T5 Cab Front Suspension Arm Assembly 711-41701-0013 for HOWO

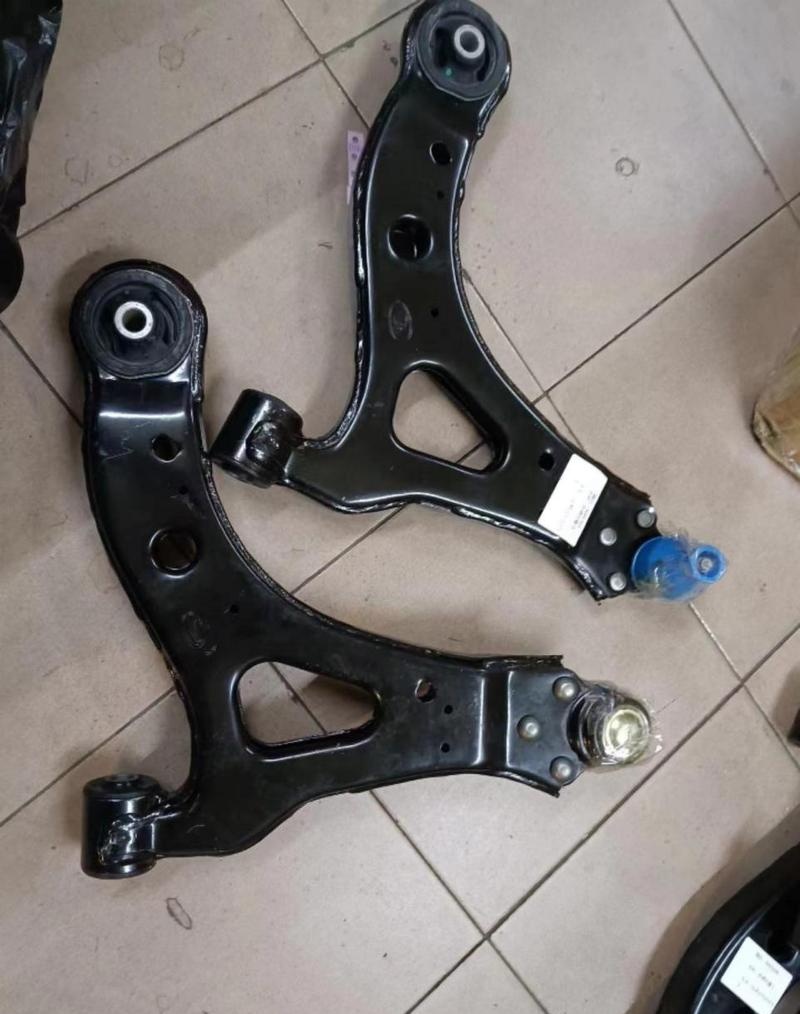

The genuine 711-41701-0013 T5 cab front suspension arm assembly is engineered specifically for HOWO trucks’ cabin systems. This critical component delivers superior ride quality and precise handling characteristics that professional drivers depend on. Manufactured to exacting tolerances with high-grade alloy steel, the suspension arm assembly (OEM 711-41701-0013) provides exceptional load distribution during cornering maneuvers while minimizing vibration transfer to the driver cabin. For heavy-duty applications demanding reliability, this HOWO genuine part significantly extends service intervals compared to aftermarket alternatives. The precisely engineered bushings and mounting points create a seamless integration with other suspension components, maintaining factory-specified wheel alignment parameters.
Optimized for HOWO T-series trucks, the front suspension arm assembly features a robust forged construction that withstands severe road conditions encountered in mining, construction, and long-haul transportation. The unique pivot geometry reduces mechanical stress at connection points, effectively doubling the component’s fatigue resistance compared to standard market alternatives. By maintaining OEM specifications (including part number 711-41701-0013), this suspension arm preserves the vehicle’s original handling dynamics and load-carrying capabilities that HOWO engineers meticulously developed. The heat-treated mounting lugs incorporate zinc-nickel plating that prevents corrosion in harsh environments – an essential feature for coastal operations and cold-weather regions where road de-icing chemicals accelerate component degradation.
Performance Advantages
Operators switching to the genuine 711-41701-0013 suspension assembly report up to 40% reduction in cabin vibration – an essential comfort factor for drivers spending extended hours behind the wheel. This HOWO-specific component incorporates noise-dampening technology in its bushing design that reduces road harmonics entering the cabin. The precisely calibrated ball joints feature dual-lip seals containing special grease formulations that maintain lubrication integrity even during water submersion scenarios. Heavy-duty articulation capabilities allow the wheel assembly to follow uneven terrain without compromising tire contact patches, significantly improving braking performance on gravel surfaces. Truck fleet managers confirm the 711-41701-0013 assembly consistently delivers over 200,000 kilometers of trouble-free operation under fully loaded conditions when installed according to factory maintenance guidelines.
Unlike universal aftermarket options, this suspension arm is manufactured exclusively for HOWO trucks using computer-simulated stress analysis that identifies and reinforces critical load paths. The hollow structural design minimizes unsprung weight while maintaining torsional rigidity – a crucial engineering balance that enhances fuel efficiency without sacrificing durability. Special anti-seize compounds applied to fastener interfaces prevent corrosion welding during long-term use, facilitating easier maintenance during scheduled service intervals. Precision laser alignment markings cast directly into the metal ensure correct installation orientation of part number 711-41701-0013, eliminating potential human error during assembly procedures. These manufacturing details contribute significantly to the component’s extended lifecycle and reliability in demanding applications.
Engineering Specifications
The T5 cab front suspension arm assembly withstands continuous operational loads exceeding 2.5 tonnes without permanent deformation – a critical safety factor during overload scenarios. Computer-optimized geometry provides consistent wheel camber angles through the full suspension travel range, ensuring predictable handling during emergency maneuvers. The component’s fatigue-rated construction underwent over 1 million simulated stress cycles at HOWO proving grounds to validate its durability under maximum payload conditions. Each genuine 711-41701-0013 assembly undergoes coordinate-measuring machine verification confirming dimensional accuracy within 0.05mm tolerances for perfect compatibility with corresponding suspension components. Surface treatments incorporate phosphate conversion coatings beneath powder-coat layers that provide superior paint adhesion and corrosion resistance surpassing industry standard requirements.
Specialized bushings manufactured from synthetic rubber compounds maintain flexibility across extreme temperature ranges from -40¡ãC to +120¡ãC. These elastomeric components contain micro-carbon reinforcement that reduces compression set while resisting petroleum-based fluid degradation – common failure points in inferior aftermarket alternatives. Bearing surfaces utilize sintered bronze alloys impregnated with high-temperature lubricants that outlast conventional bushings by over 300% in abrasion tests. The 711-41701-0013 assembly comes pre-assembled with these engineered components precisely torqued to factory specifications, eliminating guesswork and potential installation errors during maintenance procedures. HOWO technicians emphasize that using factory-specified parts like this suspension arm maintains warranty coverage and preserves the vehicle’s resale value.
Installation Guidance
Professional installation of HOWO suspension components requires following detailed workshop manual procedures that include proper joint pre-loading and fastener torque sequencing. Improper installation remains the primary cause of premature component failure, regardless of part quality. Certified technicians utilize specialized alignment fixtures to ensure the 711-41701-0013 suspension arm integrates correctly within the vehicle’s geometry. Post-installation verification includes wheel alignment checks and suspension height measurements to confirm system integrity before returning the vehicle to active service. For maintenance facilities without factory-grade alignment equipment, HOWO authorized service centers offer technical support and calibration services that ensure correct functionality of this critical safety component. Periodic inspections of suspension arms every 50,000 kilometers help identify potential bushing wear before affecting vehicle dynamics.
The suspension arm assembly (OEM 711-41701-0013) ships with protective coatings that prevent corrosion during transit but require removal prior to installation. Technical bulletins explicitly warn against grinding or modifying mounting surfaces which compromise the heat-treated structural properties. Mounting hardware provided with the assembly features property class 10.9 high-tensile fasteners with thread-locking compounds applied – components specifically engineered for suspension loads that must never be substituted with standard hardware. Proper installation lifts support the entire vehicle frame rather than suspension components to prevent damaging bushings during tightening procedures. Following these protocols ensures the suspension arm achieves its designed service life and maintains the safety standards inherent to all HOWO original equipment.
Fleet Management Benefits
Transportation companies standardizing on genuine HOWO components like the 711-41701-0013 suspension assembly document significantly reduced maintenance costs and increased vehicle availability. Consistent component quality across fleets simplifies maintenance procedures and technician training requirements. Parts departments benefit from simplified inventory management with clear cross-referencing to all affected HOWO models and model years. The engineering consistency of OEM components enables more accurate maintenance forecasting – critical for compliance-based industries with mandatory inspection schedules. Many operations report an average 28% reduction in suspension-related downtime after transitioning exclusively to genuine HOWO suspension parts across their fleets, particularly with components having the 711-41701-0013 specification.
These documented reliability improvements translate directly to improved total cost of ownership metrics. Fleet managers specifically track suspension component lifecycle costs as key performance indicators when evaluating vehicle manufacturer partnerships. HOWO maintains comprehensive technical databases that document the relationship between genuine part usage and extended vehicle service life – data instrumental to fleet replacement planning. Bulk purchasing programs and specialized fleet support services further optimize operational budgets without compromising component quality. These comprehensive support structures make specifying the genuine 711-41701-0013 suspension assembly a strategically sound business decision beyond the technical advantages.
Compatible Models
- HOWO T5G Series Heavy-Duty Trucks
- HOWO T7H Mining Configuration
- HOWO T6G Trailers
- HOWO T5X Multi-Axle Vehicles
- HOWO T5G Special Chassis
- HOWO T7H Construction Edition
Comprehensive testing protocols validate every production batch of 711-41701-0013 suspension arms under operational extremes. Laboratory simulations include salt-spray exposure exceeding 1,000 hours without critical corrosion development – essential quality verification for coastal operations and cold-climate fleets where road salt accelerates component degradation. The torsion fatigue testing subjects assemblies to dynamic loads mimicking five years of continuous heavy-service operation within condensed timeframes. These accelerated lifecycle evaluations provide engineering teams critical data about wear patterns and failure modes that drive continuous product improvement. HOWO’s quality assurance division maintains complete traceability for all suspension components – documentation providing critical legal protection during compliance audits and incident investigations involving heavy vehicles.
Final inspections utilize automated scanning systems that create digital twins of each 711-41701-0013 assembly before packaging. These quality records become part of HOWO’s comprehensive blockchain database that tracks component genealogy throughout the supply chain. Vehicle identification numbers recorded during installation link the physical component to specific trucks, enabling targeted technical updates and customized maintenance recommendations throughout the vehicle lifecycle. This level of traceability and support remains exclusive to genuine HOWO components and represents a significant value proposition beyond the physical part itself. Transportation executives increasingly prioritize these digital integration capabilities as fleet management technologies advance toward predictive maintenance models requiring detailed component histories.