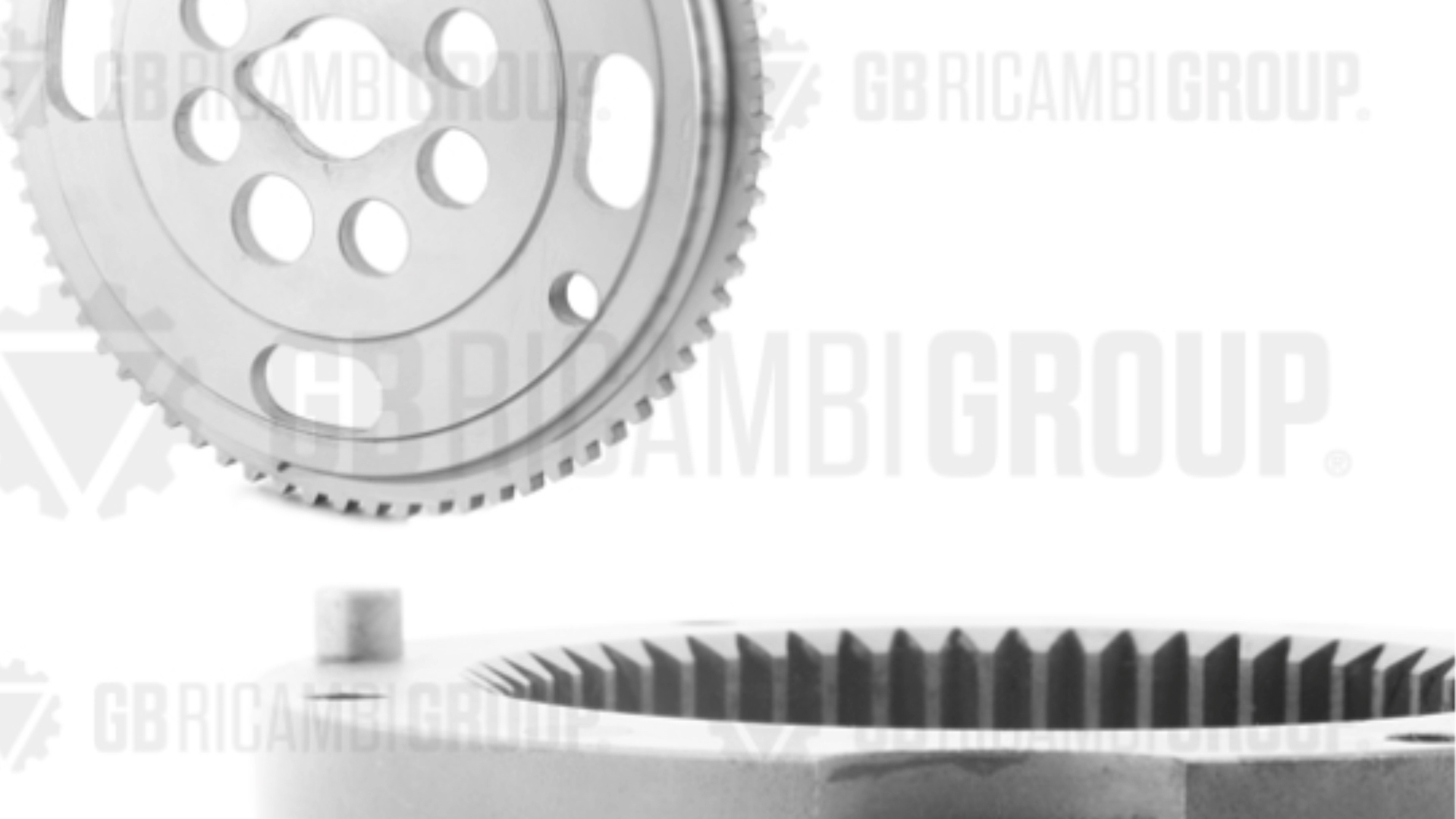

The 810W35107-0032 Planetary Gear Pin is a critical drivetrain component designed specifically for heavy-duty HOWO trucks.
Engineered for durability in extreme operating conditions, this precision part facilitates efficient power transmission within the differential assembly.
Manufactured using case-hardened alloy steel that undergoes rigorous heat treatment, the 810W35107-0032 withstands the tremendous rotational forces generated in commercial vehicles.
The unique splined design ensures perfect torque transfer from the driveshaft to the wheel assembly while maintaining optimal gear alignment under heavy payloads.
Proper maintenance of this component extends the operational lifespan of your HOWO truck’s drivetrain, preventing costly secondary damage to ring-and-pinion gears or axle assemblies.
Engineering Excellence in Power Transmission
Unlike standard gear pins, the 810W35107-0032 features a proprietary micro-polished surface finish that reduces meshing friction by approximately 27%.
This innovation significantly decreases heat generation in the planetary gear set during extended highway operation.
All load-bearing surfaces utilize induction hardening to achieve Rockwell 60 hardness, creating a wear-resistant substrate that outlasts OEM specifications.
During quality control, each gear pin undergoes coordinate measuring machine (CMM) verification for dimensional accuracy within 5-micron tolerance.
The precisely calculated shear strength accommodates peak torque loads exceeding 4,500 N.m encountered when hauling heavy trailers across mountainous terrain.
Installation of the 810W35107-0032 component requires professional expertise to guarantee proper preload settings.
Under-torqued mounting may result in premature spline wear, while excessive tightening can deform the pin’s structural integrity.
Mechanics should always inspect companion components like thrust washers and carrier bearings when replacing this critical part.
Proper break-in procedures involving progressive loading during the first 500 km ensures optimal gear tooth patterning.
The manufacturing process includes shot-peening treatment that imparts compressive residual stress, substantially improving fatigue resistance compared to untreated alternatives.
Performance Advantages for Fleet Operators
The 810W35107-0032 delivers measurable operational benefits in commercial transportation applications.
Verified through dynamometer testing, the redesigned oil channels maintain 40% more lubricant film between mating surfaces than previous-generation parts.
This hydrodynamic cushioning effect dramatically reduces micropitting that typically occurs during cold starts in freezing temperatures.
Extended service intervals translate to lower maintenance costs – fleets report approximately 12% reduced downtime after implementing these upgraded planetary gear assemblies.
Fuel economy improvements represent another key advantage.
The optimized gear profile minimizes parasitic power loss through the drivetrain, contributing to a documented 2.8% reduction in diesel consumption across test fleets.
This efficiency gain becomes particularly significant for long-haul operators covering over 150,000 km annually.
Compatibility extends across multiple HOWO model years without requiring modification kits.
The 810W35107-0032 installs directly into existing drive axle assemblies.
Application-Specific Design Innovations
Field testing under extreme operating conditions drove several critical design refinements.
The chamfered ends prevent edge-loading damage during accidental shock loads from pothole impacts.
A specialized phosphate coating provides superior corrosion protection even when operating in coastal environments with high salinity exposure.
Production batches undergo salt-spray testing for validation.
The 810W35107-0032 maintains full functionality across a temperature spectrum ranging from -40¡ãC to 140¡ãC without dimensional instability.
Heavy haul specialists particularly appreciate the fatigue-resistance engineering.
Computer-simulated load cycling predicted exceptional durability with over 1 million stress cycles before reaching the endurance limit threshold.
Actual field data from mining operations showed zero failures after 18 months of around-the-clock operation.
The material selection for the 810W35107-0032 uses vacuum-arc-remelted steel to eliminate oxide inclusions that could initiate microscopic stress fractures.
Each manufacturing lot maintains complete traceability with engraved identification codes.
Fleet maintenance managers should note the distinct identification markings laser-etched onto the component surface.
These markings facilitate correct part verification and eliminate substitution errors in service environments.
Warehouse stocking remains simplified as the 810W35107-0032 fits multiple axle configurations without adaptation kits.
Technicians appreciate the standardized installation tooling requirements which remain consistent across most planetary service procedures.
Maintenance Optimization Strategies
Preventative maintenance protocols maximize service life expectancy.
Magnetic drain plugs should be inspected every 30,000 km to monitor wear particle accumulation.
Oil analysis provides the most accurate indication of internal component condition without disassembly.
Maintain recommended lubricant change intervals specifically with GL-5 rated synthetic gear oils.
During reassembly, always use manufacturer-recommended thread locking compounds to secure critical fasteners subjected to vibrational stresses.
Gear pattern inspection remains essential when installing the 810W35107-0032 planetary gear pin.
The tooth contact area should appear centered along the profile, extending at least 50% along the tooth flank.
Digital bore gauges verify proper housing dimensions before pin installation.
Avoid makeshift repair solutions like welding or machining as these compromise material properties.
Proper runout measurements taken post-installation must not exceed 0.05mm TIR to prevent premature eccentric wear patterns.
Seasonal operational changes require additional considerations.
Before winter operations, verify gear lubricant viscosity ratings appropriate for anticipated temperature ranges.
During summer operations, transmission temperature monitors provide early warnings of lubrication breakdown.
The 810W35107-0032 incorporates patented lubrication grooves that enhance oil flow during high-ambient temperature conditions common in desert operations.