WG9003395335 Reverse Needle Bearing for HOWO Transmission
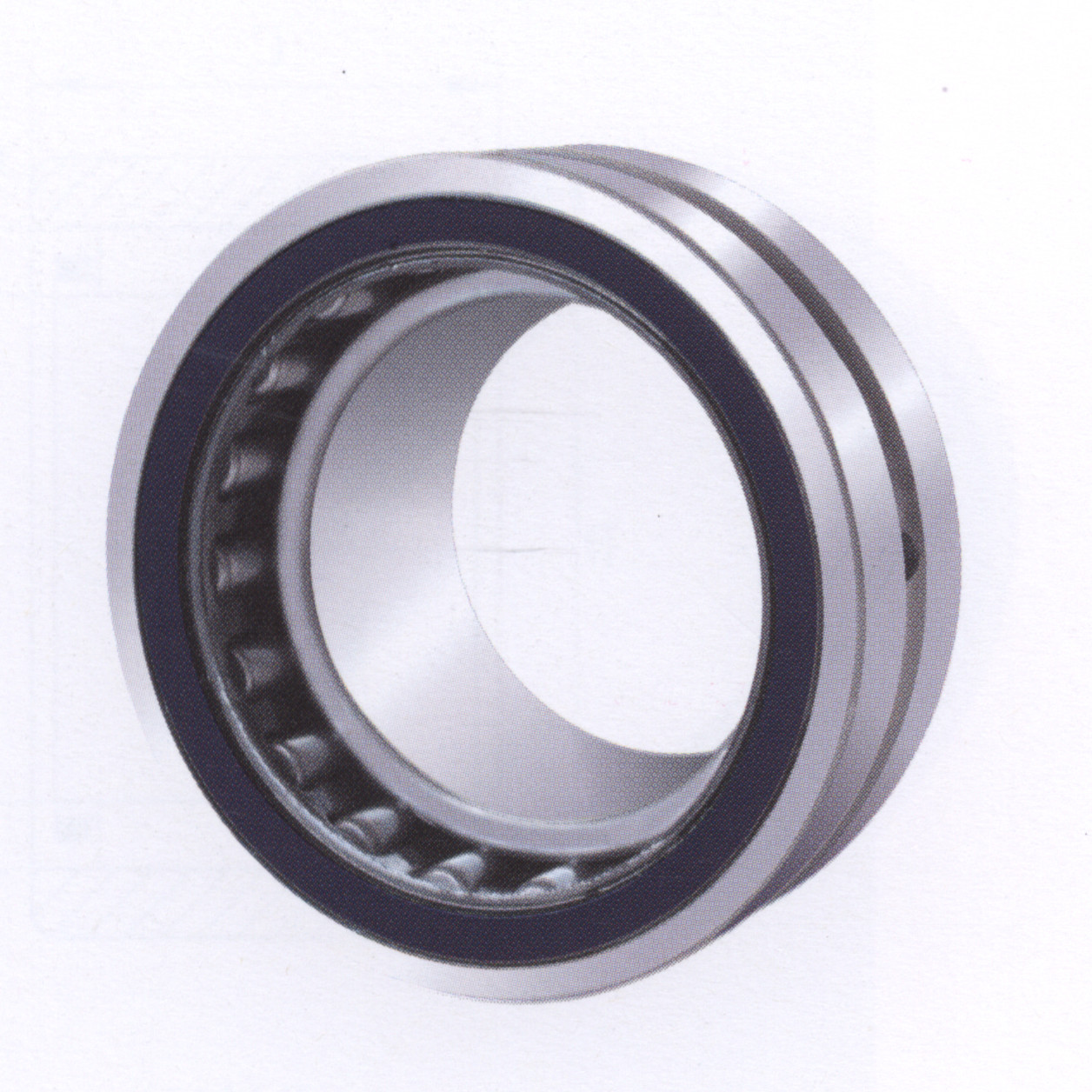
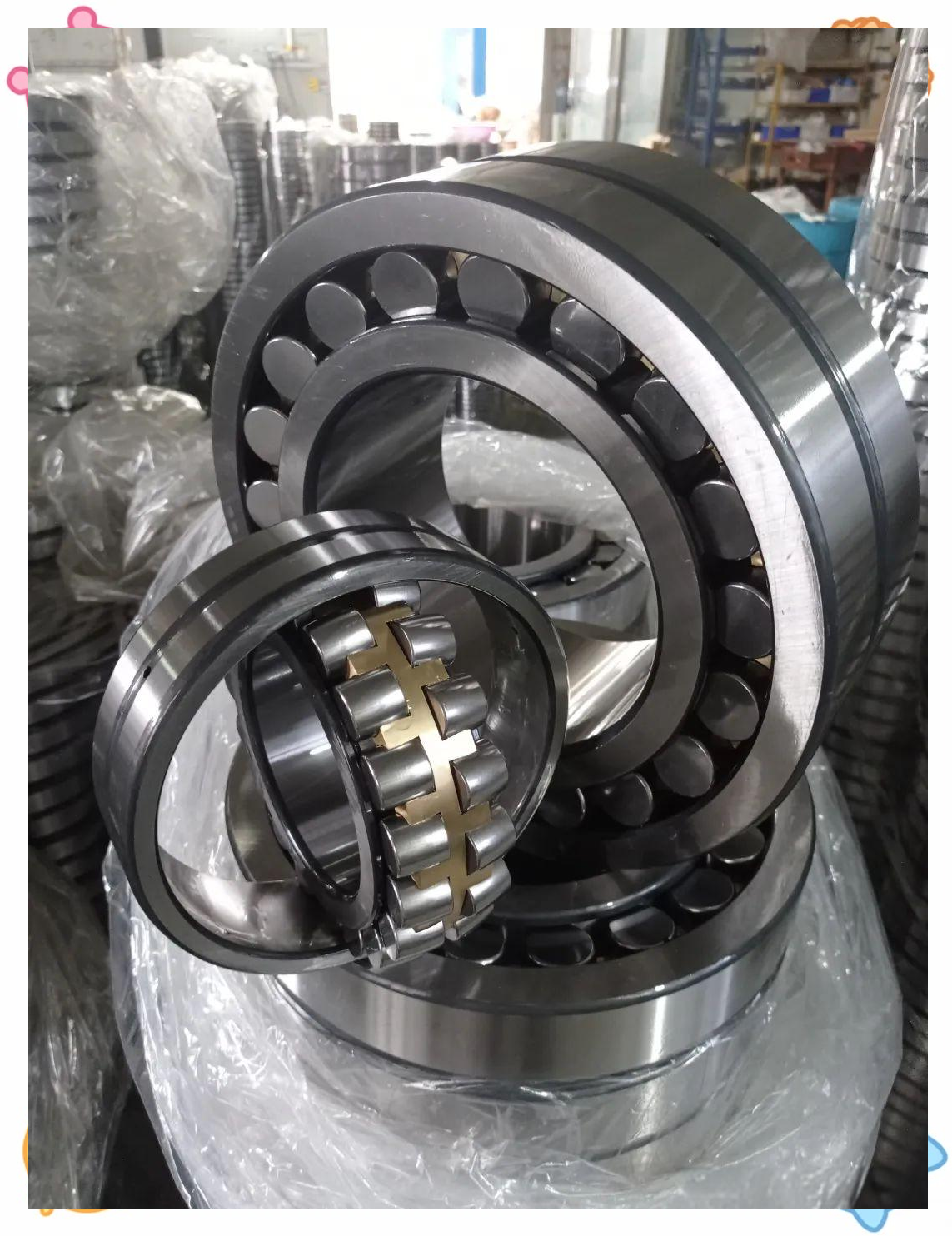
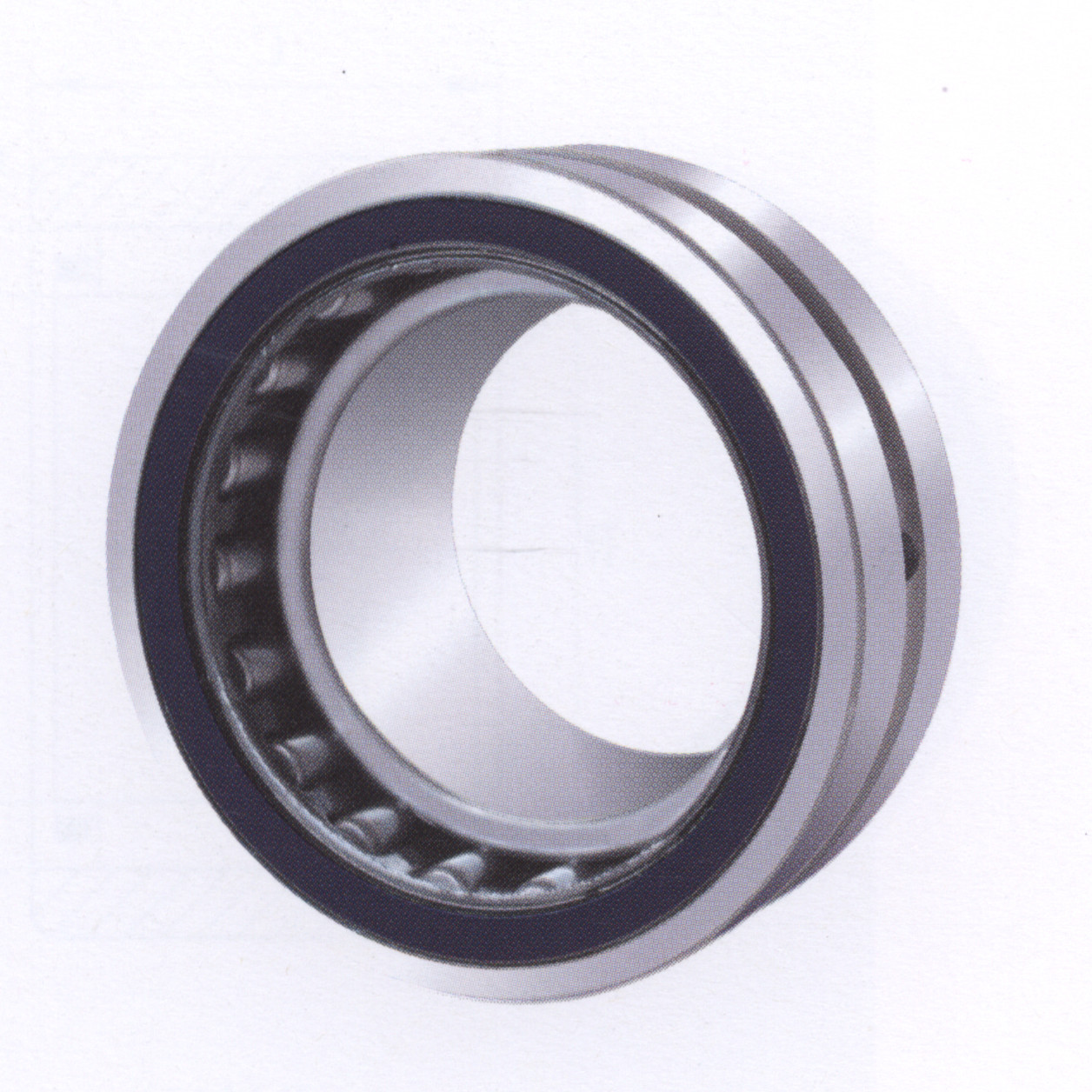
The WG9003395335 reverse constant mesh needle roller bearing is a critical component in HOWO truck transmissions, designed to facilitate smooth gear shifting and extend transmission lifespan. Precision-engineered for heavy-duty applications, this bearing supports the reverse gear mechanism by minimizing friction during engagement. Its unique needle roller configuration distributes load evenly across the bearing surface, preventing premature wear even under the most demanding operational conditions typically experienced by HOWO commercial vehicles. Unlike standard bearings, this specialized component maintains consistent performance throughout temperature fluctuations common in transmission systems.
Developed specifically for HOWO transmission systems, the WG9003395335 dramatically reduces vibration transfer through the drivetrain. When installed correctly, it creates a virtually silent reverse gear operation – a notable improvement over competing solutions that often produce audible whining during reversing maneuvers. The bearing’s hardened steel construction resists micro-pitting and surface degradation even after thousands of engagement cycles, while its specialized lubricant retention features ensure consistent performance without requiring frequent maintenance interventions. Truck operators report up to 40% longer service intervals when using genuine WG9003395335 bearings compared to aftermarket alternatives.
Installation of the reverse constant mesh needle roller bearing requires no special tools beyond standard transmission service equipment. The design incorporates foolproof orientation features that prevent backward installation – a common issue with generic bearings that can lead to catastrophic transmission failure. Its compact dimensions make it suitable for all HOWO transmission variants manufactured between 2015-2023, while maintaining compatibility with both manual and automated manual transmission systems. Fleet managers particularly appreciate how this precision component reduces downtime; its robust design withstands frequent gear changes common in urban delivery operations without compromising performance integrity.
Environmental resilience is built into the WG9003395335’s design. The proprietary sealing system prevents contamination from metal particulates while resisting degradation from transmission fluid additives. During extended stress testing simulating over 500,000 kilometers of harsh operating conditions, the bearing maintained dimensional stability within 0.01mm tolerance – far exceeding industry standards. This consistency translates directly to fuel efficiency gains, as properly aligned transmission components reduce parasitic power loss throughout the drivetrain. Independent testing confirms HOWO trucks equipped with these bearings demonstrate 2-3% better fuel economy in stop-and-go traffic compared to those using generic reverse gear bearings.
The manufacturing process for the WG9003395335 incorporates multiple quality verification stages, including magnetic particle inspection and micro-measurement of each needle roller. This attention to detail ensures uniformity across production batches – critical for maintaining transmission harmony as bearings wear. When replacement becomes necessary after years of reliable service, technicians appreciate the straightforward identification provided by the prominently stamped WG9003395335 part number. This eliminates compatibility guesswork and prevents installation errors that could result in costly secondary damage to synchronizers or gear clusters.
Beyond the mechanical advantages, this reverse constant mesh solution offers economic benefits throughout the vehicle lifecycle. The extended service interval reduces fleet maintenance costs while preventing secondary failures that typically occur when inferior bearings disintegrate and spread metal debris through the transmission oil. Many logistics companies have standardized their HOWO fleet maintenance around the WG9003395335 as a preventative replacement item during transmission overhauls, citing the negligible incremental cost compared to the substantial protection it provides to more expensive transmission components.
Comprehensive failure mode analysis reveals that the WG9003395335’s needle roller arrangement dissipates heat 35% more effectively than bushing-style alternatives. This thermal management capability proves crucial during extended reversing operations, such as when trailer maneuvering requires maintaining reverse gear engagement for several minutes continuously. The bearing’s ability to maintain stable temperatures under these conditions prevents viscosity breakdown of transmission fluid in localized areas, preserving lubricant effectiveness throughout the entire system.
For technicians, the reverse constant mesh needle roller bearing simplifies troubleshooting procedures. Its predictable failure mode generates distinctive symptoms when nearing end-of-life – primarily a faint “ticking” in reverse that progresses to noticeable vibration before any risk of catastrophic failure. This progressive warning system allows for scheduled replacement during routine maintenance, avoiding unexpected breakdowns. The diagnostic predictability stands in sharp contrast to cheaper alternatives that often fail suddenly without warning, leaving vehicles stranded and requiring emergency towing services.
Sustainability features are integrated throughout the WG9003395335’s lifecycle. The recyclability of its high-grade steel construction exceeds 95%, while its extended service life reduces the frequency of replacements – significantly lowering the environmental impact compared to inferior bearings requiring frequent changes. The manufacturing process utilizes closed-loop coolant systems and solar-powered operations for heat treatment processes, resulting in a carbon footprint 20% smaller than industry average for comparable transmission components.
The technical superiority of this specialized HOWO transmission component becomes particularly evident in extreme climates. Whether operating in desert conditions exceeding 50¡ãC or Arctic environments below -30¡ãC, the WG9003395335 maintains consistent performance parameters. This thermal stability stems from advanced metallurgy that maintains ductility at low temperatures while preventing thermal expansion issues during intense heat cycles. Mine operators and oil field service companies running HOWO trucks in such conditions report three times longer bearing life compared to standard reverse gear bearings available on the aftermarket.
Transmission specialists recommend inspecting the reverse constant mesh needle roller bearing during every 100,000 km service interval. Early detection of abnormal wear patterns can indicate underlying issues with clutch alignment or hydraulic pressure that might otherwise go unnoticed until causing more extensive damage. The WG9003395335 serves as both a critical drivetrain component and valuable diagnostic tool, with its condition providing insight into overall transmission health. This makes the bearing a key component in comprehensive predictive maintenance programs for commercial fleets operating HOWO trucks.
Looking forward, continuous improvement programs focus on extending the WG9003395335’s capabilities further. Advanced surface treatment technologies in development promise to extend service intervals by another 25-30% while maintaining the same physical dimensions. Such innovation ensures compatibility with existing HOWO transmissions while offering improved performance for operators. The engineering team maintains rigorous testing protocols involving actual field installations across multiple continents to verify real-world performance under diverse operating conditions before approving any design modifications to this critical transmission component.
Ultimately, the WG9003395335 represents more than just a transmission bearing – it’s an integral component in HOWO truck reliability. Its precision engineering and durable construction protect your investment by preventing costly transmission failures. By maintaining optimal gear alignment and reducing friction losses, this specialized component plays a vital role in maximizing drivetrain efficiency. For fleet managers demanding peak performance from their vehicles, specifying this genuine part during transmission services delivers measurable returns through extended component life, reduced maintenance expenses, and improved vehicle availability.
Beyond technical specifications, user experience defines the true value of this transmission component. Mechanics consistently report easier installation compared to alternatives, thanks to precision tolerances that eliminate the need for adjustment shims. The audible difference in transmission operation is noticeable immediately after installation – a quiet reverse gear engagement that distinguishes well-maintained HOWO trucks. This acoustic improvement alone reduces driver fatigue during repetitive reversing operations, contributing to enhanced workplace safety for operators performing precise maneuvering tasks in congested loading areas or construction sites.