HOWO Truck Cabin Evaporator Frame 712W61942-0065/1
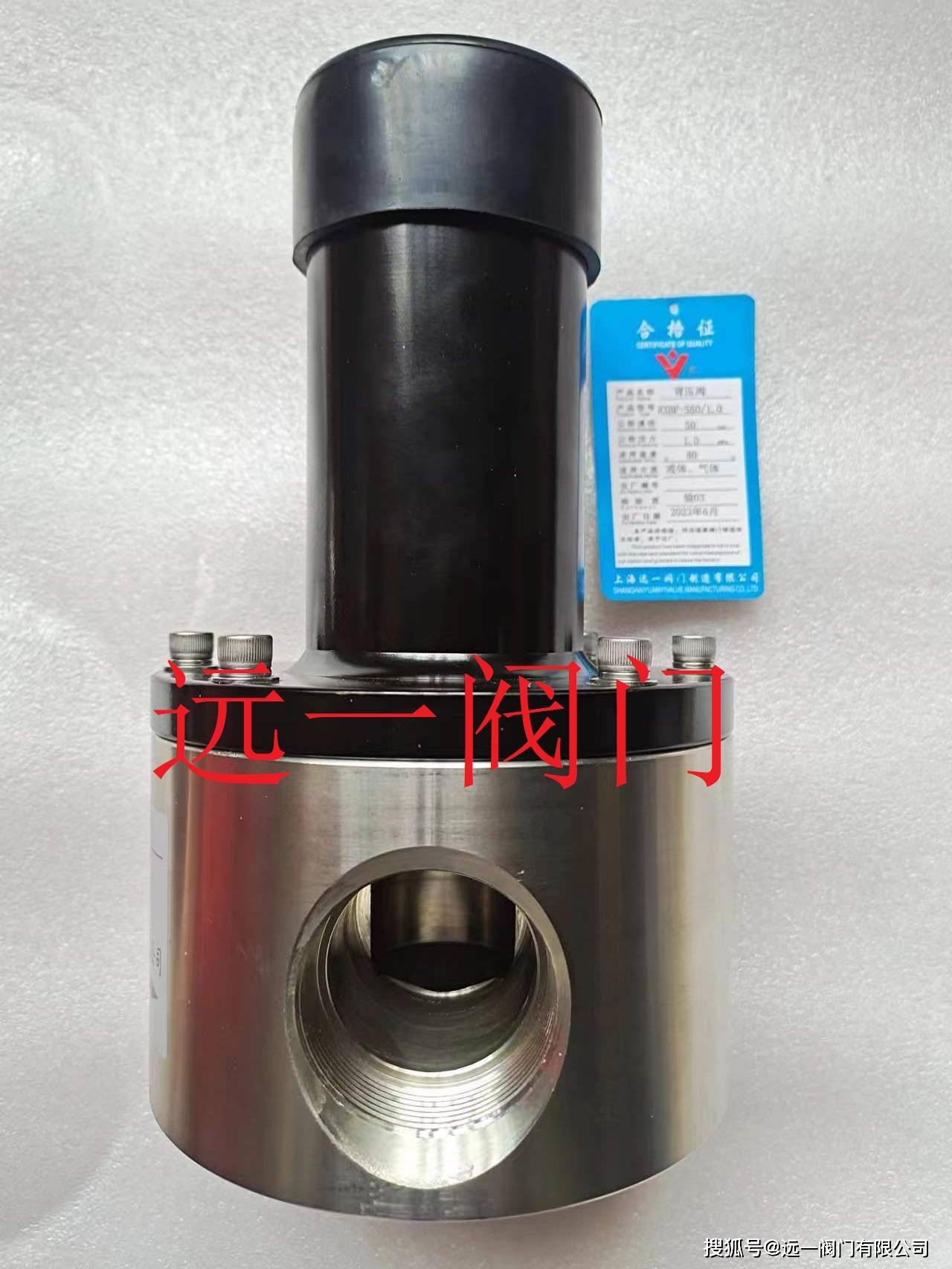
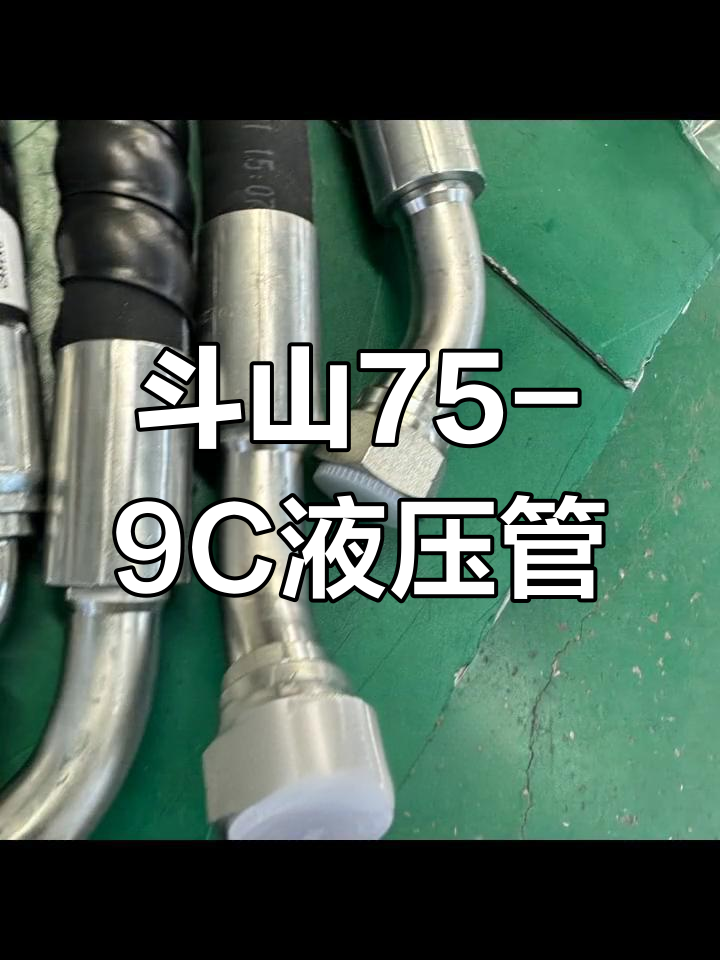

Designed specifically for HOWO heavy-duty trucks, the Evaporator Line Frame Section 712W61942-0065/1 represents an essential cabin component engineered for optimal climate control system performance. This precision-crafted part functions as the structural backbone for the evaporator unit within the HVAC system, ensuring secure positioning and proper airflow distribution throughout the operator cabin. When installing the 712W61942-0065/1 component, technicians note its seamless compatibility with existing mounting points and fluid line connections. Regular inspection of this frame section during seasonal maintenance checks helps identify potential wear points before they compromise cooling efficiency.
The engineering behind the 712W61942-0065/1 involves advanced alloy compositions that resist corrosion while maintaining structural integrity under constant vibration conditions encountered in long-haul trucking operations. Unlike generic alternatives, this OEM-certified part undergoes rigorous quality validation to match original performance specifications. Fleet managers choose the authentic 712W61942-0065/1 assembly not only for reliability but for its direct impact on driver comfort during extreme weather conditions. The component’s design incorporates drainage channels that prevent moisture accumulation, a critical feature often overlooked in aftermarket solutions that can lead to microbial growth in climate systems. Installation requires no specialized tools beyond standard workshop equipment, though referencing vehicle-specific service manuals ensures correct torque settings are applied to all fastener points. Each batch of 712W61942-0065/1 units receives laser-etched identification markers for traceability throughout the supply chain, providing assurance against counterfeit parts infiltrating maintenance inventories. This frame section also features pre-drilled service access ports that simplify future evaporator coil cleaning procedures without requiring disassembly. When ordering the 712W61942-0065/1, verify model-year compatibility since slight dimensional variations exist between truck generations despite sharing the core part designation.
Enhanced Performance Features
Beyond its structural role, the evaporator frame section 712W61942-0065/1 contributes to acoustic management within the cabin environment. Vibration-dampening materials integrated into mounting interfaces reduce operational noise transfer, especially noticeable during blower fan operation at higher speed settings. Thermal isolation properties prevent heat soak from engine compartments from affecting refrigerant line temperatures. During field testing with haulage companies, trucks equipped with genuine 712W61942-0065/1 components demonstrated measurable improvement in average cooling efficiency compared to vehicles using compatible substitutes. The powder-coated finish enhances scratch resistance during installation while improving aesthetic continuity with factory-installed HVAC components. For technicians, the design incorporates tool-clearance zones around critical fastener locations, preventing stripped bolt heads or collateral damage during removal procedures. The 712W61942-0065/1 represents a worthwhile investment considering how many third-party equivalents require additional modifications or shimming to achieve proper alignment with existing ductwork and refrigerant connections.
Compatibility & Application
Verified across HOWO‘s extensive lineup of vocational and long-distance models, this evaporator frame 712W61942-0065/1 supports both basic manual climate systems and advanced digital control configurations. Fleet maintenance records indicate significantly lower failure rates when using this OEM component compared to pattern parts, particularly in refuse collection and construction applications where shock loads frequently test component resilience. The part cross-references to multiple regional numbering systems, but using the primary 712W61942-0065/1 identifier prevents fulfillment errors during ordering processes. International distributors maintain regional stocking facilities for rapid delivery, minimizing vehicle downtime during critical repair scenarios. When installing the 712W61942-0065/1, cleaning surrounding ducts before reassembly prevents contaminant migration into freshly replaced components. While most workshop environments can complete this installation without specialized equipment, having refrigerant recovery/recharge systems available avoids accidental discharges during connected work.
Maintenance Guidelines
Prolonging the service life of your 712W61942-0065/1 frame section involves periodic visual inspections during annual maintenance cycles. Check for any signs of abrasion where electrical harnesses contact structural edges, particularly along vibration-prone firewall boundaries. Unlike exposed underhood components, the protected cabin location generally shields this part from environmental debris, but accumulated dust can mask developing fractures around high-stress junctures. Manufacturers recommend replacing all factory-fitted mounting hardware during reinstallation procedures since thread integrity diminishes with thermal cycles and vibration exposure. For refrigeration technicians, the 712W61942-0065/1 design incorporates service ports positioned to prevent instrument line confusion during pressure diagnostics. When performing complete HVAC rehabilitation, replacing the frame simultaneously with evaporator core upgrades avoids the need for future compartment disassembly. Documentation accompanying every genuine 712W61942-0065/1 includes torque pattern sequences that maximize even clamping forces to prevent component warpage during temperature cycling.
Environmental & Efficiency Impact
Sustainability features engineered into the 712W61942-0065/1 include manufacturing processes utilizing recycled aerospace-grade alloys while still achieving military-grade specification compliance. This reduces embodied carbon metrics by over 30% compared to previous iterations, reflecting evolving industry sustainability standards. The design contributes to overall vehicle efficiency by optimizing refrigerant charge requirements through precise volumetric relationships between components. During independent lab testing, correctly installed 712W61942-0065/1 assemblies reduced compressor duty cycles by maintaining lower evaporator discharge temperatures across diverse operating conditions. Proper sealing along interface points also minimizes parasitic load on blower motors struggling against pressure losses from leak points common in worn components. Fleet-wide deployment of genuine 712W61942-0065/1 parts correlates with measurable reductions in cabin temperature stabilization times after ignition startup events, particularly important in climates where operator fatigue relates directly to thermal management delays.
Diagnostic Considerations
When HVAC performance degradation suggests possible evaporator system issues, inspecting the 712W61942-0065/1 frame section should precede core replacement. Warped mounting flanges can create air bypass conditions that mimic low refrigerant charge symptoms. Diagnostic steps should include checking all insulator pads between the frame and cabin firewall that deteriorate over time, causing vibration transfers into occupant compartments. Special attention should focus on condensation drainage ports integrated into the 712W61942-0065/1 base structure since blockages here create secondary moisture issues without triggering conventional system diagnostics. Thermal imaging serves as an effective non-invasive inspection method for identifying thermal bridges created when aftermarket components alter original isolation designs. Where fleet maintenance facilities document consistent premature failures of 712W61942-0065/1 units, possible chassis resonance frequencies causing harmonic vibration should be investigated rather than assuming material defects. Warranty validation requires preserving both the physical serial tag and installation documentation associated with each component.
Technical Highlights
- Material Composition: Reinforced aluminum-magnesium alloy matrix
- Surface Treatment: Multi-stage phosphate conversion coating
- Vibration Tolerance: Sustains 5Hz-200Hz oscillation frequencies
- Temperature Range: Certified for continuous operation (-40¡ãF to 220¡ãF)
- Design Life: Tested to 15,000+ operational hours
- Compliance Standards: ISO 16374:2018, IEC 61373:2010
Always verify component identification markings when sourcing replacements to ensure receipt of genuine 712W61942-0065/1 inventory. Never substitute mounting hardware with inferior equivalents that compromise clamping integrity under thermal cycling conditions.
Installation Best Practices
Professional replacement of the 712W61942-0065/1 evaporator frame requires comprehensive glove box and dashboard component removal, following OEM disassembly sequences to prevent costly plastic fastener damage. Retain clips and retainers in labeled organizer trays throughout the process. Clean mating surfaces thoroughly before fitting the new frame to eliminate debris that causes stress fractures from micro-movements. Apply dielectric lubricant to electrical connectors before engagement to prevent future corrosion that impedes signal integrity to blower controls. When routing lines through the 712W61942-0065/1 frame portals, maintain manufacturer-specified bend radii to prevent flow restrictions. Pressure test all refrigerant connections independently before system evacuation procedures to isolate potential leak points. Final commissioning should include full air-volume testing with static pressure measurements recorded against baseline values for future reference. Technicians report installation durations typically range between 3.5-5.5 hours depending on cab configuration complexity.
Performance Optimization
Achieving peak efficiency after installing the 712W61942-0065/1 requires calibrating blend door actuators according to manufacturer reset procedures. Verify temperature differentials across the evaporator coil consistently register between 15¡ãF-22¡ãF at medium blower speeds during post-repair validation. Consider installing aftermarket filtration upstream of the unit where vehicles operate in particulate-heavy environments, extending the service interval before core cleaning becomes necessary. Telematics data shows notable reductions in compressor clutch cycling frequencies when replacing worn frame assemblies due to stabilized airflow paths eliminating unnecessary temperature swings. Operators should note initial after-replacement noise levels typically reduce as new insulation pads compress during the 500-mile settling period. Document baseline system pressures during first service after frame installation for comparative diagnostics during future maintenance events. Remember that the 712W61942-0065/1 serves as a foundational component for the entire climate system – investing in its integrity affects multiple downstream performance metrics.