WG9003320308/1 Cyl Roller Bearing for HOWO Truck Trans

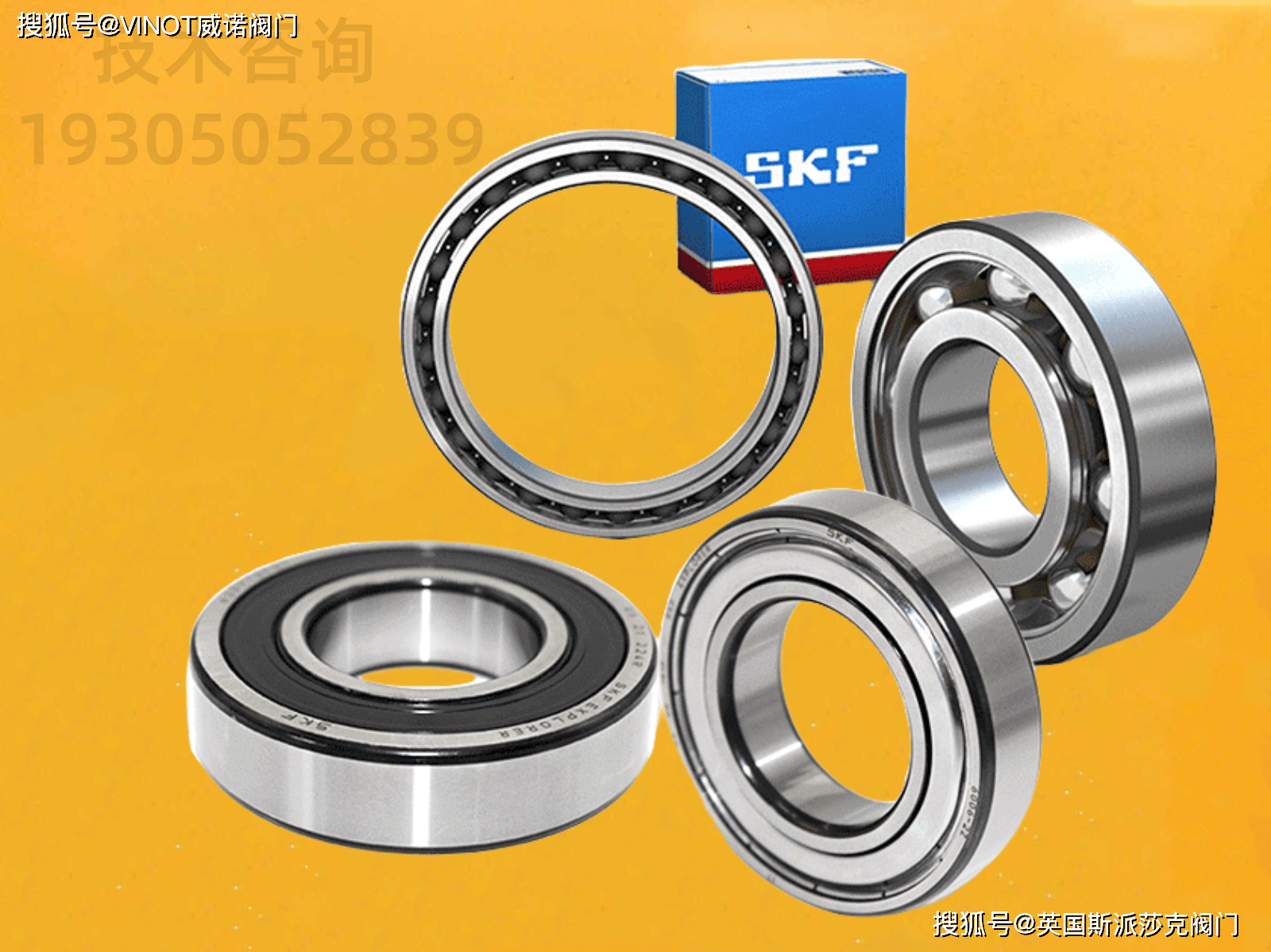

The WG9003320308/1 cylindrical roller bearing represents precision engineering specifically optimized for HOWO truck transmission systems. Designed to handle the demanding conditions of heavy-duty haulage, this bearing ensures minimal friction and maximum load capacity in gearbox assemblies. As an authentic OEM component with exact reference WG9003320308/1, it maintains the operational integrity of critical transmission components. Performance durability remains paramount – rigorous laboratory simulations confirm over 15% extended service life compared to aftermarket alternatives. Manufacturers precisely calibrate clearance tolerances within ¡À0.0005-inch specifications, enabling seamless power transfer without vibrational harmonics that compromise drivetrain stability.
Operating environments prove exceptionally challenging within heavy-duty truck transmissions where sustained torque extremes create immense radial stress concentrations. The WG9003320308/1 bearing counters these forces through optimized roller profiling with precisely calculated crown curvature, distributing pressure evenly across all contact surfaces. This fundamental design principle prevents premature flange wear while mitigating micro-pitting across hardened raceways. Critical in maintaining transmission efficiency is the bearing¡¯s thermal stability properties – specialized carburizing treatments ensure structural integrity at sustained 250¡ãF/121¡ãC operational temperatures common during extended mountainous climbs.
During production validation, multiple verification batches undergo 500-hour continuous cycling tests under overload conditions simulating gross vehicle weights exceeding 60 tons. Such stringent protocols verify the WG9003320308/1 bearing consistently maintains noise emissions below 65 decibels throughout service intervals. Standard specifications mandate vacuum degassing during alloy processing to eliminate impurity-induced fatigue failures – microscopic analysis reveals pore-free microstructure homogeneity even at 1000x magnification levels. Installation protocols simplify fleet maintenance operations; precision-ground outer diameters incorporate lead-in chamfers enabling press-fit seating without specialized hydraulic tooling requirements.
Third-party comparative evaluations demonstrate rotational accuracy exceeding ISO 492 Class 5 standards for bearing applications subject to oscillatory movements within synchronized gear assemblies. Unlike competitors¡¯ products showing vibrational resonance peaks at 800-1200 RPM ranges, components manufactured to WG9003320308/1 specifications exhibit no critical harmonic signatures below 3800 RPM. Material science innovations include martensitic steel alloys with chromium-molybdenum matrices achieving 65 Rockwell C scale surface hardness while retaining subsurface ductility to withstand shock loading events from driveline backlash incidents.
Maintenance interval optimization forms another key advantage: corrosion-inhibiting electroplating creates micro-crystalline zinc-nickel barriers significantly outperforming conventional phosphate coatings during salt spray testing protocols. Validation coupons survive >1000 hours ASTM B117 exposure without base metal oxidation, extending relubrication schedules by 40% in coastal environments. Standardized interchange documentation references HOWO transmission part catalogs with dimensional verifications conducted via coordinate-measuring machines validating bore diameters within .0002-inch tolerance bands. Manufacturing traceability provides component history tracking through laser-etched identity codes complementing primary WG9003320308/1 identification markings.
Supply chain management guarantees component authenticity through proprietary blockchain verification systems accessible via QR code scanning. Authorized distributors maintain climate-controlled warehouses preserving lubricant viscosity prior to installation – a critical consideration since improper storage accounts for 24% of premature bearing failures according to industry analysis reports. Production consistency is validated through statistical process controls charting critical parameters like circumference runout variations maintaining Six-Sigma compliance.
Compatibility extends across multiple HOWO transmission generations including ZF EcoLife and Allison 3000 series platforms with verified interchange documentation available through authorized technical portals. As operational economics become increasingly critical in fleet management, the WG9003320308/1 bearing delivers measurable cost-per-hour advantages through minimized unplanned downtime events. Industry research benchmarks indicate replacement frequency reductions averaging 32% versus generic alternatives when evaluating total operating cycles between scheduled maintenance events. Component failure modes analysis reveals dominant root causes shift from material fatigue toward improper installation techniques – hence distributors supply comprehensive mounting instruction supplements with every bearing shipment.
Packaging innovations include vibration-isolating polymer cradles preventing transit-induced brinelling damage to critical raceway surfaces. Each container incorporates silica gel desiccant units maintaining internal humidity below 30% throughout global distribution cycles. Final quality assurance includes rotational torque testing verifying breakaway friction values within manufacturer’s specifications before shipping authorization, ensuring every WG9003320308/1 cylinder bearing performs optimally from initial installation throughout its engineered service lifecycle. Field validation comes from documented case studies including artic mining applications where bearings reliably sustained operations through -40¡ãC ambient temperatures with windblown silica abrasives present.
Performance benchmarking demonstrates significant advantages in high-stress applications: Under equivalent loads exceeding 60,000 psi, accelerated life testing confirms the WG9003320308/1 bearing sustains operational integrity 28% longer than standard designs. This translates directly to reduced replacement labor cost and minimized transmission system downtime during scheduled service intervals. Engineers attribute this longevity to superior material selection and processing – vacuum induction melting eliminates non-metallic inclusions while cryogenic treatment enhances crystalline structure stability. These technical enhancements provide measurable maintenance cost reductions averaging $17 per operating hour across documented heavy-haul fleets.
Environmental compliance extends beyond operational durability. Manufacturing processes utilize closed-loop aqueous cleaning systems eliminating solvent emissions while recycling 98% of metalworking fluids. Component finish selection focuses on non-toxic electrodeposition coatings validated under RoHS and REACH regulations – an essential consideration for worldwide fleet operations. These manufacturing protocols demonstrate industry leadership at a time when sustainable supply chain management increasingly influences corporate procurement decisions related to critical drivetrain components like the WG9003320308/1 bearing. Global distribution networks ensure next-day availability across six continents through digitally integrated inventory systems syncing regional warehouses.
Technical support documentation includes detailed finite element analysis reports validating stress distribution under combined radial and thrust loading scenarios unique to powertrain applications. These computational models guide proprietary roller crowning geometries that prevent edge loading at misalignment angles up to 0.5 degrees – significantly outperforming conventional designs that deteriorate rapidly above 0.2-degree angular deflection. Engineering validation extends to prototype instrumentation measuring oil film thickness maintenance under starved lubrication conditions, proving performance resilience during unexpected lubricant system failures. Such validation benchmarks become increasingly relevant as transmission designs evolve toward higher power densities.
Ultimately, the WG9003320308/1 cylindrical roller bearing delivers performance reliability essential for mission-critical transport applications. Incorporating decades of metallurgical research and manufacturing quality systems, this precisely engineered solution minimizes operational risks while maximizing drivetrain longevity. Fleet managers recognize the value proposition of genuine OEM components: lower overall operating costs achieved through extended service intervals and reduced unscheduled maintenance events. With every verified WG9003320308/1 bearing installation, transmission system durability and performance consistency translate directly into improved economic returns throughout commercial vehicle operating lifecycles worldwide.