WG2214220007/1 Positioning Fork for HOWO Truck Transmission
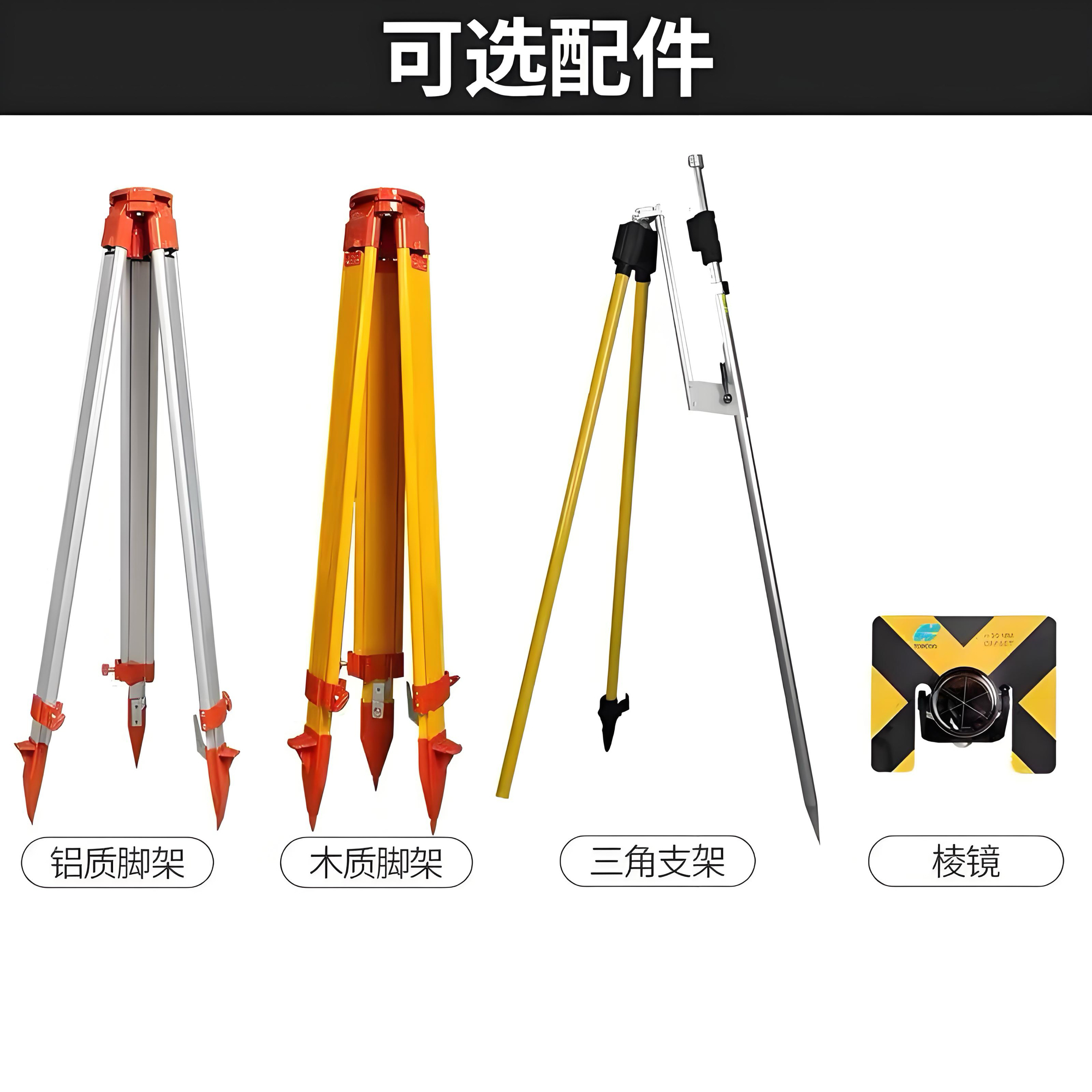

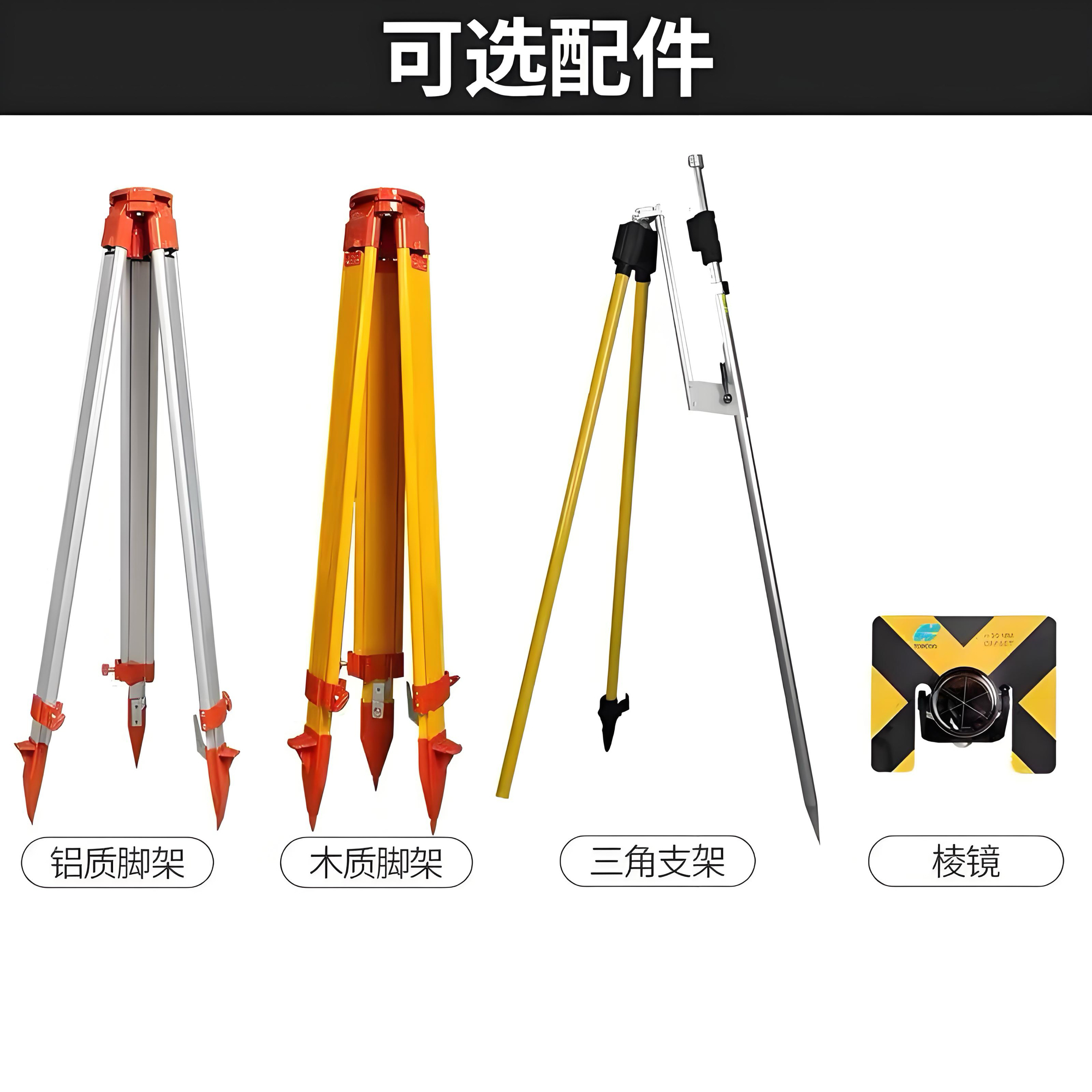
The WG2214220007/1 Positioning Fork is a precision-engineered component essential for optimal performance in HOWO heavy-duty trucks. This critical transmission part ensures accurate gear engagement by smoothly transitioning gear collars during shifting sequences. Manufactured to exact OEM specifications, the positioning fork provides reliability under the most demanding operating conditions. When properly maintained, it significantly extends transmission lifespan while minimizing costly downtime for fleet operators and individual truck owners alike.
Developed exclusively for HOWO transmission systems, this specialized component withstands the extreme torque requirements found in commercial haulage applications. The fork’s robust construction features reinforced pivot points that resist deformation during high-stress shifting maneuvers. By maintaining precise alignment within the gearbox assembly, the WG2214220007/1 Positioning Fork prevents premature gear wear and eliminates the grinding noises associated with misalignment issues. Truck technicians particularly appreciate the installation-ready design that requires no modification or special tools for proper fitting.
Durability Engineering
Every Positioning Fork (OEM: WG2214220007/1) undergoes rigorous quality validation to exceed industry durability benchmarks. The precision-forged alloy steel core receives specialized heat treatment to achieve the ideal balance between impact resistance and operational flexibility. Protective coatings minimize corrosion while reducing friction coefficients at critical contact points. These engineering decisions translate directly to fewer transmission rebuilds and extended maintenance intervals for truck operators, resulting in significant operational cost savings over the vehicle’s service life.
Performance Impact
The significance of the Positioning Fork in the WG2214220007/1 specification cannot be overstated for drivetrain efficiency. Optimally functioning forks facilitate seamless gear transitions, eliminating the power interruption that occurs during clumsy shifts. This translates to improved fuel economy through reduced power loss during gear changes. For drivers, the immediate benefit is a smoother driving experience without jerking or hesitation during acceleration sequences. Fleet managers particularly value this component’s role in minimizing transmission-related roadside breakdowns that disrupt delivery schedules.
Precision Manufacturing
Specialized CNC machining ensures each WG2214220007/1 Positioning Fork meets exact dimensional tolerances within 0.02mm precision. This manufacturing precision guarantees perfect alignment with gearbox synchronizers and slider assemblies. The complex contouring on the fork arms provides ideal leverage points while precisely contoured contact surfaces ensure maximum surface contact during gear engagement. These details, though invisible to the naked eye, create tangible performance differences in daily truck operations.
Compatibility Information
This WG2214220007/1 Positioning Fork is designed specifically for HOWO heavy-duty truck transmissions between model years 2015-2023. Exact compatibility covers dual-clutch and synchronized gearbox configurations across the HOWO T7, HOWO T5G, and HOWO A7 model ranges. Installation requires no modifications, providing plug-and-play replacement for worn components. Available through authorized parts distributors, this genuine positioning fork maintains full warranty coverage when installed by certified technicians.
Maintenance Advantages
The WG2214220007/1 Positioning Fork features engineered wear indicators that simplify maintenance planning. Visual inspection points allow technicians to assess component condition during routine fluid changes without full transmission disassembly. Design enhancements around pivot bushings significantly reduce lubrication requirements compared to earlier fork designs. These maintenance-friendly features reduce workshop time during service intervals, getting trucks back in service faster while lowering overall maintenance costs.
Reliability Factors
Extreme environment testing validates the WG2214220007/1’s performance across temperature ranges from -40¡ãC to +150¡ãC. The specialized metal alloy maintains structural integrity despite constant exposure to transmission fluid additives that degrade lesser materials. Fatigue testing demonstrates a minimum service life of 500,000 kilometers under normal operating conditions. These reliability metrics translate to fewer component replacements, minimized vehicle downtime, and predictable maintenance budgeting for transportation companies.
Operational Benefits
Implementing the WG2214220007/1 Positioning Fork yields measurable operational improvements. Reduced shift effort decreases driver fatigue during demanding routes. Power transfer efficiency improvements contribute to 1-3% better fuel economy in real-world applications. Most significantly, proper gear engagement prevents collateral damage to synchronizer rings and gear teeth, preventing cascade failures that lead to catastrophic transmission damage. These benefits directly impact fleet profitability through reduced fuel consumption and lower repair expenses.
Technical Specifications
Manufactured from SAE 4140 chromoly steel, the WG2214220007/1 fork maintains dimensional stability throughout its service life. Standard weight measures 1.8kg with balanced weight distribution ensuring vibration-free operation up to 4,500 RPM. Critical dimensions include pivot-to-tine distance of 162¡À0.05mm with contact surfaces hardened to 55-60 HRC for optimal wear resistance. Comprehensive testing validates shear strength exceeding 28 kN/mm2, substantially surpassing operational requirements in heavy-duty transmissions.
Supply Chain Assurance
Authentic WG2214220007/1 Positioning Forks feature traceable manufacturing documentation, including material certifications and production batch tracking. Each component ships with anti-counterfeiting verification to guarantee genuine quality. Standard packaging includes corrosion-inhibiting vapor barriers that maintain component integrity during extended storage periods. These supply chain measures give purchasing managers confidence in part authenticity and quality consistency when ordering replacements for their fleets.